How Autonomous Forklifts Improve Warehouse Efficiency?
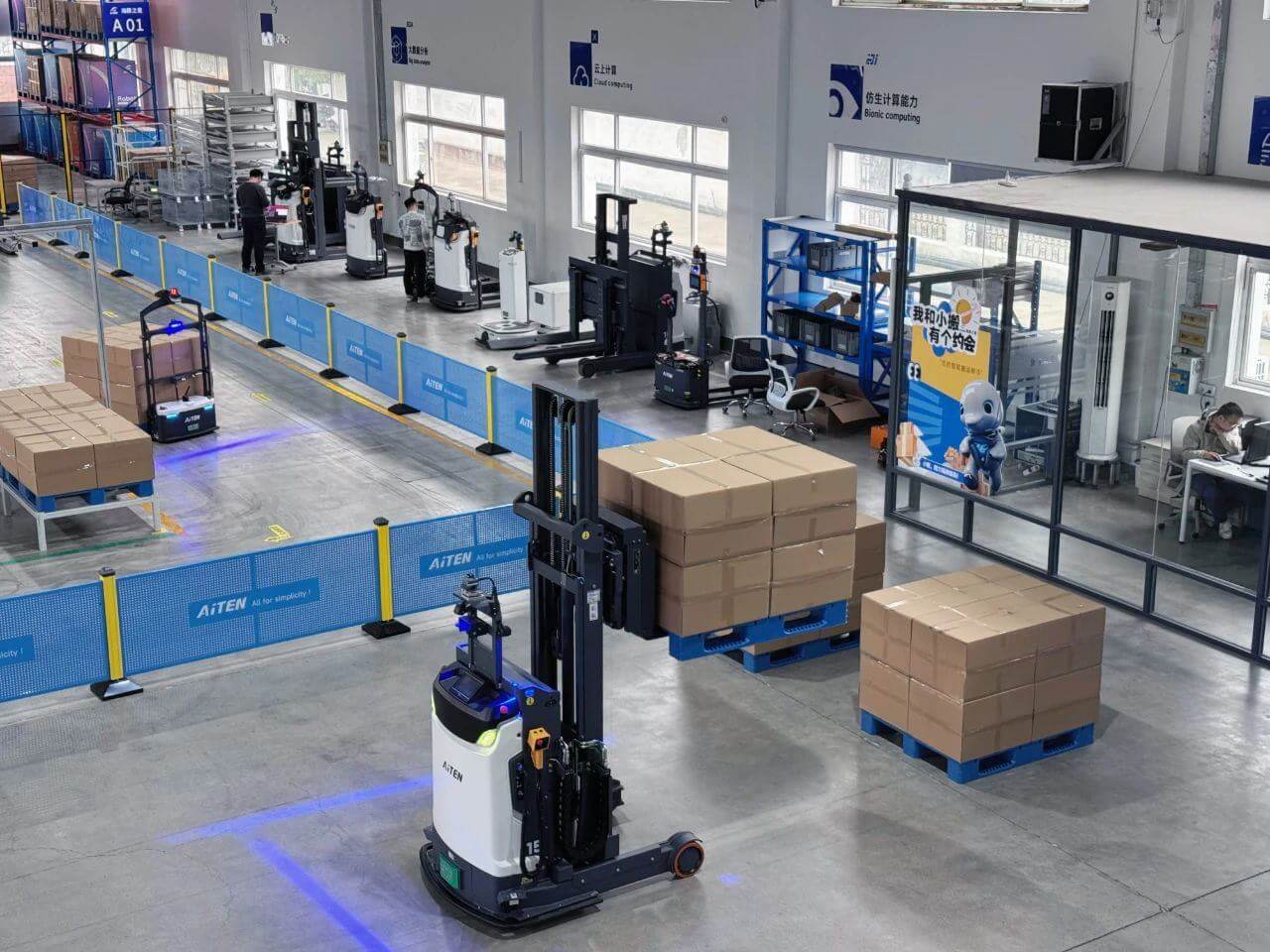
As supply chain demands increase and labor shortages persist, autonomous forklifts—also known as self-driving or robotic forklifts—are becoming an essential tool for warehouse optimization. These smart machines offer a reliable solution to improve productivity, enhance safety, and reduce operational costs.
Whether you are a logistics provider or a manufacturing company, automating certain processes can improve productivity. This can be achieved by gradually automating individual processes or by completely transforming the systems of large companies.
In this article, we explore how autonomous forklifts significantly boost warehouse efficiency and why forward-thinking businesses are investing in this game-changing technology.
Key Advantages of Automatic Forklifts
Autonomous forklifts offer numerous advantages over traditional manual forklifts, particularly in terms of improving warehouse operational efficiency and productivity. One study found that facilities deploying these advanced machines saw a 30% increase in productivity metrics, highlighting their potential to transform the warehousing industry.
1. Reduced Labor Dependency
The logistics industry is currently facing a serious labour shortage, and automated systems play an indispensable role in filling this gap. Automation provides a viable solution by taking on repetitive, physical tasks that were traditionally performed by humans.
Traditional forklifts require skilled human drivers. However, rising labor costs and worker shortages have made staffing a constant challenge. Autonomous forklifts operate without human intervention, enabling 24/7 operation without breaks, fatigue, or scheduling conflicts. This leads to:
- Consistent material flow
- Lower reliance on manual labor
- Faster ROI on automation investments
Numerous case studies show that companies have successfully deployed automation technology to alleviate labour shortages and maintain operational efficiency despite labour shortages. In addition, automation enables organizations to reallocate human resources so that your employees can handle more complex, value-added tasks.
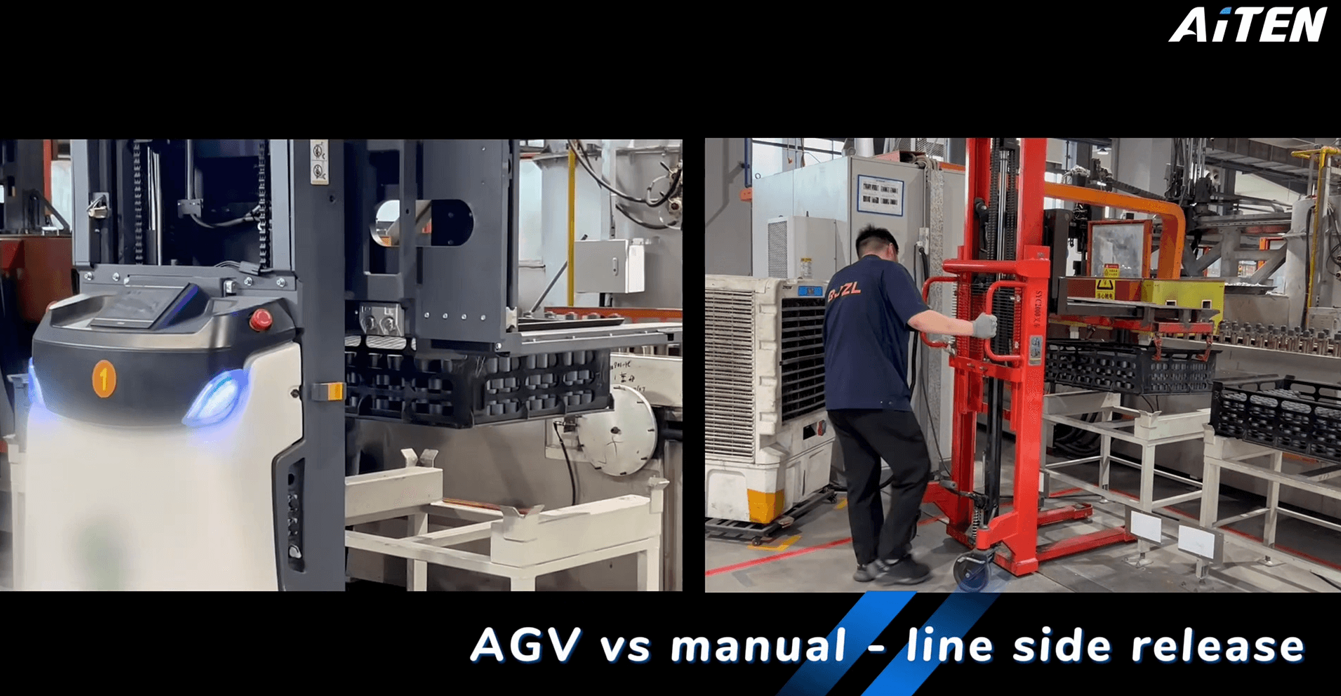
2. Increased Accuracy and Fewer Errors
One of the major advantages of autonomous forklifts is their ability to follow precise routes and handle loads consistently. By using advanced sensors, cameras, and real-time mapping technologies, these forklifts reduce:
- Product damage due to mishandling
- Incorrect pallet placement
- Inventory count errors
The result is improved inventory accuracy and streamlined fulfillment.
3. Enhanced Safety in the Workplace
The safety enhancements offered by autonomous forklifts are noteworthy, as these machines significantly reduce the incidence of human error in complex warehouse environments. With advanced obstacle detection and emergency stop functions, autonomous systems have revolutionised safety protocols and dramatically reduced accident rates.
Unfortunately, warehouse accidents caused by traditional forklifts are all too common. Automated forklifts are equipped with advanced safety laser scanners that can detect any obstacles and stop when necessary. Even during close-range operations, they ensure a safe working environment.
Warehouses adopting autonomous technology have reported a significant reduction in workplace accidents, with some facilities seeing a decrease in accident rates of up to 40%. These safety measures, combined with continuous monitoring capabilities, not only ensure more efficient warehouse operations but also provide a safer environment for all personnel involved.
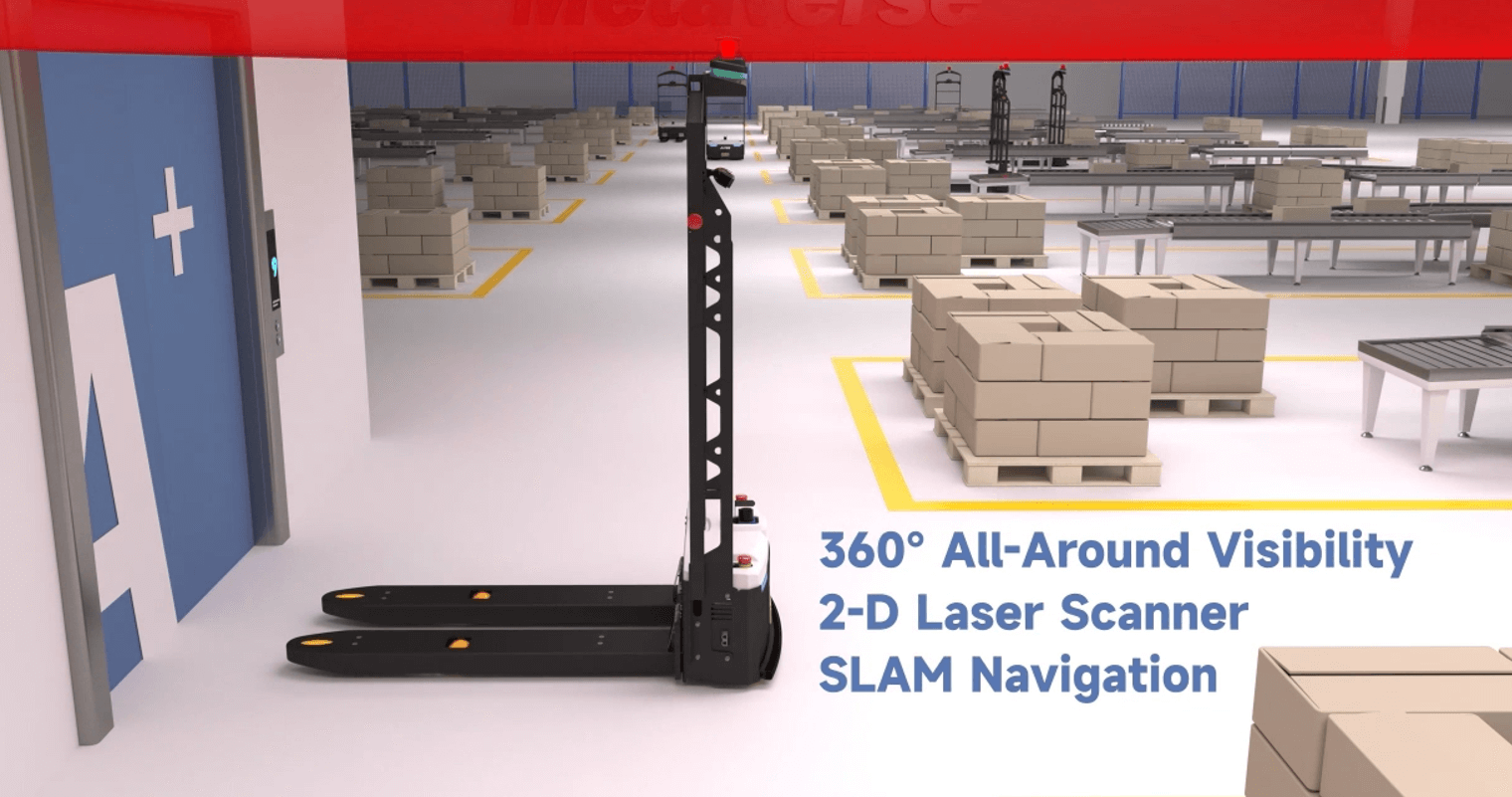
4. Optimized Workflow and Throughput
Automation helps to achieve consistent workflows and efficient driving behaviour. Intelligent order and fleet software minimises transport distances and avoids vehicle congestion, thereby improving your operational efficiency around the clock.
Autonomous forklifts integrate with Warehouse Management Systems (WMS) and Manufacturing Execution Systems (MES) to dynamically adapt to workflow changes. Benefits include:
- Intelligent task prioritization
- Route optimization to avoid congestion
- Synchronization with other automated equipment
Such integration leads to higher throughput and reduced downtime.
Warehouse managers will appreciate robot forklifts for helping them increase storage capacity and efficiently utilise space. Once the retrieval process is automated, you can speed up shipping and reduce inventory backlogs in storage spaces.
5. Scalability and Flexibility
Whether scaling up during peak seasons or adapting to layout changes, autonomous forklifts offer unmatched flexibility. Modern models can:
- Navigate narrow aisles and dynamic environments
- Handle a variety of load types (pallets, racks, containers)
- Be redeployed with minimal configuration changes
This makes them ideal for growing businesses and multi-shift operations.
6. Lower Operational Costs
Though initial investment may be significant, autonomous forklifts reduce long-term costs by:
- Eliminating overtime pay
- Reducing training and onboarding expenses
- Minimizing equipment downtime and maintenance
These savings contribute directly to the bottom line.
Real-World Applications
Industries adopting autonomous forklifts include:
- E-commerce warehouses (faster fulfillment)
- Automotive manufacturing (just-in-time material delivery)
- FMCG distribution centers (high-volume pallet handling)
- Cold storage (harsh environment automation)
Case studies:
效率提升 40%:AiTEN Robotics 在發動機製造公司的創新應用
智慧型排程系統與 AGV 機器人讓倉儲效率提升 60%,並實現零工傷突破
Which Parts of Your Operations Can be Automated?
Imagine all the repetitive goods handling in a warehouse. Automation can be implemented in the following areas:
- Long-distance pallet transport: Heavy-duty horizontal transport between workstations
- Block stacking: Block stacking for compact storage
- High-bay warehousing: Storing and retrieving goods at high elevations
- Towing: Timely delivery of parts between workstations
- High-density storage: Shelf pallet transport
Interested in applying this lean approach to your organization? Learn more about automation today and explore how you can benefit from AiTEN Robotics' extensive automation solutions.
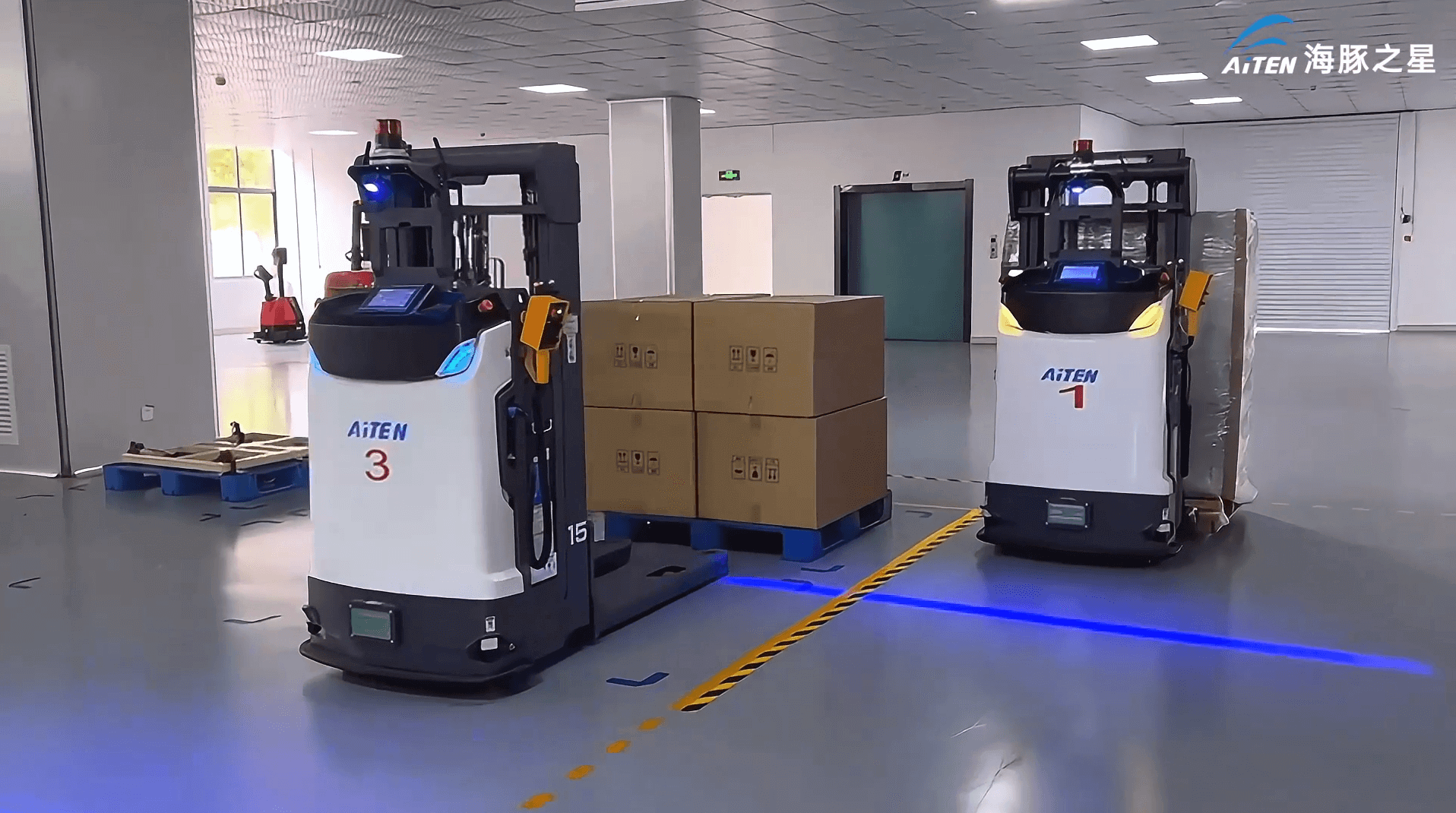
The Future of Automated Forklift Warehouses
Automated forklift warehouses represent a revolutionary leap forward in warehouse efficiency and safety. By automating traditional manual tasks, these systems offer significant advantages in terms of increased productivity, reduced costs, and enhanced safety. While implementation may present challenges, the long-term benefits make automated forklift warehouses an essential component of modern logistics and supply chain management. As technology continues to advance, the role of automated forklift warehouses in shaping the future of warehousing will undoubtedly grow increasingly important.
Additionally, infrastructure upgrades may include expanding charging stations and advanced communication systems to effectively manage larger fleets. In the future, we will focus on creating more adaptable and scalable automated systems to meet the needs of large distribution centres.
總結
Autonomous forklifts are more than just a technological trend—they are a strategic investment in operational excellence. By improving accuracy, safety, and speed, they redefine what’s possible in modern warehouse management.
For businesses aiming to stay competitive and future-ready, integrating autonomous forklifts is no longer optional—it's essential.
Why Choose AiTEN to Meet Your Automated Forklift Needs?
AiTEN Robotics is a global leader in autonomous industrial vehicles (AMR/AGV) and logistics automation solutions. AiTEN Robotics has developed ten product series to meet the needs of full-stack material handling scenarios. AiTEN Robotics has deployed more than 200 projects in over 30 countries and regions, and is trusted by numerous Fortune 500 companies across industries such as automotive, food and beverage, chemicals, pharmaceuticals, manufacturing, and third-party logistics, enhancing operational safety, efficiency, and future readiness.
Contact AiTEN to learn how our innovative autonomous forklifts and intelligent systems can transform your material handling processes.