What Are Under-Pallet AGVs? Compact Robots for Smart Warehousing
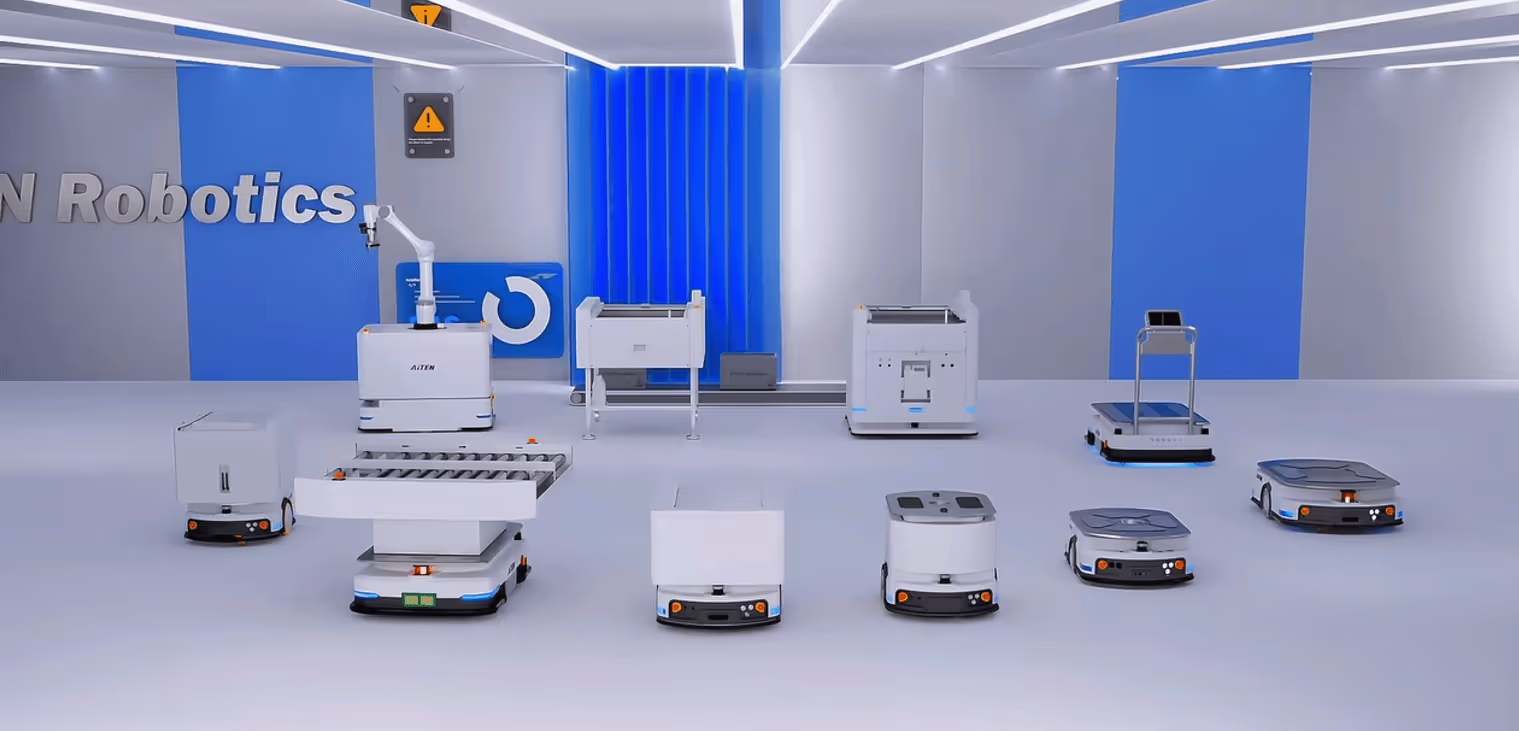
In the wave of smart manufacturing and smart warehousing, under-pallet AGVs (Automated Guided Vehicles) have become the core equipment for logistics automation with their ‘low-key and efficient’ characteristics. These automated transport robots, which can be concealed under shelves or materials, are reshaping the material flow model in factories and warehouses with their advantages of flexible deployment, space optimisation, and low-cost integration.
1. What is an Under-pallet AGV?
An under-pallet AGV is a type of automated equipment that operates by being concealed beneath material units (such as pallets, racks, or containers), enabling automatic lifting, transportation, and docking. Compared to traditional forklift-style AGVs, it does not require manual operation and can complete material transportation via pre-set paths or autonomous navigation, particularly excelling in narrow spaces and high-density storage environments.
Structurally, an under-pallet AGV typically consists of a drive unit, a lifting mechanism, a navigation system, a control system, and safety sensors. Taking the AiTEN TP Lifting Series as an example, its chassis height can be as low as 300mm, with a load capacity range of 300-1500kg, enabling it to easily access the underside of various material carriers. By lifting, it completes the entire ‘pick-transport-place’ process, optimising space utilisation.
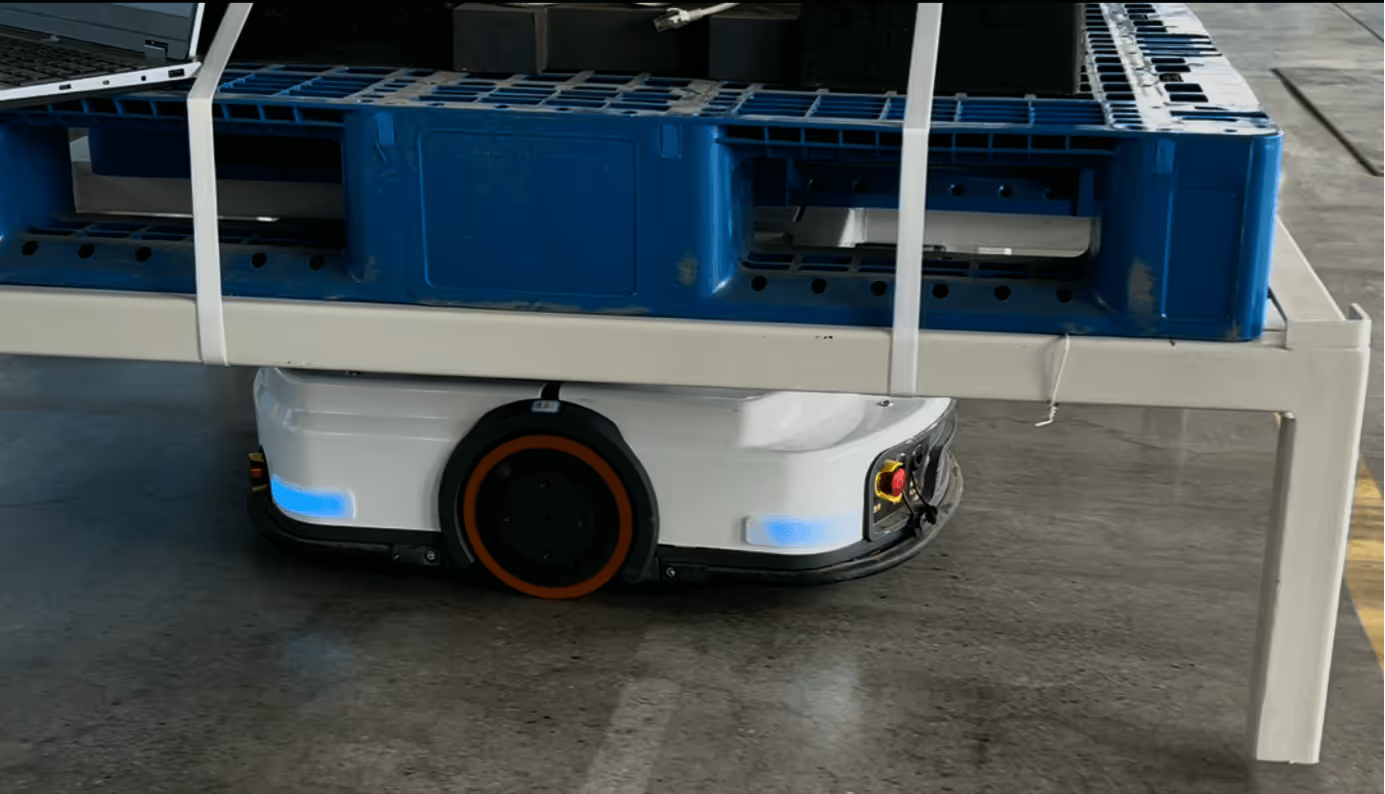
2. Core Advantages of Under-pallet AGVs
(1) Improved space utilisation
The under-pallet AGV has a low body height (generally below 30 cm) and a small turning radius, enabling it to navigate flexibly in channels as narrow as 1.5 metres. It is well-suited for dense warehouse layouts featuring narrow aisles and high shelves. The flat warehouse area of China Telecom Suzhou Branch covers a large area and primarily handles lightweight and small-sized materials. The delivery robot TP30 has a rated load capacity of 300 kg, fully meeting the requirements for material handling. The TP30 delivery robot is compact and elegant, with a body length of only 750 mm, a width of 540 mm, and a height of 250 mm, enabling it to freely navigate narrow aisles and low shelves. The TP30 delivery robot's body can be fitted with different modules to customise submerged lifting-specific racks, tailored to the actual dimensions of the materials to meet customers' personalised needs.
AiTEN enhances warehouse efficiency for china telecom with advanced AGV management system
(2) Flexible deployment with zero modification requirements
No need to lay magnetic navigation tracks or modify the ground. Modern under-pallet AGVs mostly use laser SLAM navigation technology and are also compatible with QR code navigation. They can quickly plan paths through software, easily handle the most dense and complex environments, and provide accurate positioning and efficient navigation. For older warehouses, they can save time on equipment debugging and path deployment compared to traditional automation solutions.
(3) Safer human-machine collaboration
Equipped with a 360° omnidirectional radar obstacle avoidance system, AGVs can real-time identify pedestrians and obstacles, ensuring precise operation in complex and diverse work environments. In workshop scenarios where people and vehicles coexist, their ‘stealth operation + high-speed stability’ characteristics can reduce collision risks by over 90%, fully meeting the CE certification requirements for industrial robots.
3. Technical Highlights
- High-precision positioning: Utilising our proprietary SLAM technology, positioning accuracy can reach ±10 mm, ensuring stability and safety.
- Cluster scheduling algorithm: Through our proprietary software platform, multi-machine collaboration and dynamic path optimisation can be easily achieved.
- Modular Design: Featuring a reinforced chassis design, it supports prolonged operation and high-frequency tasks. The modular design facilitates maintenance and upgrades, allowing flexible adjustment of functional modules to accommodate various material forms such as pallets, bins, and racks.
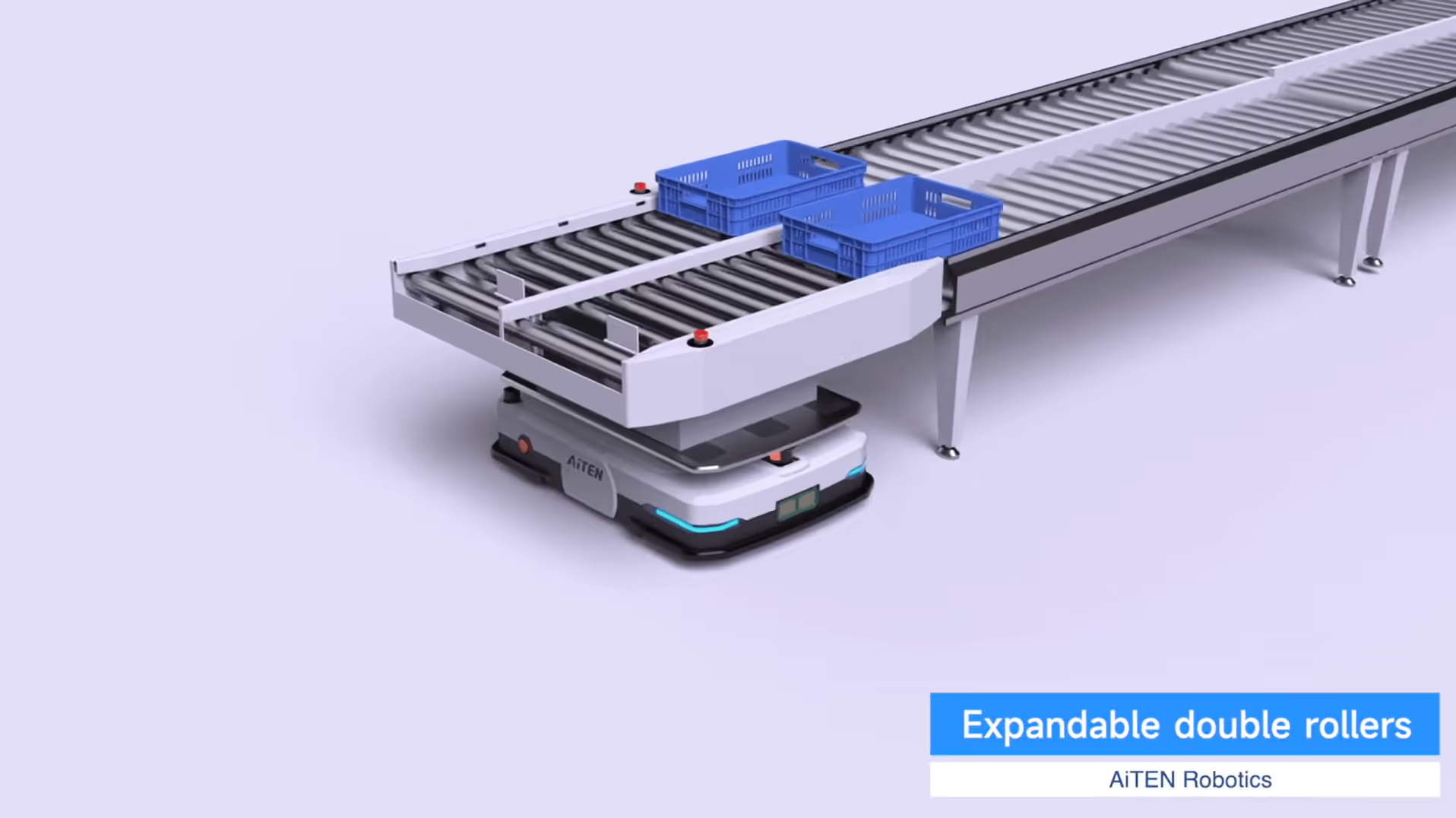
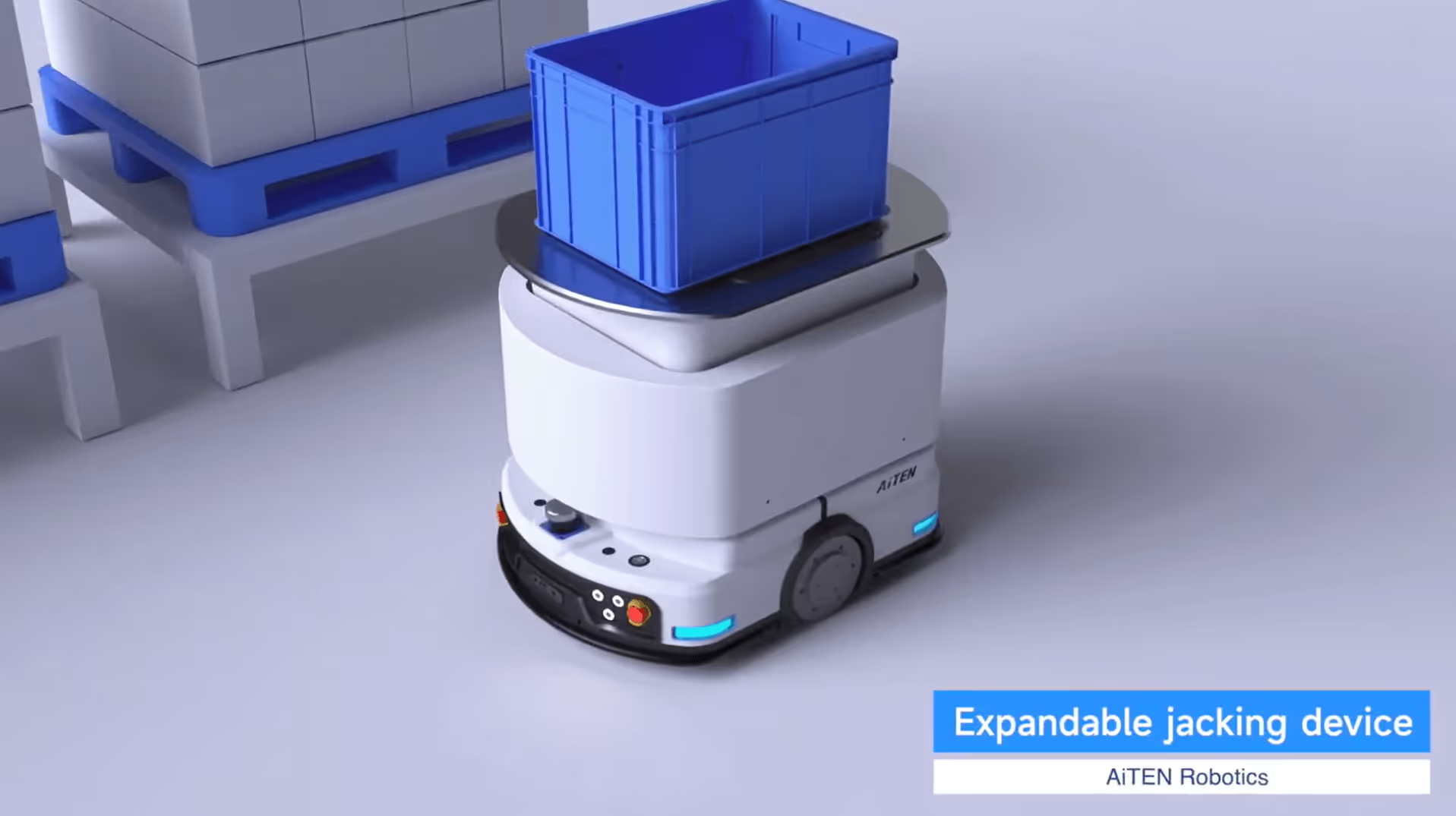
- Rapid integration capabilities: Supports seamless integration with WMS and MES systems, enabling automatic task distribution through API interfaces and reducing manual intervention.
4. Typical Application Scenarios
Flat handling: Material box/material trolley production line distribution, automated handling, optimised space utilisation

Production line connection, production line distribution: Connect different workstations to achieve flexible production and material transport

5. Selection Recommendations
- Based on load requirements, AGVs with different load capacities are suitable for different scenarios.
AMR load capacity analysis: how to choose the right transport robot?
- Pay attention to channel width: For narrow channels, choose omnidirectional wheel drive models to improve turning flexibility.
- Consider future expansion: Choose an open system that supports secondary development to facilitate the addition of AGVs or new functions in the future.
Schlussfolgerung
As the ‘invisible driving force’ behind flexible automation, under-pallet AGVs are becoming the preferred solution for automation upgrades in small and medium-sized warehouses and production lines, thanks to their ‘small size, big power’ advantage. Whether it is the basic need to replace manual handling or the advanced goal of building an intelligent logistics network, they can provide efficient, safe, and low-cost automation solutions.
Choosing the right type of AGV will lay a solid foundation for your smart logistics system.
About AiTEN Robotics
As a company specialising in intelligent logistics solutions, AiTEN Robotics has consistently focused on the ‘smart factory’ scenario, deeply integrating technological innovation with industry needs. It has provided comprehensive services to over 200 manufacturing clients worldwide: Leveraging a full range of material handling robot product portfolios to cover diverse material handling scenarios, we have developed an industry-grade intelligent scheduling system to enable efficient collaboration among multiple devices. Through a comprehensive lifecycle service system spanning pre-sales planning, deployment and implementation to operations optimisation, we empower enterprises to achieve logistics intelligence transformation, continuously driving the digital upgrading and high-quality development of the manufacturing industry.
Contact us to explore automation solutions for your factory.