What Robots are Used in Warehouses? Let’s Learn About Types of Automated Warehouse Robots
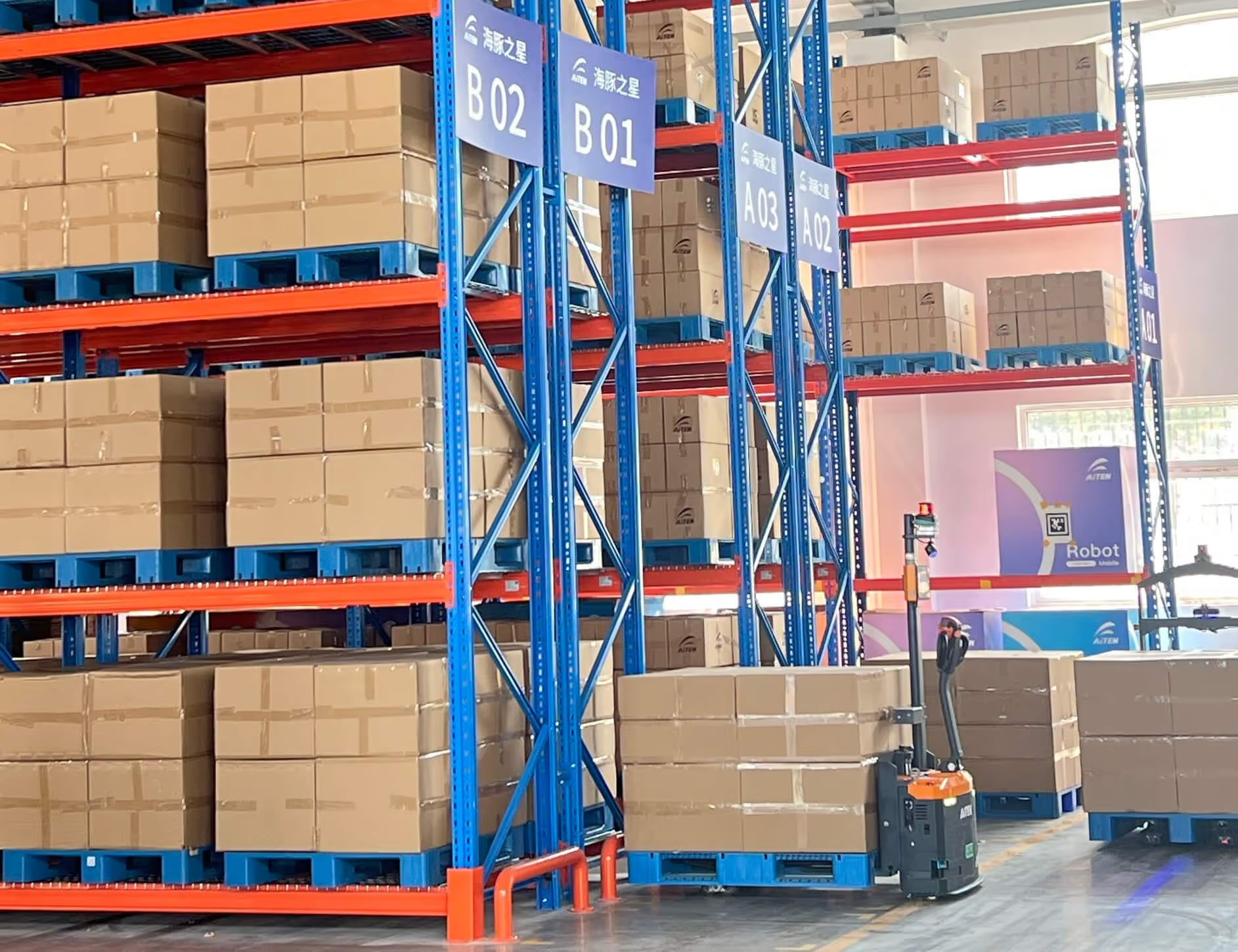
In an era of relentless technological advancement, the role of robots in reshaping industries cannot be overstated. In the realm of logistics and warehousing, different types of robots have emerged as indispensable allies, revolutionizing the way goods are stored, moved, and managed.
1. What are Automated Warehouse Robots?
Automated warehouse robotics refers to the use of robotic technology and automation systems in a warehouse or distribution center to perform various tasks related to the movement, organization, and management of goods and materials. Broadly speaking, these robots and automation systems are designed to streamline and optimize warehouse operations, improving efficiency, accuracy, and productivity.
2. Different Types of Automated Warehouse Robots
The logistics industry has witnessed a transformation in recent years, with various types of robots playing pivotal roles in streamlining operations and optimizing efficiency. Here, we explore the diverse array of logistics robots usually in use today:
(1)Autonomous Mobile Robots (AMRs)
Autonomous mobile robots (AMRs) are sophisticated robots that can independently navigate your warehouse, eliminating the need for human intervention. AMRs utilize advanced technologies, such as machine learning, artificial intelligence and sensors to plan and adjust their routes in real-time.
They can also manage unforeseen challenges, whether it’s avoiding unanticipated crowds or evading falling objects.
(2)Automated Guided Vehicles (AGVs)
Automated guided vehicles (AGVs) are warehouse robots that follow predetermined paths using a combination of sensors, markers and lasers for accurate navigation and movement.
Unlike AMRs, AGVs rely on fixed routes and guidance from warehouse operators to function. They also have less adaptability to unexpected changes in their surroundings.
AiTEN's material box handling robot AL05 adopts SLAM and laser navigation technology, combined with real-time environment scanning, automatically plans the optimal route to ensure efficient handling in complex environments, and is equipped with multiple sensors to monitor the surrounding environment in real time and automatically avoid obstacles. It can achieve all-weather and fully automatic handling operations, reducing manual intervention, especially suitable for high-frequency and highly repetitive handling tasks, ensuring continuous operation of the production line.
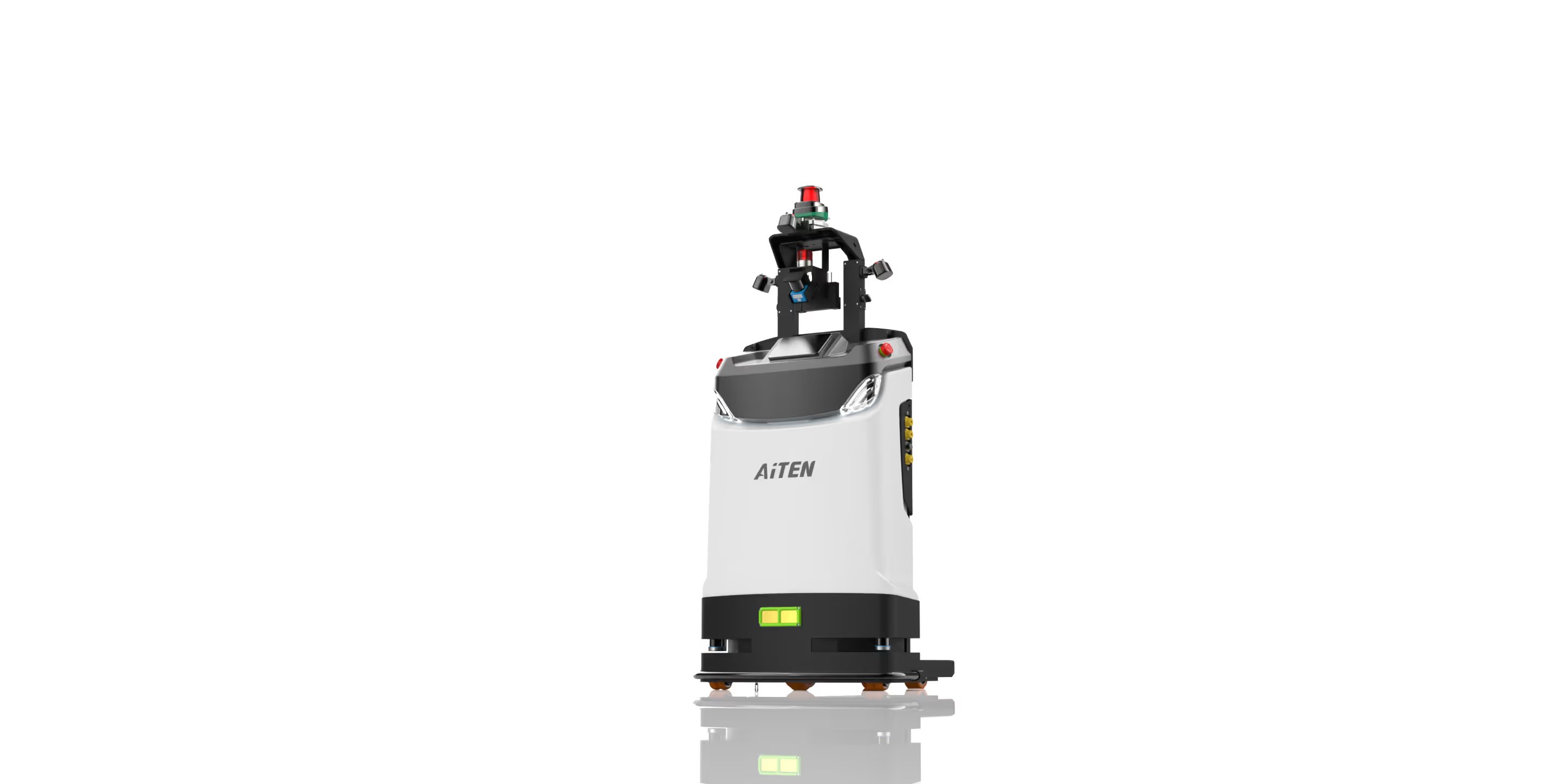
(3)AS/RS (Automated Storage and Retrieval Systems)
AS/RS systems encompass a wide range of technologies, including cube storage robots, shuttles, miniloads, and Vertical Lift Modules (VLMs), each designed to automate different aspects of storage and retrieval. Cube storage robots, for example, can optimize space utilization and operational efficiency by managing densely packed inventory bins with high precision and speed.
The AiTEN AS series consists of cutting-edge automated guided forklifts (AGF) characterized by a compact, modular design. The AS Series adopts a steering wheel chassis mechanism integrated with laser SLAM navigation. This enables autonomous navigation and obstacle avoidance, allowing for flexible and effective operations in complex, industrial environments.
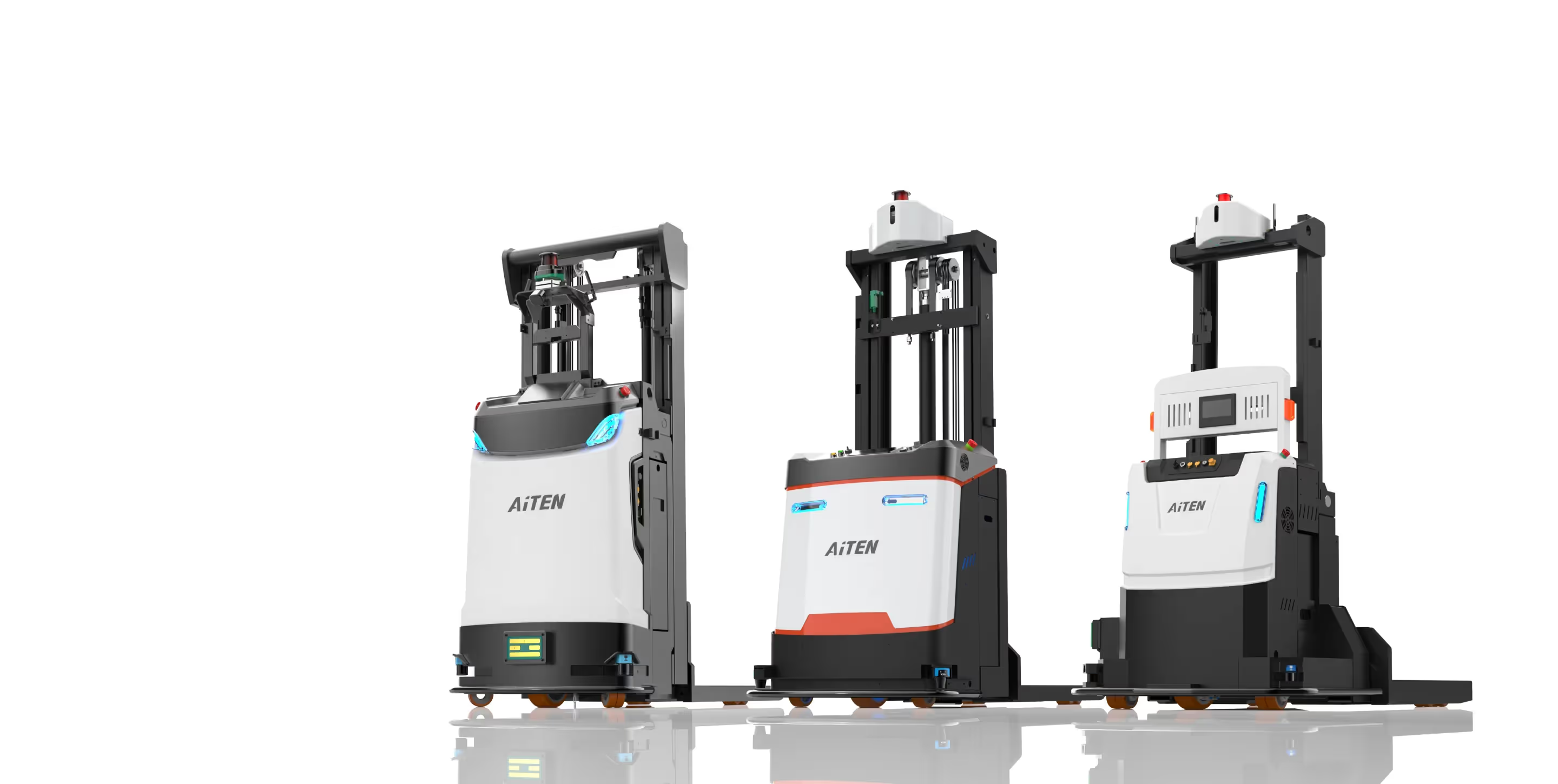
(4)Robotic arms
Robotic arms, also referred to as robotic manipulators, pick and place robots or piece-picking robots, are equipped with multiple joints and end-effectors to handle a wide range of tasks. In logistics, they are used for picking, packing, and palletizing products. These precision instruments improve order fulfillment speed and accuracy. Robotic arms can replace humans at AS/RS workstations for picking, packing, and preparing orders.
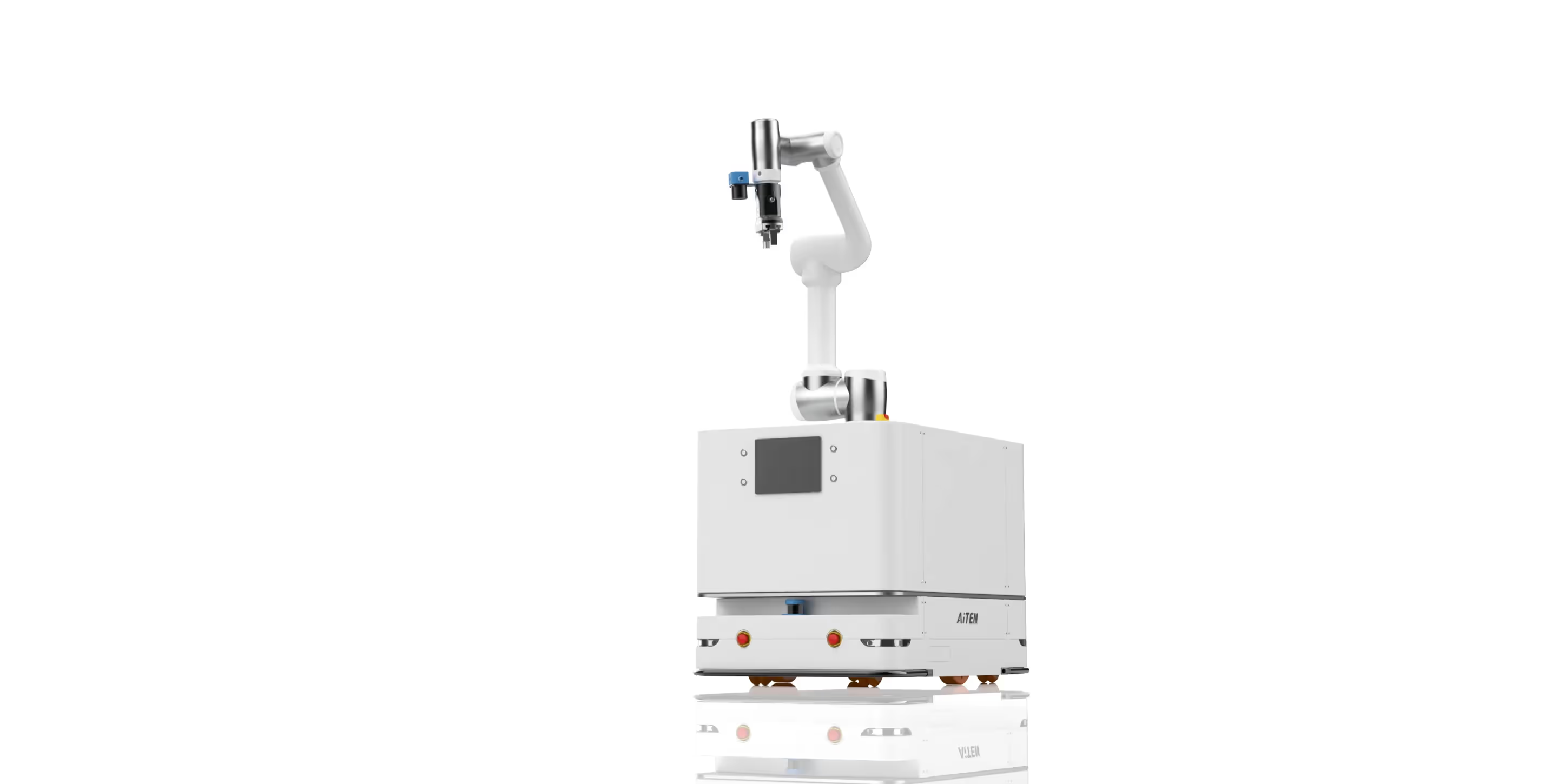
(5)Automated Labeling Robots
Automated labeling robots are warehousing robots that can help warehouse operators automatically place the label in the right spot on the package.
They are equipped with precision applicators to place labels on the desired spot every time. These robots also have sensors and cameras to detect the product’s position and orientation, so they can adjust the label application accordingly.
(6)Packaging Robots
Packaging robots are automated warehouse robots that can help ensure products and pallets are securely wrapped for transport and storage, providing consistent wrapping tension, all while reducing manual labor and material waste.
They are equipped with load sensors to determine the weight and stability of the pallet and turntables to rotate the pallet or product, ensuring even wrapping from all sides.
(7)Cleaning Robots
Cleaning robots are automated warehouse robots that can help maintain cleanliness and hygiene standards in a facility, ensuring a safer and more efficient work environment.
They are equipped with rotating brushes, vacuum systems and sensors to detect dirt and obstacles, and drops.
Cleaning robots include floor scrubbing robots, vacuuming robots and disinfection robots.
(8)Security Robots
Security robots are automated warehouse robots that can help enhance the security of a warehouse by providing continuous surveillance and immediate alerts when unauthorized access, potential breaches, or other unusual activities are detected.
They are equipped with motion and sound sensors and cameras, offering 360-degree views, night vision and even thermal imaging for comprehensive surveillance.
Conclusion
The world of automated warehouse robots is continuously growing, and these different sorts of robots are only the tip of the iceberg. The potential for robots to alter the logistics business is limitless, thanks to recent development in AI, machine learning, and other technologies.
Contact us for advice on the best fit for your warehouse. We’ll perform a warehouse audit to guide you to the right choice.