How to Implement Driverless Forklifts in Your Warehouse
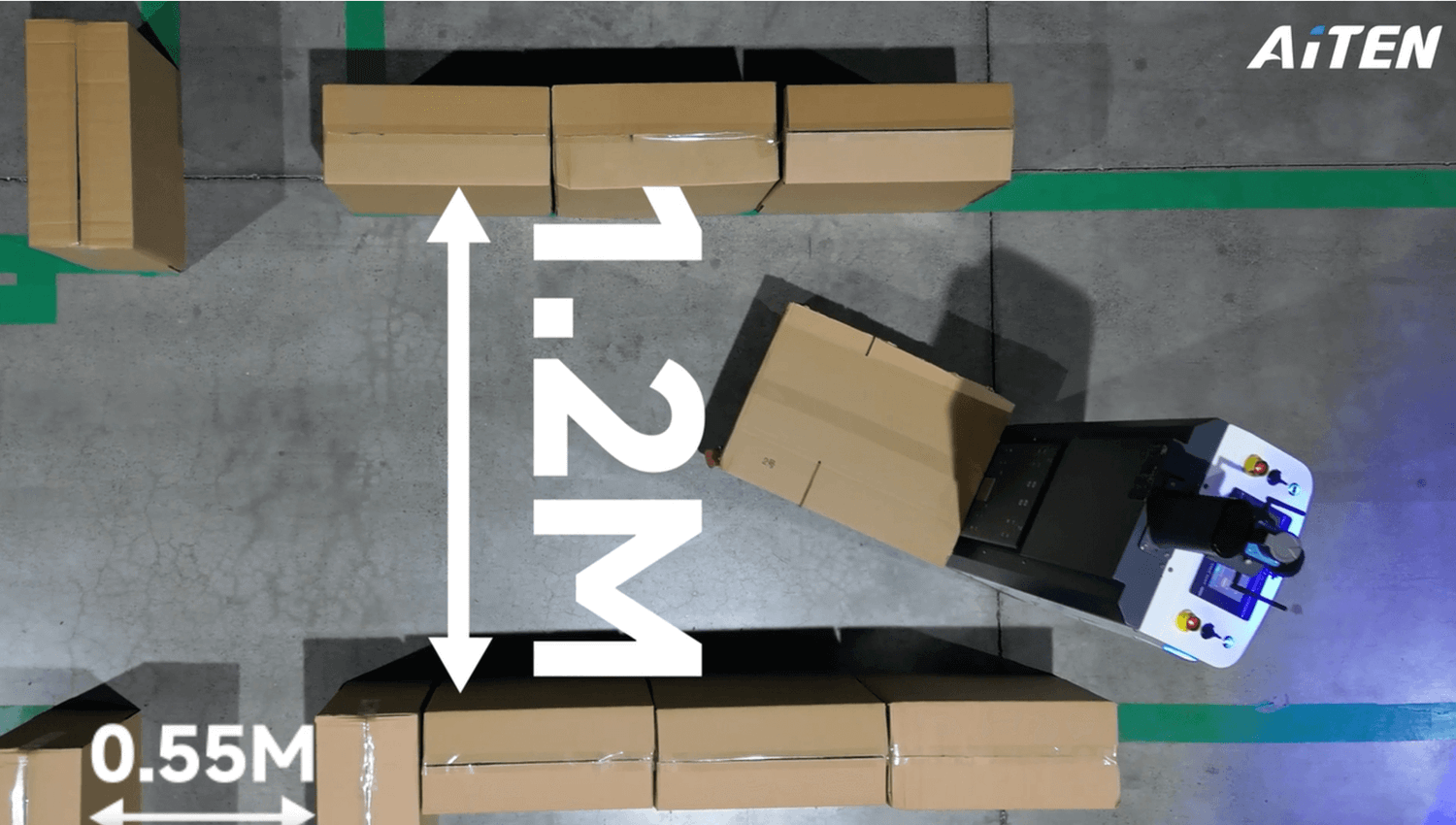
Integrating driverless forklifts into your warehouse operations can transform efficiency, but success depends on a strategic, step-by-step approach. This article will guide to ensure a smooth transition.
1. Assess Your Warehouse Needs & Layout
Start by mapping your current workflows:
- Task Analysis: Identify repetitive tasks (e.g., pallet stacking, cross-warehouse transfers) that driverless forklifts can automate. Prioritize high-volume, low-complexity tasks first.
- Layout Evaluation: Check for narrow aisles (<2m), floor conditions and obstacle density. Driverless forklifts with laser SLAM navigation thrive in dynamic environments, but mapping fixed obstacles (columns, racks) upfront streamlines programming.
- Load Requirements: Match forklift specs to your needs - payload capacity, lifting height, and battery runtime (8+ hours for 24/7 shifts).
2. Choose the Right Technology & Partner
Not all driverless forklifts are equal. Focus on:
- Navigation Systems: Laser SLAM (flexible, no infrastructure changes) vs QR code (high precision, ideal for fixed paths). For mixed-use warehouses, hybrid systems offer the best of both.
- Integration Capabilities: Ensure the forklift’s software connects with your WMS/MES systems via APIs. Real-time data sync (e.g., inventory updates, task status) is critical for seamless operations.
- Vendor Support: Select partners with local service teams. Post-implementation training and 24/7 technical support minimize downtime during the transition.
3. Pilot Testing in a Controlled Zone
Before full deployment:
- Start Small: Dedicate a 500-1,000 sq.m zone for 2-4 weeks. Test tasks like pallet retrieval and dock-to-rack transfers.
- Measure KPIs: Track metrics like task completion time, collision rates, and energy usage. Compare results to manual operations to validate ROI.
Driverless forklifts vs manual forklifts in warehouse environments
- Gather Feedback: Involve warehouse staff to identify usability issues (e.g., interface clarity, emergency stop responsiveness). Their input ensures adoption.
4. Scale Gradually & Train Your Team
- Phased Rollout: Expand to 2-3 zones after successful piloting, increasing the fleet size by 10-20% monthly. This avoids overwhelming your systems.
- Training: Equip staff to monitor, troubleshoot, and reroute forklifts via the control dashboard.
- Continuous Optimization: Use fleet management software to analyze data - adjust routes to reduce congestion, schedule charging during off-peak hours, and update task priorities based on demand spikes.

5. Validate ROI & Iterate
Calculate long-term benefits:
- Cost Savings: Reduced damage to goods and equipment adds to savings.
- Efficiency Gains: 24/7 operation and consistent speed boost throughput by 30-50% in high-volume facilities.
- Scalability: Easily add units during peak seasons (e.g., Black Friday) without hiring temporary staff.
AiTEN’s cases:
結論
Implementing driverless forklifts isn’t just about technology - it’s about aligning automation with your unique workflows. By starting with a clear assessment, choosing flexible systems, and scaling thoughtfully, you’ll unlock safer, more efficient operations that adapt to future growth.
Ready to start? Contact us for a free warehouse assessment tailored to your driverless forklift needs.