Forklift Robot Pallet Positioning Technology: The Key to Accurate Handling
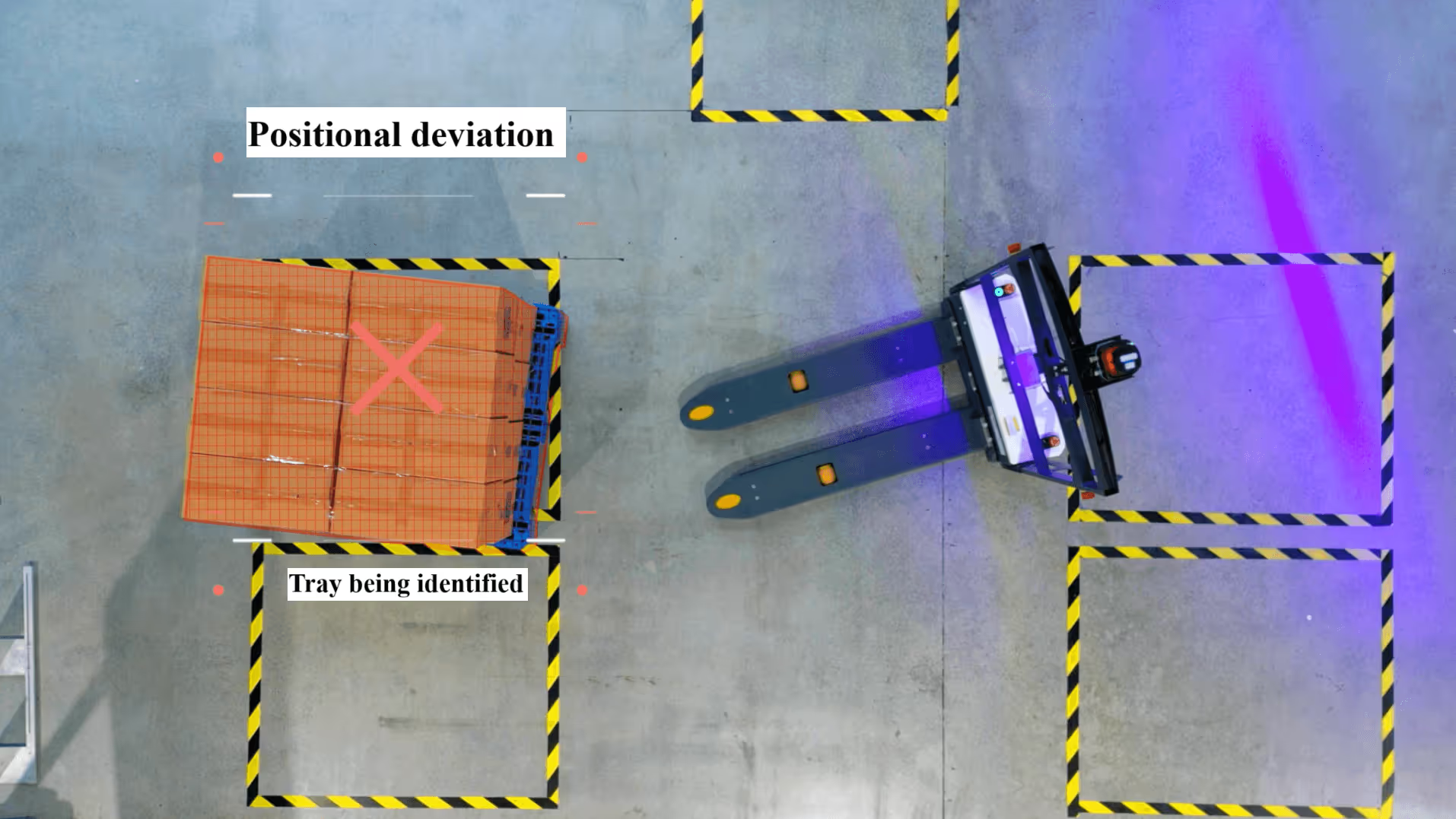
With the accelerated development of intelligent logistics and intelligent manufacturing, intelligent transformation has become a key path to improve efficiency and reduce costs. Forklift robots (AGV/AMR forklift) are increasingly widely used in warehousing, manufacturing, retail and other industries.
Among them, pallet positioning technology is one of the core links to achieve efficient and stable operation, and the accuracy and reliability of this technology directly determine the overall operating efficiency of the automated logistics system. In this paper, we will analyze the principle of forklift robot pallet positioning technology, the key technology path, and the advantages and challenges in practical applications.
What is Forklift Robot Pallet Positioning Technology?
Forklift robot pallet positioning technology refers to the ability of the robot to accurately identify, dock and fork the pallet in the handling operation. It involves pallet spatial position identification, attitude judgment, dynamic adjustment and path optimization and other aspects, which directly affect the handling efficiency and operational safety.
In short, it is the process of forklift robots utilizing advanced sensors and intelligent algorithms to automatically identify the position and attitude (direction and tilt angle) of the pallet and accurately align the pallet in a complex and dynamic warehouse environment. The goal is to ensure that the fork tines can be inserted into the pallet jack safely, stably and efficiently.
Why is “Pallet Positioning” Important?
Logistics and warehousing environments are becoming increasingly complex, with a wide variety of goods, different pallet specifications, and operational scenarios that require high efficiency and accuracy.
A pallet is the smallest handling unit in warehousing logistics. If the forklift robot (including AGV/AMR) can not quickly and accurately find the hole position of the pallet, there will be problems such as fork deviation, falling, and secondary adjustment, which will directly affect the return on investment. Therefore, high-precision, low-delay pallet positioning technology has become the key bottleneck for the large-scale landing of unmanned forklifts.
- Safety First: Positioning deviation may cause forklift robots to hit pallets, shelves or other equipment and facilities, and even cause cargo overturning or personnel injury risk.
- Efficiency: Accurate positioning means that forklift robots can quickly and accurately complete the fork picking or placing in one place, avoiding repeated adjustments and wasting time, significantly improving the efficiency of logistics operations.
- Stable and Reliable: The automation system needs to ensure the stable and reliable output of each operation, and accurate positioning is the foundation and prerequisite for unmanned forklift trucks to continue to operate efficiently.
- Reduce Human Intervention: Frequent human intervention in automated warehouses means that the value of automation cannot be truly released, and accurate positioning is a necessary condition to ensure the continuous operation of full automation.
At the same time, accurate pallet positioning helps to optimize the use of warehouse space and achieve high-density storage of goods through accurate stacking operations.
The Mainstream Pallet Positioning Technology Path
According to different application scenarios and accuracy requirements, the current forklift robots mainly use the following types of pallet localization technology:
1. LiDAR + SLAM map building localization
- Principle: Based on 2D or 3D LiDAR to build the environment map and real-time positioning of the forklift robot itself, combined with the pallet contour recognition for accurate positioning.
- Advantages: does not rely on environmental markers, strong adaptability.
- Application Scenario: Medium and large warehouses, industrial workshops.

2. Visual Recognition (RGB/Depth Camera)
- Principle: Acquire image or depth information through a camera to recognize pallet jacks, labels or profile edges.
- Advantage: High accuracy, suitable for complex pallet identification, such as mixed European/American standard pallets.
- Challenges: Sensitive to light, requires high-performance image algorithm support.
3. QR code/reflector + navigation marking positioning
Principle: Set up QR code, reflective markers and other auxiliary signs on the pallet or cargo space to improve positioning stability.
- Advantages: reliable positioning, low implementation cost.
- Applicable scenarios: fixed goods warehouse, production line, the line docking.
4. Multi-sensor fusion localization
- Principle: Fusion of LIDAR, vision, IMU, ultrasonic and other sensors to achieve highly robust localization.
- Advantage: to cope with the challenges of occlusion, light changes, complex paths, etc..
- Trend: the mainstream direction of high-end forklift robot development.
Schematic Diagram of the Pallet Positioning Process
- Navigate to the target location - Use a map or fixed path navigation system to guide the forklift to the vicinity of the pallet.
- Pallet Positioning - Identify the center and attitude of the pallet in real time through sensors to determine the position of the jack.
- Attitude Adjustment and Insertion - The system controls the forklift arms to make fine adjustments to accurately insert and lift the pallet.
- Handling and Unloading - Combined with target point navigation, the system completes the handling task and unloads the pallet safely.
Common Challenges and Optimization Directions
Despite significant progress in pallet positioning technology for forklift robots, there are still some challenges in practical applications.
First, the diversity of pallets is a major problem. pallets used by different industries and enterprises differ in size, shape, material, etc., which brings challenges to the versatility of positioning technology. For example, some special industries may use customized pallets, which are difficult to adapt by traditional positioning techniques.
Secondly, the complex operating environment also puts positioning technology to the test. There may be insufficient light, more dust, and blockage of goods in the warehouse, which affects the accuracy and stability of positioning.
To cope with these challenges, on the one hand, AiTEN R&D staff continuously optimize the positioning algorithm and improve its adaptive ability so that it can handle different types of pallets. For example, a multimodal data fusion approach is used to fuse and analyze data from multiple sensors, such as vision and LiDAR, to more accurately identify and locate pallets.
On the other hand, the improvement of hardware equipment is enhanced to improve the anti-interference ability of the equipment. For example, develop cameras with higher resolution and noise resistance, and LiDAR that can work stably in harsh environments. Meanwhile, by establishing a pallet database to store and manage the characteristics of different types of pallets, the system can quickly match and identify new pallets when they are encountered, improving the accuracy and efficiency of positioning.
Future Trends in Pallet Positioning Technology
In the future, forklift robot pallet positioning technology will develop in the direction of more intelligent, accurate and efficient. With the continuous progress of artificial intelligence technology, the deep learning model will be more intelligent, capable of automatically learning and adapting to a variety of complex pallet and environmental conditions, further improving the accuracy and speed of positioning. At the same time, multi-sensor fusion technology will be more widely used to realize all-around, high-precision positioning of the pallet through the deep fusion of data from a variety of sensors, such as vision, LiDAR, ultrasonic and so on.
- AI deep empowerment: Deep learning will play a greater role in target detection, attitude estimation, and abnormality processing, and improve the level of intelligence.
- Multimodal fusion deepening: Laser, vision, radar, IMU and other sensor fusion algorithms will be more intelligent.
- Standardization and modularity: Positioning technology interfaces and solutions will tend to be standardized and modularized for easy integration and deployment.
- Increasing anti-jamming performance: Improving the positioning stability in complex lighting, dust, pallet deformation, partial occlusion and other industrial scenarios is the key to improving the value of the system on the ground.
Positioning technology will be more deeply integrated with other functions of forklift robots, such as path planning, obstacle avoidance, etc., to realize the whole process of intelligent operation of forklift robots, and provide stronger technical support for the intelligent development of the logistics and warehousing industry.
總結
Pallet positioning technology directly determines the robot's execution ability, operational safety and operational efficiency level in complex industrial environments. With the development of AI, perception and control technology, the pallet positioning ability of forklift robots will continue to improve, helping enterprises to take a firmer step on the road to cost reduction and efficiency.
About AiTEN Robotics
As a company specialising in intelligent logistics solutions, AiTEN Robotics has consistently focused on the ‘smart factory’ scenario, deeply integrating technological innovation with industry needs. It has provided comprehensive services to over 200 manufacturing clients worldwide: Leveraging a full range of material handling robot product portfolios to cover diverse material handling scenarios, we have developed an industry-grade intelligent scheduling system to enable efficient collaboration among multiple devices. Through a comprehensive lifecycle service system spanning pre-sales planning, deployment and implementation to operations optimisation, we empower enterprises to achieve logistics intelligence transformation, continuously driving the digital upgrading and high-quality development of the manufacturing industry.
Contact us to explore automation solutions for your factory.