Guide to AGV Forklift Systems: Redefining Smart Factory Logistics
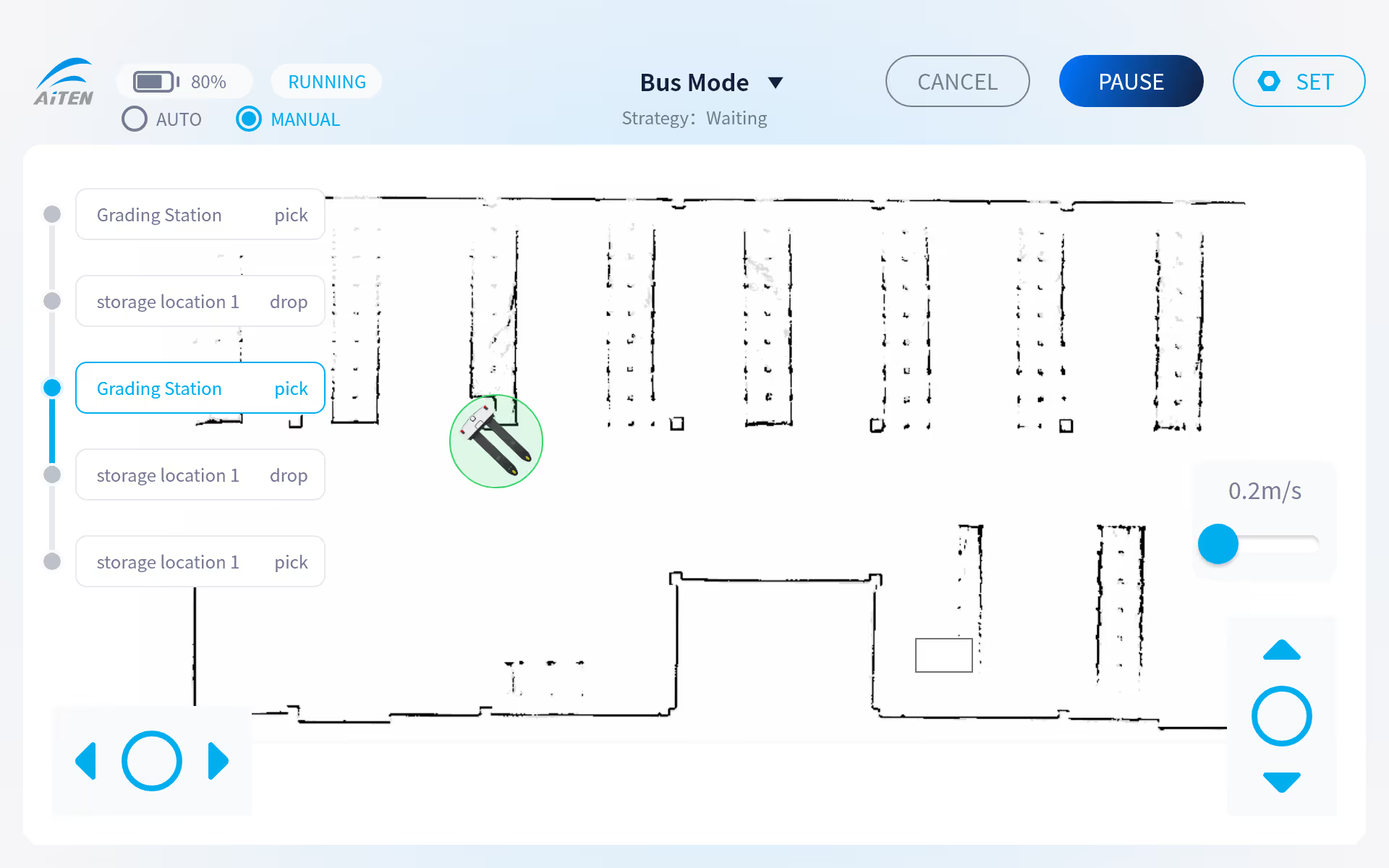
In the wave of intelligent manufacturing transformation and upgrading, the AGV (automatic guided vehicle) unmanned forklift system has evolved from a single device into a full-chain intelligent handling solution. This complex system, which integrates hardware architecture, software algorithms, and scenario adaptation, is redefining the boundaries of logistics efficiency in factories and warehouses with its ‘perception-decision-execution’ closed-loop capabilities.
System Architecture
1. Hardware Layer: Modular Intelligent Carriers
- Mobile platforms: Typical models include AiTEN Robotics' APx20 double-sided pallet forklift, TP100 robot, and ARV15 omnidirectional transport and stacking robot, all featuring powerful lifting capabilities.
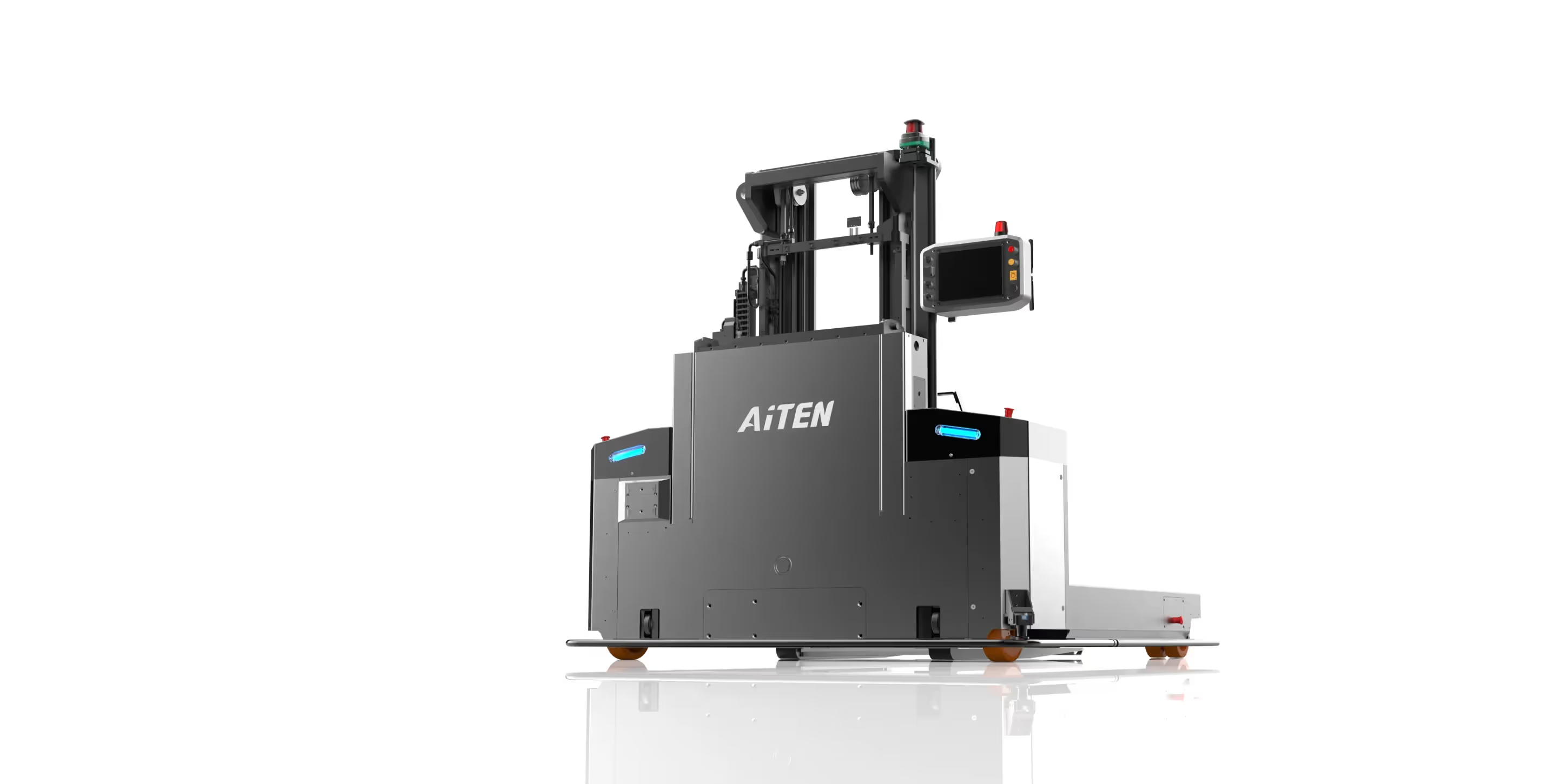
- Perception system: Multi-sensor data, including lidar (precise ranging but susceptible to interference from strong light), visual cameras (object type recognition, limited in low-light conditions), and ultrasonic sensors (close-range blind spot detection), complement each other's shortcomings and enhance obstacle recognition accuracy.
AGV(무인운반차) 실시간 장애물 회피 기술을 위한 다중 센서 융합
- Energy module: Lithium iron phosphate batteries support 30-minute fast charging, combined with a smart battery swap station design, to enhance endurance and enable 24-hour continuous operation.
2. Software layer
- Cluster management system: Based on reinforcement learning algorithms, it can simultaneously dispatch more than 100 AGVs and automatically avoid route conflicts. The AiTEN RDS dispatch system uses efficient intelligent algorithms and intelligent management functions to accurately configure logistics resources and efficiently dispatch various tasks. Whether it is internal warehouse goods transportation or cross-regional logistics distribution, it can ensure accuracy and reduce congestion to less than 0.5%, while increasing multi-machine collaboration efficiency by 35%.
- Task allocation engine: After integration with the WMS (Warehouse Management System), it can optimise routes in real time based on order priority, equipment load, and other parameters. AiTEN's WCS (Warehouse Control System) seamlessly integrates with peripheral equipment such as automatic doors, elevators, and conveyor lines, deeply integrating with the scheduling system to precisely transmit control commands to the core control system. This promotes the automation of integration processes, achieving higher-level intelligent collaboration and efficient operations between devices, laying a solid foundation for the construction of smart factories.
- Data visualisation platform: Utilising digital twin technology with real-time simulation at its core, the platform precisely monitors logistics operations. Through three-dimensional real-time simulation, it provides an intuitive experience of AGV operational status, assisting enterprises in optimising decision-making, enhancing efficiency, and reducing costs, thereby creating an efficient and intelligent logistics automation solution.
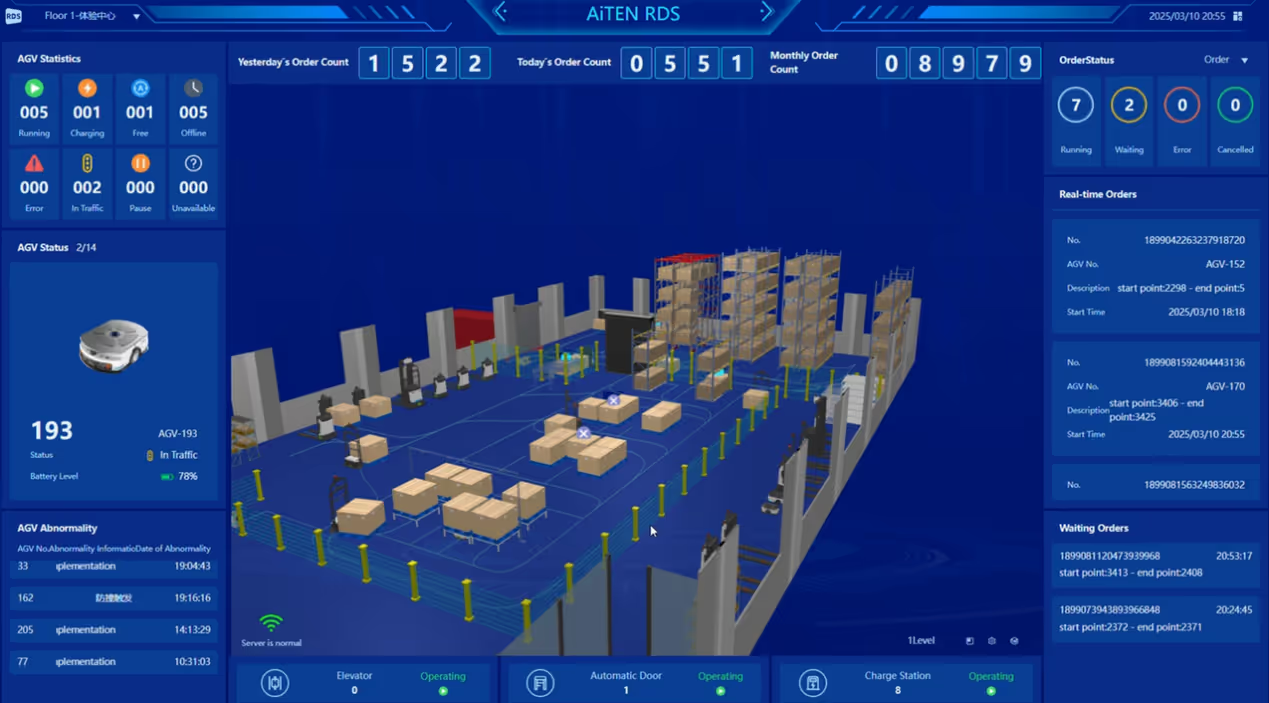
핵심 기술
- Dynamic Navigation and Positioning
Utilising laser SLAM + UWB hybrid navigation, millimetre-level positioning is achieved in indoor environments without GPS through environmental feature matching.
- Multi-vehicle Collaboration Algorithm
Drawing inspiration from ant colony optimisation principles, AGV clusters can autonomously negotiate task allocation, such as automatically adjusting priorities during peak hours to reduce downtime caused by material shortages.
- Safety Redundancy Design
Hardware-wise, collision-avoidance sensors and emergency stop buttons are installed. Software-wise, AI behaviour prediction algorithms reduce obstacle detection response time to within 0.3 seconds.
Scenario-based Applications
- E-commerce intelligent warehousing: In the ‘goods-to-person’ picking scenario, the AGV system works with sorting robots to achieve a processing efficiency of 2,000 orders per hour, which is five times higher than manual picking.
- Automotive flexible manufacturing: An AGV system deployed by a new energy vehicle manufacturer has achieved material data digitisation and full-process automation in the production process, ensuring a delivery accuracy rate of 99.99%, a 35% improvement in management efficiency, and a 30% increase in warehouse space utilisation.
물류 관리가 혼란스러운 자동차 공장의 창고 활용도를 30% 향상시킨 AiTEN의 맞춤형 솔루션
- Low-temperature cold chain delivery: Low-temperature-resistant AGVs and dispatching systems enable a smooth transition from traditional to intelligent operations in food cold storage facilities. Once a robot has completed its task, if there are no new tasks assigned, it will automatically proceed to the charging area to recharge. This ensures that it is always ready for action while reducing energy consumption costs.
Cold Storage in Spain-AE15 Intelligent Unmanned Forklift Robot Application Example
결론
The value of AGV unmanned forklift systems has long transcended the scope of ‘automated handling tools,’ becoming intelligent nodes that connect factory equipment and break down data barriers. For manufacturing and logistics companies, choosing an AGV system solution with full-stack technical capabilities is not just about introducing a set of equipment, but about building a digital infrastructure for the future. With the deep integration of technologies such as 5G and edge computing, this system will continue to unlock its potential, driving the evolution of industrial material handling from ‘automation’ to ‘autonomous operation.’
As a company specialising in intelligent logistics solutions, AiTEN Robotics has consistently focused on ‘smart factory’ scenarios, deeply integrating technological innovation with industry needs, and has provided comprehensive services to over 200 manufacturing clients worldwide: By leveraging a full range of material handling robot product portfolios to cover diverse material handling scenarios, developing an industry-grade intelligent scheduling system to enable efficient collaboration among multiple devices, and providing a comprehensive lifecycle service system spanning pre-sales planning, deployment implementation, and operational optimisation, we help enterprises achieve logistics intelligence transformation and continuously empower the digital upgrading and high-quality development of the manufacturing industry.