Analysis of AGV Pallet Handling Pick-and-Place Path Planning Technology
.avif)
AGV precise pallet picking and placing rely on advanced path planning technology. The task not only requires collision-free paths, but also high-precision posture and smooth trajectories when approaching pallets. This article analyses the core technologies for achieving this goal, such as the coordinated application of Hybrid A and Bézier curves.
Why Does Pallet Handling Require Special Path Planning?
Challenges:
- High precision at the end: The forks must be aligned with the pallet fork holes with centimetre/millimetre precision and meet strict parking orientation requirements.
- Strong movement constraints: Strict adherence to AGV dimensions, minimum turning radius and non-complete constraints (no lateral movement) is required, especially in narrow spaces.
- Path smoothness: Avoid sudden acceleration, deceleration or turning to ensure cargo stability and operational safety.
- Near-End Precision Obstacle Avoidance: High-precision sensing is required when approaching pallets to address unknown obstacles or positioning errors.
Technical Analysis
1. Global path planning
Technology: Dijkstra, standard A*
Function: Quickly generate a general path (connected, low cost) from the starting point to the tray area on the global grid map.
Features: Fast speed, ignores kinematic details.
2. Endpoint Fine Path Planning
Core Technology: Hybrid A**
Advantages: Searches in a continuous state space (x, y, θ) and directly embeds vehicle kinematic models (such as bicycle models).
Effects: Generates feasible paths that reach the exact target posture (x, y, θ) and comply with constraints such as turning radius, solving complex turning issues in the ‘last metre’.
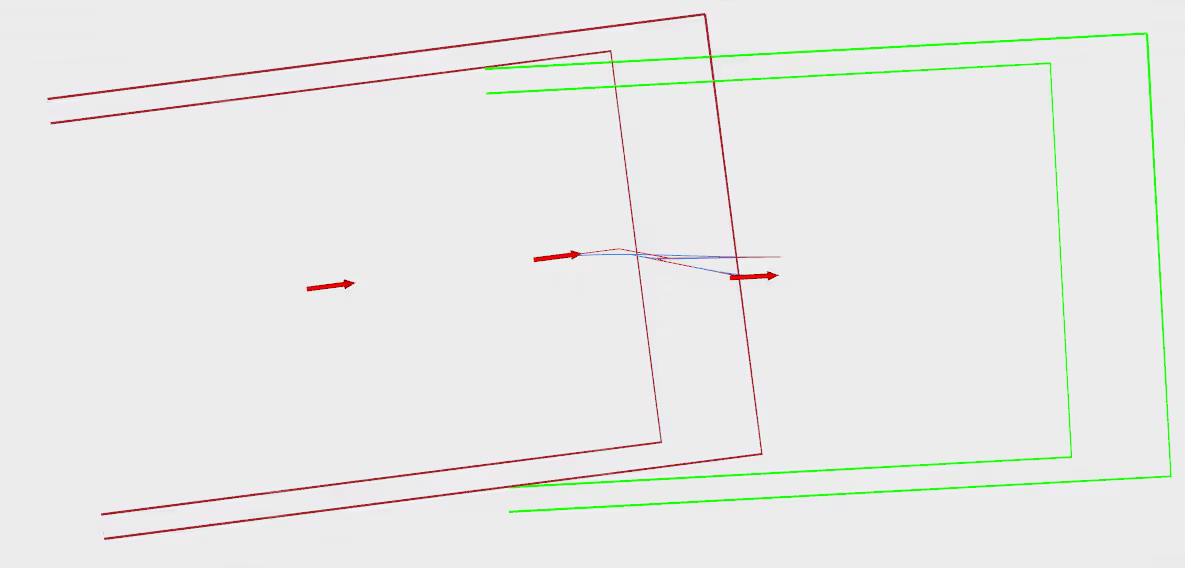
3. Path smoothing and optimisation
Core technology: Bézier curves
Advantages: Generates smooth, continuous curves through control points, ensuring that the start/end positions and directions (tangents) are controllable.
Applications: Smoothes paths generated by search (often containing angles), ensuring continuous curvature; connects path segments; generates continuous speed trajectories.
Alternative technologies: B-splines, NURBS.
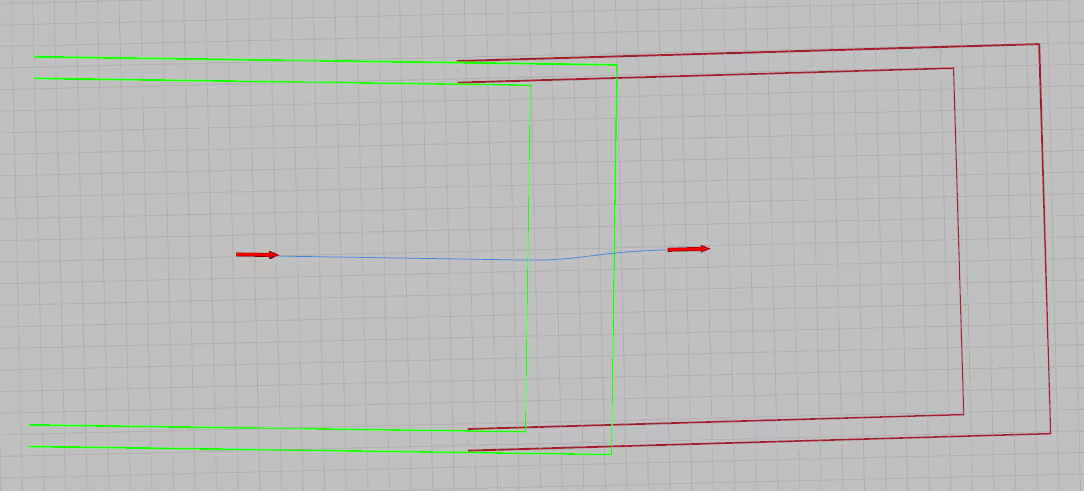
4. Real-time obstacle avoidance and path adjustment
Technology: Dynamic Window Algorithm (DWA), Time Elastic Band (TEB), Rapid Replanning.
Function: Based on sensor data, locally adjust the path/speed to avoid dynamic obstacles while staying as close as possible to the original optimised path.
Technology Convergence
The AGV pallet picking and placing path planning process may be as follows.
1. Global planning (A*): Plan a rough path from the starting point to the vicinity of the pallet area on the grid map.
2. Terminal Planning Switch: Trigger detailed planning when the AGV approaches the pallet area.
3. Precise Docking (Hybrid A*): Plan a path that complies with kinematics to the target pose (x, y, θ).
4. Path Smoothing (Bezier/Spline): Smooth the stitched path to generate a geometrically continuous final path.
5. Trajectory generation: Generate a trajectory with velocity/acceleration constraints based on the smoothed path for the controller to execute.
6. Real-time obstacle avoidance: Monitor the entire process and dynamically adjust the path/speed to avoid obstacles.
Challenges
Although existing technologies can already solve AGV pallet picking and placing problems to a certain extent, there are still ongoing challenges and opportunities for development:
- Balancing efficiency and accuracy: More detailed planning often means higher computing costs. How to improve planning speed while ensuring accuracy is an area for continuous optimisation.
- Adaptability to dynamic environments: How to handle moving obstacles, changing pallet positions or postures more robustly.
- Sensor fusion and positioning accuracy: High-precision path execution relies on high-precision real-time positioning and environmental perception.
- Multi-AGV collaborative operations: In densely populated picking and placing areas, how to efficiently and safely coordinate multiple AGVs for operations.
- Learning-based methods: Exploring the use of reinforcement learning and other methods to enable AGVs to autonomously learn optimal picking and placing strategies and paths.
Conclusión
Precise pallet picking and placing by AGVs is a complex and precise task in the field of automation. It does not rely on a single ‘silver bullet’ technology, but rather on the clever combination and coordination of multiple path planning and optimisation technologies.
From global route guidance to kinematic perception-based end-point planning enabled by Hybrid A*, and smooth trajectories achieved through techniques like Bézier curves, these technologies collectively chart a ‘smart path’ for AGVs to operate safely, precisely, and efficiently, injecting powerful momentum into modern automated logistics and production. As technology continues to advance, we have every reason to believe that future AGVs will demonstrate even greater intelligence and flexibility in pallet handling operations.
AiTEN Robotics, headquartered in Suzhou, China, is a global leader in autonomous industrial vehicles (AMR/AGV) and logistics automation solutions. AiTEN Robotics has developed ten product series to meet the needs of full-stack material handling scenarios. AiTEN Robotics has deployed more than 200 projects in over 30 countries and regions, and is trusted by numerous Fortune 500 companies across industries such as automotive, food and beverage, chemicals, pharmaceuticals, manufacturing, and third-party logistics, enhancing operational safety, efficiency, and future readiness.