AiTEN Robot's Best Autonomous Forklift for Material Handling

As the demand for automation continues to reshape warehouses and factories, autonomous forklifts have become a game-changer in material handling. These smart machines improve safety, reduce labor costs, and increase operational efficiency. Whether you're managing a logistics hub or a manufacturing plant, choosing the right autonomous forklift can significantly impact your bottom line.
In this article, we’ll explore the top autonomous forklifts for material handling in 2025, compare their key features, and help you choose the best solution for your needs.
What Is an Autonomous Forklift?
What is an autonomous forklift? Revolutionizing warehouse operations
An autonomous forklift, also known as an AGV (Automated Guided Vehicle) or AMR forklift (Autonomous Mobile Robot), is a self-driving material handling machine. Equipped with sensors, LiDAR, SLAM navigation, and AI algorithms, these forklifts can:
- Transport pallets or goods without human intervention
- Navigate dynamic environments safely
- Avoid obstacles in real-time
- Integrate with WMS/ERP systems
What Can Forklift Robots be Used for?
Forklift robots are versatile and extremely valuable in a variety of material handling scenarios.
In warehouses, they excel at pallet transport, efficiently moving goods between storage locations and loading/unloading areas.
In manufacturing environments, these robots perform well in raw material handling, ensuring a stable supply for production lines.
In finished product management, they transport finished products to storage or shipping areas.
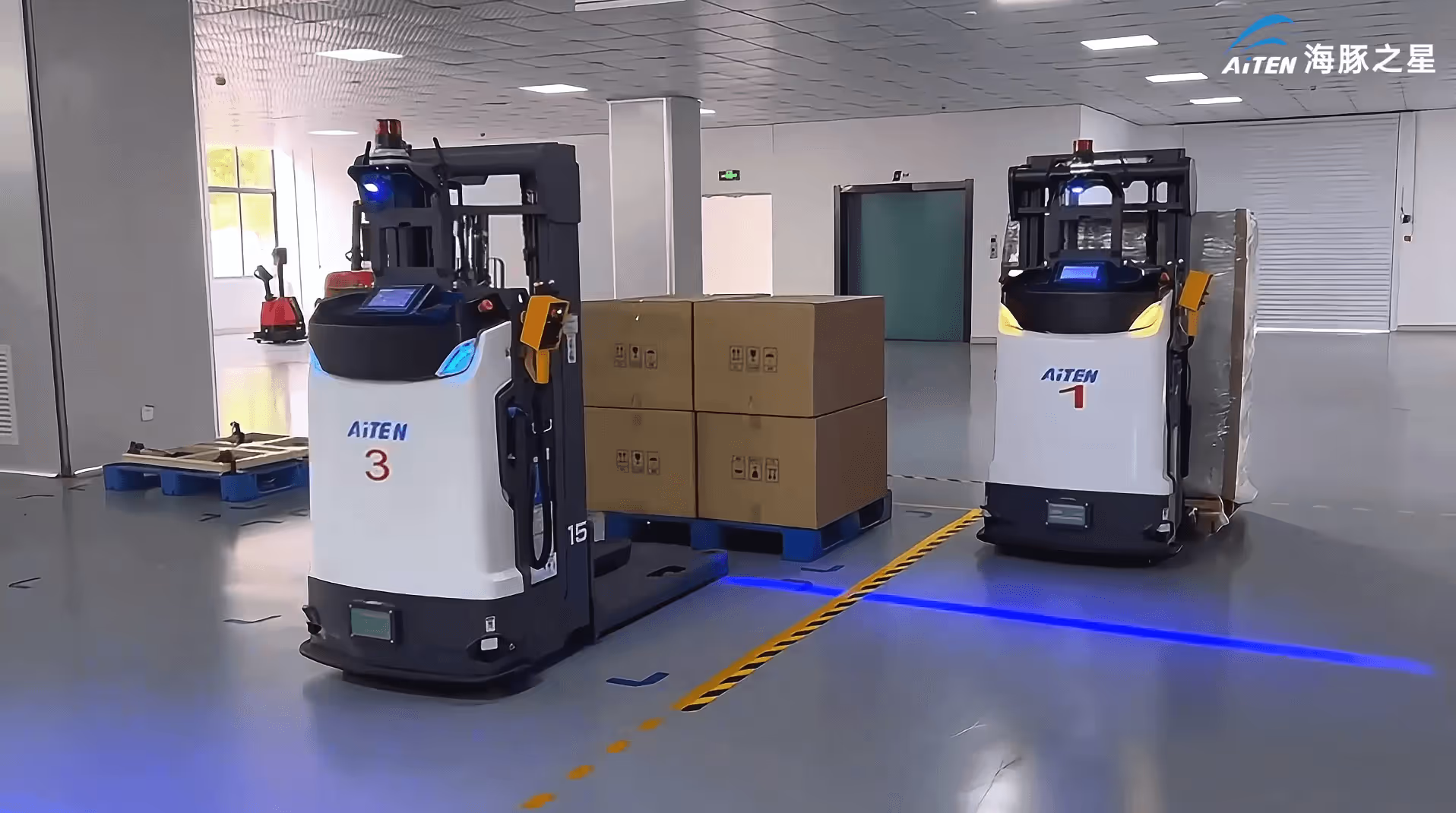
Inventory management is another area where automated forklifts demonstrate their value. They can automatically perform inventory checks and handle replenishment tasks, thereby reducing errors and improving overall inventory accuracy.
In logistics operations, they play an important role in cross-docking (i.e., the rapid transfer of goods between incoming and outgoing shipments), helping to streamline the distribution process.
AiTEN Robot Autonomous Forklift Recommendation
1. AiTEN APx Automated Guided Vehicle
The AiTEN APX Automated Guided Vehicle provides an autonomous solution for long-term repetitive tasks, with a rated load capacity of up to 3000kg. These tasks often result in high operator turnover rates. Now, you can retain talent by automating these monotonous, repetitive tasks and promote skilled operators to more attractive, higher-value tasks. If immediate task execution is required, the APX Automated Guided Vehicle can also switch to manual mode, further enhancing the flexibility of the solution.
- Narrow aisle handling
- Material distribution in production workshops
- Inventory replenishment and transportation
AiTEN APx series material handling robot product specifications
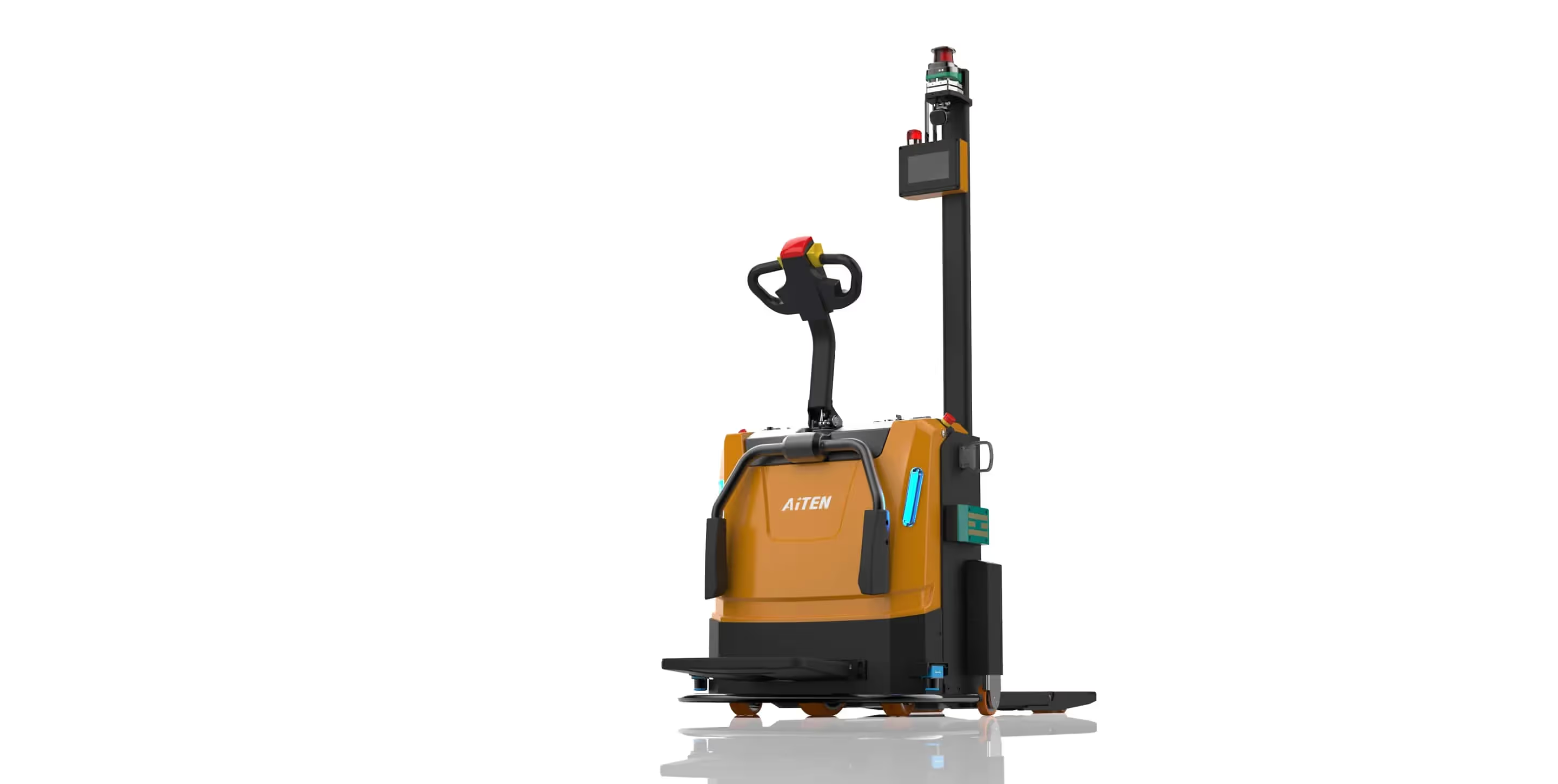
2. AiTEN AR Forward-Moving Automatic Forklift
AiTEN Robotics' automatic reach truck has a rated load capacity of 1000kg-2000kg and can automatically store and retrieve goods at a height of 3 metres, maximising vertical storage space and addressing labour shortages. It is ideal for distribution centres and warehouses facing inventory growth challenges.
- Autonomous charging
- Operates in various temperatures and warehouse management systems
- Ideal for distribution centres and warehouses
AiTEN AR series automatic forklift product specifications
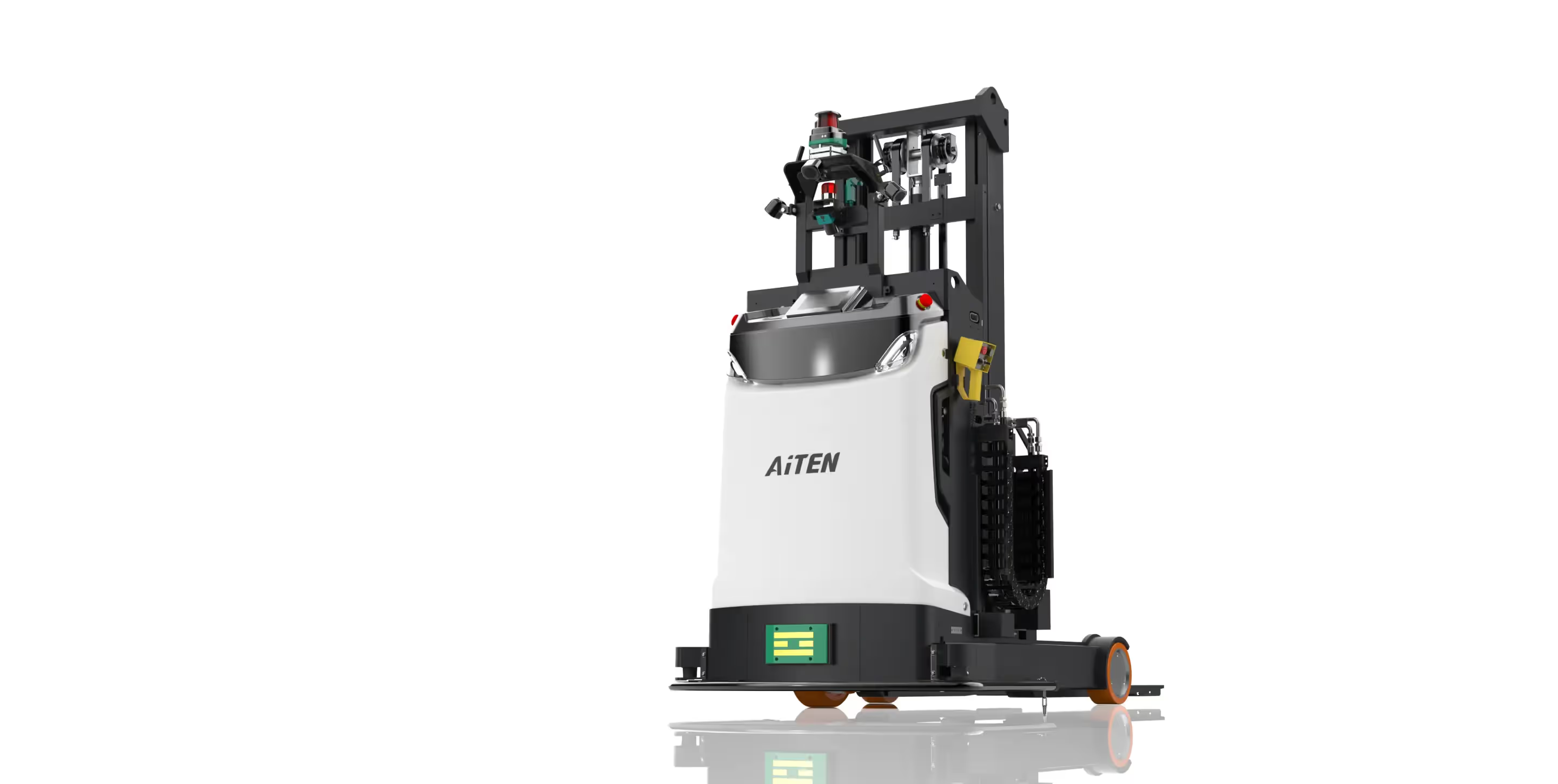
3. AiTEN AE Automatic Counterbalanced Stacker
The automatic counterbalanced stacker provides an autonomous solution for your horizontal and vertical transport needs, with a rated load capacity ranging from 1,000 to 3,000 kg. By automating these needs, you can reduce ongoing labour challenges and avoid damage to products, facilities, and forklifts.
- The height for storing or removing pallets can reach up to 3 metres
- Handles pallets of smaller widths
- Autonomous charging
AiTEN AE automatic counterbalanced stacker product specifications
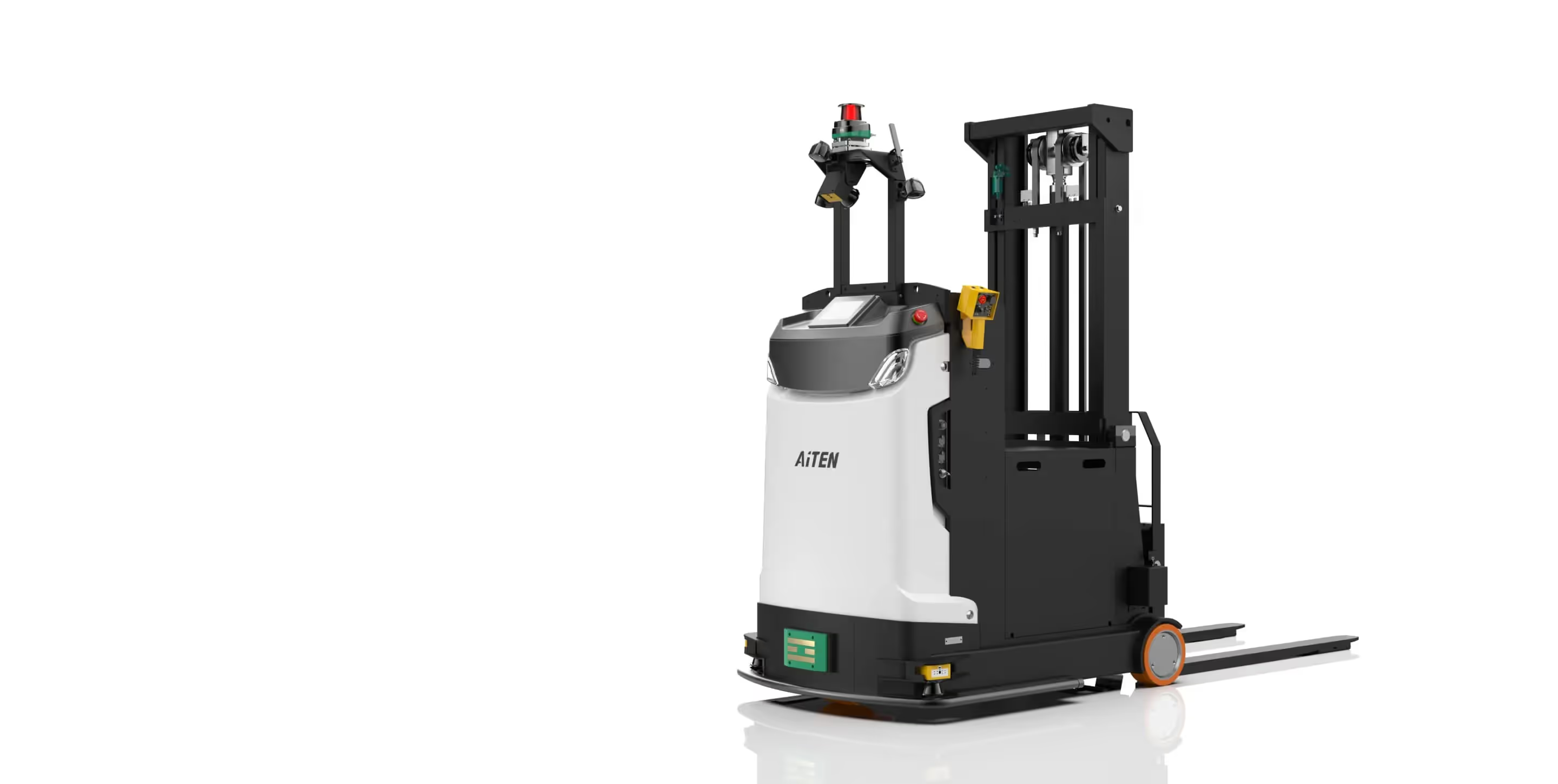
How to Choose the Right Autonomous Forklift
Before integrating forklift robots into your operations, it is crucial to carefully evaluate several key factors.
First, assess whether forklift automation is technically and economically feasible. This requires analysing your current operations, such as aisle widths and material handling processes, to determine whether forklift robots are suitable for your specific environment. A detailed return on investment analysis is essential, taking into account not only initial costs but also long-term cost savings from increased efficiency and reduced errors.
Consider the scalability and flexibility of potential solutions to ensure your investment can grow with your business and adapt to changing market demands. The choice of navigation technology is also critical, as different methods have their own advantages and disadvantages. Ensure that the selected solution can be seamlessly integrated with your existing warehouse management and ERP/MES systems.
Safety should be a top priority, so be sure to look for reliable safety features and certifications. Consider how the forklift robot will interact with people and other equipment in the facility.
By carefully considering these factors, you can make an informed decision about whether forklift robots are suitable for your business and which solution best meets your operational needs and business objectives.
Benefits of Using Forklift Robots
Automatic forklift robots, commonly known as AGVs (automated guided vehicles), are equipped with cutting-edge technology that enables them to navigate their surroundings autonomously. This means that they can transport materials from one location to another without human intervention. This innovative method of material handling offers the following advantages:
1. Using forklift robots can bring many significant advantages to businesses. Perhaps most importantly, these machines can operate around the clock without needing breaks or shift changes, thereby significantly improving productivity.
2. This continuous operation can significantly increase throughput and efficiency, enabling businesses to handle more goods at a faster pace and with greater consistency.
3. By eliminating human error and fatigue-related accidents, forklift robots significantly reduce workplace injuries. Their advanced sensor systems enable them to detect and avoid obstacles, creating a safer working environment for employees.
4. While the initial investment in a forklift robot system may be substantial, the long-term cost savings are typically significant as well. These savings stem from reduced labour costs, minimised damage to goods and infrastructure, and optimised space utilisation.
5. The precision of autonomous systems can improve inventory accuracy and reduce losses caused by misplacement or damage.
6. Forklift robots offer valuable flexibility and scalability. They can adapt to changing warehouse layouts and fluctuating demand, helping businesses quickly adjust their operations. This adaptability is particularly useful for companies affected by seasonal fluctuations or planning future expansion.
7. The data generated by the system provides valuable insights into material flow, equipment utilisation, and operational bottlenecks, enabling data-driven decision-making and continuous process improvement.
결론
Autonomous forklifts are accelerating the transformation of material handling processes in logistics and manufacturing, spanning a wide range of applications from light-duty warehousing to heavy-duty manufacturing.
The adoption of autonomous forklift robots marks a pivotal moment in the material handling and logistics sectors. By embracing this technology, businesses can maintain competitiveness in rapidly changing environments and pave the way for a smarter, more efficient future.
If you are planning to upgrade your factory or warehouse with intelligent solutions, selecting the right autonomous forklift is undoubtedly a crucial step toward enhancing efficiency and achieving cost savings.
About AiTEN Robotics
As a company specialising in intelligent logistics solutions, AiTEN Robotics has consistently focused on the ‘smart factory’ scenario, deeply integrating technological innovation with industry needs. It has provided comprehensive services to over 200 manufacturing clients worldwide: Leveraging a full range of material handling robot product portfolios to cover diverse material handling scenarios, we have developed an industry-grade intelligent scheduling system to enable efficient collaboration among multiple devices. Through a comprehensive lifecycle service system spanning pre-sales planning, deployment and implementation to operations optimisation, we empower enterprises to achieve logistics intelligence transformation, continuously driving the digital upgrading and high-quality development of the manufacturing industry.
Contact us to explore automation solutions for your factory.