Common Issues with AGV Forklifts: Precise Positioning, Safe Obstacle Avoidance, and System Integration Solutions
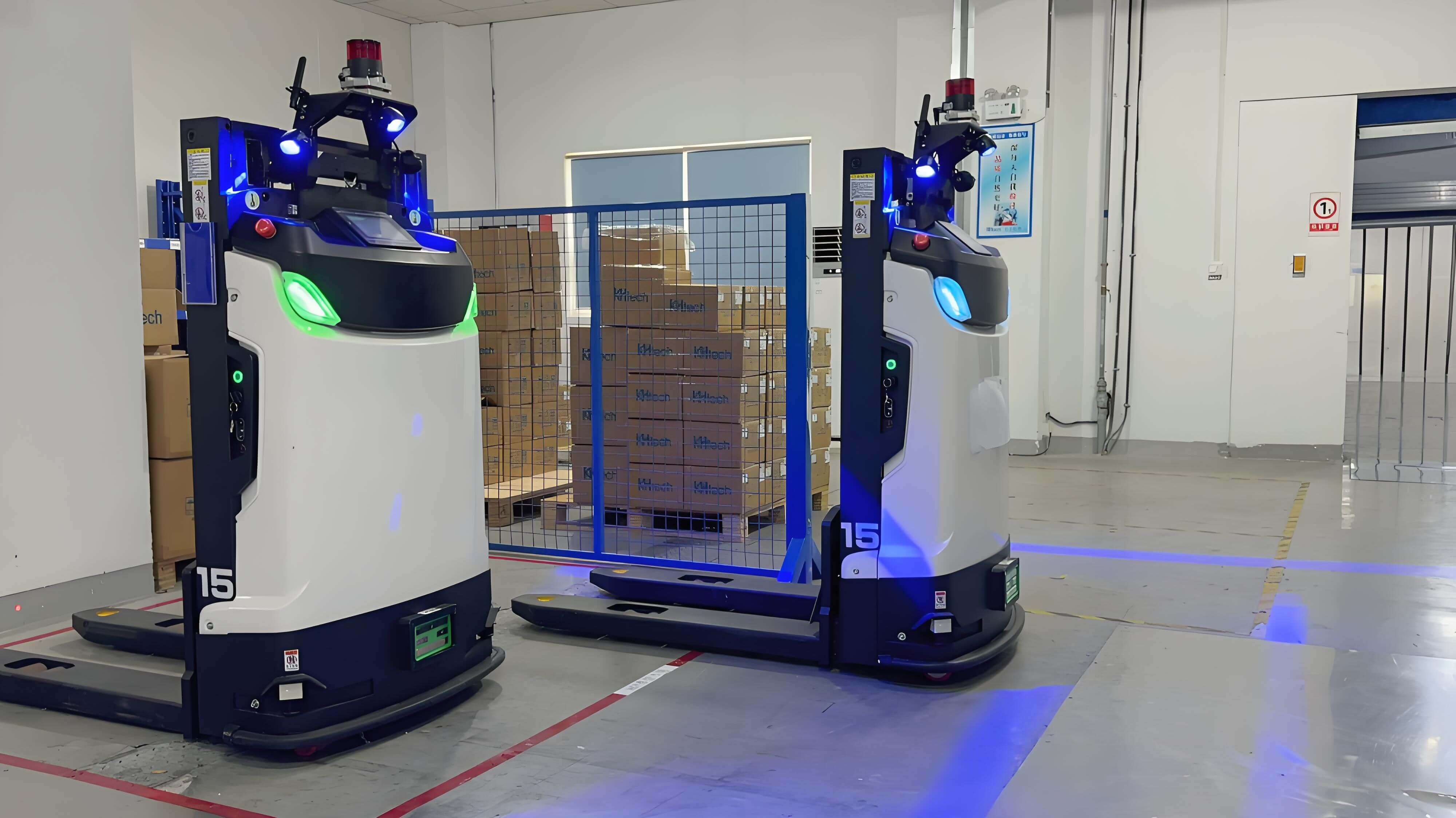
As a core piece of equipment in intelligent logistics, AGV forklifts often face issues such as positioning drift, poor system compatibility, and obstacle avoidance failure during implementation. This article offers an in-depth examination of the causes and solutions to five common issues, enabling companies to mitigate operational risks and enhance efficiency.
1. Positioning and Navigation Issues: What to Do When the Driving Path Deviates?
Typical manifestations:
- Laser SLAM forklifts lose their position in dynamic environments.
- QR code navigation AGVs frequently derail due to ground contamination.
AITEN Solutions:
- Multi-sensor fusion positioning technology
AiTEN's flagship product, the MP10s, supports a variety of advanced technologies such as 2D and 3D laser SLAM navigation, enabling precise navigation even in dynamic environments.
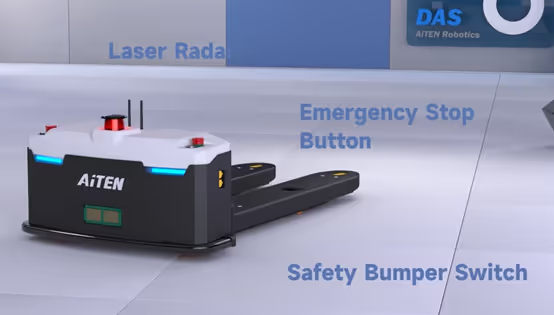
Goods arrival sensors, fork tip sensors, and pallet recognition technology further enable high-precision positioning, achieving efficient and accurate material handling.
- Adaptive Map Update System
The RCS (Robot Control System) used to manage AiTEN robots is an intuitive tool featuring high-precision sensor-based positioning and real-time response capabilities to handle shelf displacement or temporary obstacle interference.
2. Safety Obstacle Avoidance Issues: How to Deal with Sudden Obstacles?
Industry pain points: Traditional infrared sensors have large blind spots, leading to collisions.
AITEN solution:
AGV (Automated Guided Vehicle) Multi-Sensor-Fusion für Echtzeit-Hindernisvermeidungstechnologie
AiTEN robots are equipped with multiple sensors that can monitor the surrounding environment in real time and automatically avoid obstacles. They also have a collision prevention system to ensure operational safety.
3. System Integration Issues: How to Connect WMS/ERP Data Flows?
Common issues:
- Interface protocol incompatibility (Modbus/TCP vs OPC UA)
- Scheduling system and warehouse management software data are not synchronised
AITEN Solutions:
Integrated with enterprise WMS and MES systems, enabling automatic task allocation and scheduling, while supporting real-time path planning and collaborative operations among multiple robots to avoid congestion and conflicts, thereby enhancing overall operational efficiency.
Introduction to AGV Unmanned Forklift Docking Methods: The Core Hub of Intelligent Logistics
AiTEN's WCS device control system offers strong compatibility, capable of connecting with button boxes, barcode readers, RFID devices, and managing Modbus/TCP IO devices. It can also seamlessly integrate with peripheral equipment such as automatic doors, elevators, and conveyor lines, deeply integrating with the scheduling system to precisely transmit control commands to the core control system. This promotes the automation of integration processes, achieving higher-level intelligent collaboration and efficient operations between devices, laying a solid foundation for the construction of smart factories.
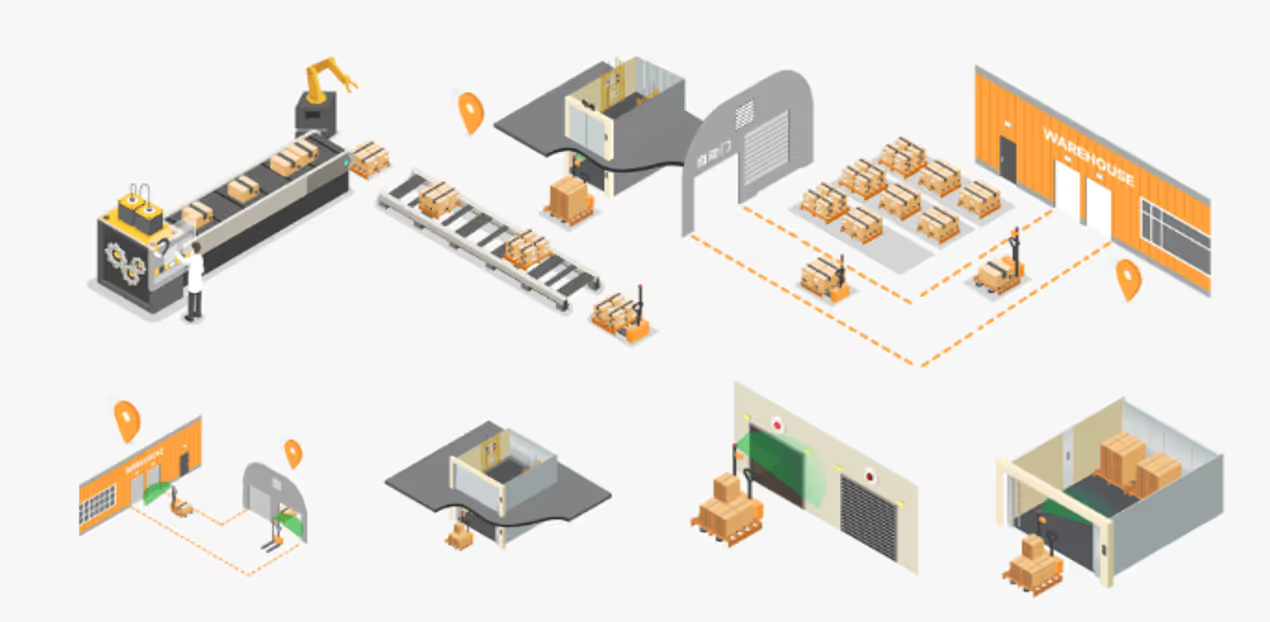
4. Battery Life and Maintenance Issues: How to Reduce Downtime?
Technical issues: Traditional lead-acid battery AGVs have a battery life of only 4-5 hours and require 8 hours to charge, which cannot meet the requirements of 24-hour continuous operation.
AiTEN Solution:
Utilising lithium iron phosphate batteries, which offer high safety standards, with up to 2,000 charge/discharge cycles. The batteries support fast charging, achieving a rated operating range of 6–8 hours, with charging time under 2 hours. They automatically charge when idle, meeting the demands of round-the-clock operations.
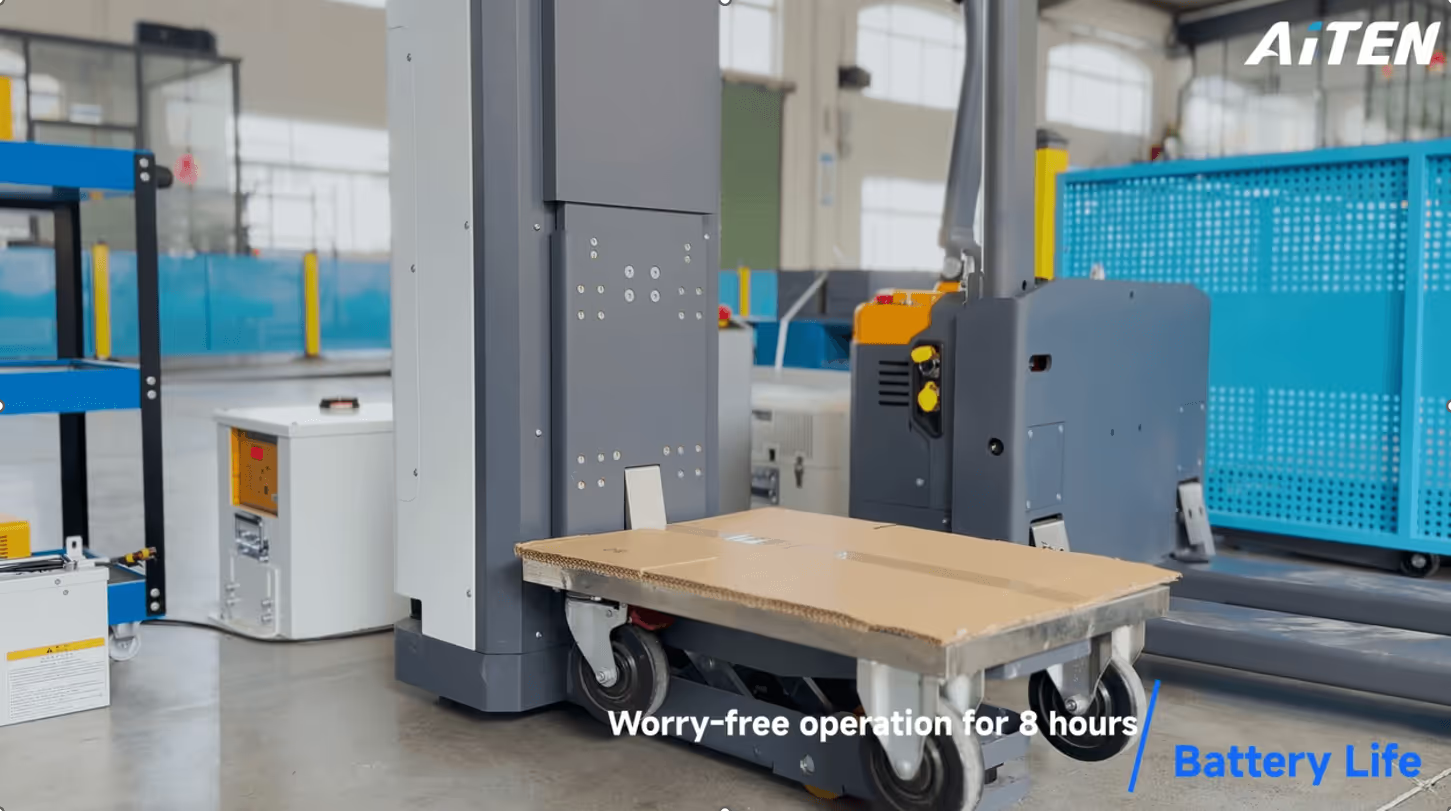
5. Multi-machine Scheduling Issues: How to Optimise Cluster Operations?
Typical manifestations: In cluster operations involving more than 50 AGVs, traditional rule-based scheduling (such as first-come, first-served) can easily lead to path conflicts, uneven task distribution, and increased empty load rates.
AiTEN Solution: The RDS Intelligent Scheduling System leverages efficient intelligent algorithms and intelligent management functions to precisely allocate logistics resources and efficiently schedule tasks. Whether it's internal warehouse goods handling or cross-regional logistics distribution, it ensures accuracy and significantly improves overall operational efficiency.
Schlussfolgerung
The bottleneck in the application of AGV unmanned forklifts is essentially a process of technical iteration and scenario adaptation. From hardware redundancy design to software intelligent upgrades, from single point failure resolution to full chain process optimisation, enterprises need to build solutions with a ‘systematic thinking’ approach. Choose AITEN to achieve full process and comprehensive protection during the use of AGV unmanned forklifts.
About AITEN Robotics
AiTEN Robotics is a global leader in autonomous industrial vehicles (AMR/AGV) and logistics automation solutions. AiTEN Robotics has developed ten product series to meet the needs of full-stack material handling scenarios. AiTEN Robotics has deployed more than 200 projects in over 30 countries and regions, and is trusted by numerous Fortune 500 companies across industries such as automotive, food and beverage, chemicals, pharmaceuticals, manufacturing, and third-party logistics, enhancing operational safety, efficiency, and future readiness.
Contact AiTEN to learn how our innovative autonomous forklifts and intelligent systems can transform your material handling processes.