Upgrading the ‘Brain’ of Handling Robots: Four Core Technologies of Body Intelligence
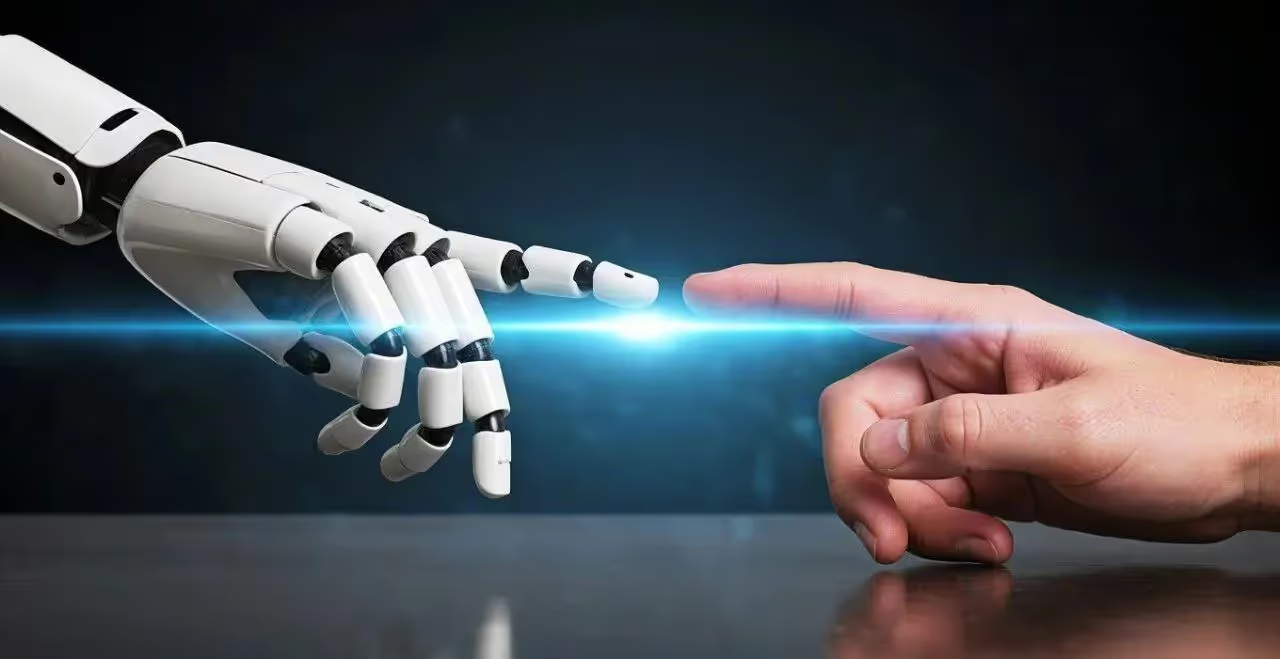
I. What is Embodied Intelligence?
Embodied Intelligence (EI) refers to a form of intelligence in which an intelligent body interacts with its environment in real time through its physical body, thus realising the integration of perception, cognition, decision-making and action. Embodied Intelligence is at the forefront of the artificial intelligence field, and embodied intelligence systems usually have the ability to perceive, cognise, decide and act. The biggest quality of embodied intelligence is that it has the ability to understand, interact, and plan, which makes it more efficient than ordinary robots.
Ⅱ. The Four Core Technologies of Embodied Intelligence
1. Multimodal Perception
Multimodal perception refers to the fact that an intelligent body acquires multi-dimensional information about the external environment through multiple sensors (e.g., visual, auditory, tactile, force, temperature, etc.), and integrates this information through fusion algorithms in order to realise an accurate perception of the surrounding environment.
2. Dynamic Modelling
Dynamic modelling refers to the real-time construction and updating of the intelligent body's cognitive model of the environment, including the geometric structure of the environment, the motion state of the objects, the physical properties and so on. Through dynamic modelling, the intelligent body can accurately understand the current state of the environment as well as the possible change trends, providing a basis for decision-making and planning.
3. Autonomous Decision Making
Autonomous decision-making refers to the intelligent body selecting the optimal behavioural scheme through certain decision-making algorithms according to the perceived environmental information and its own task objectives.
4. Group Collaboration
Group collaboration refers to the exchange of information and collaboration between multiple intelligences to jointly complete complex tasks. Through group collaboration, intelligences can share sensing information, coordinate actions, and divide labour, thus improving the efficiency and success rate of task execution.
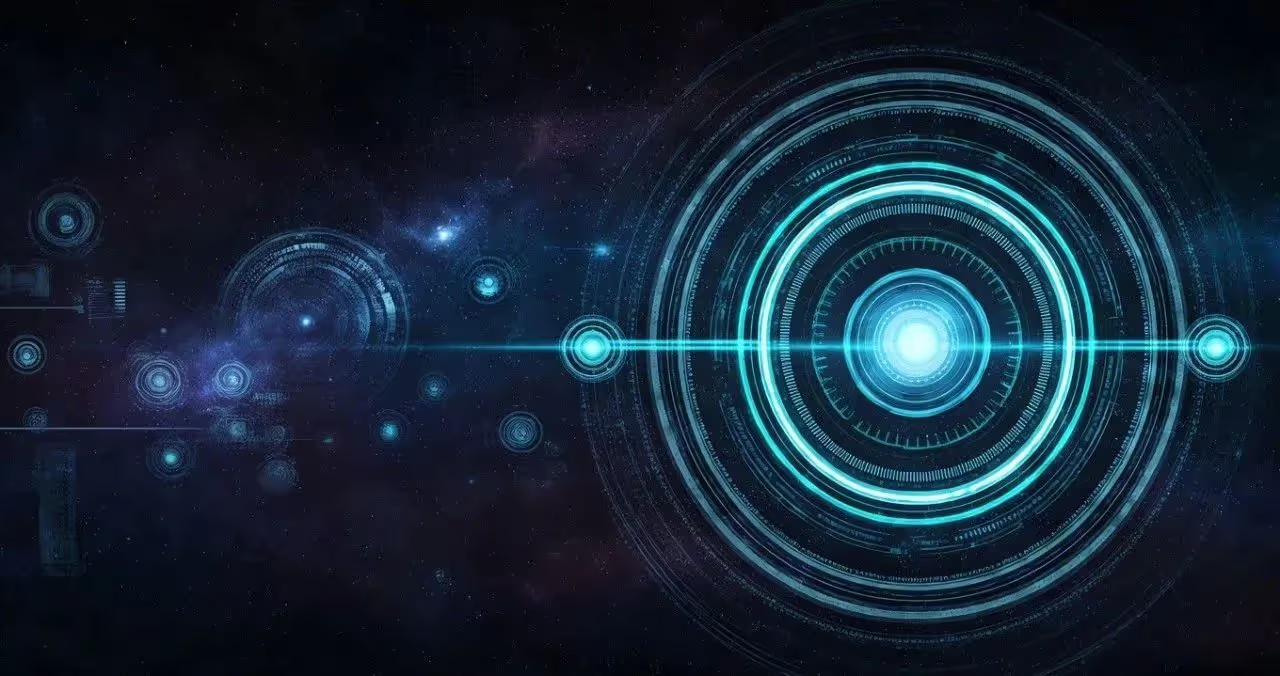
Ⅲ. Application of the Four Core Technologies of Embodied Intelligence in Handling Robots
———AiTEN handling robot as an example.
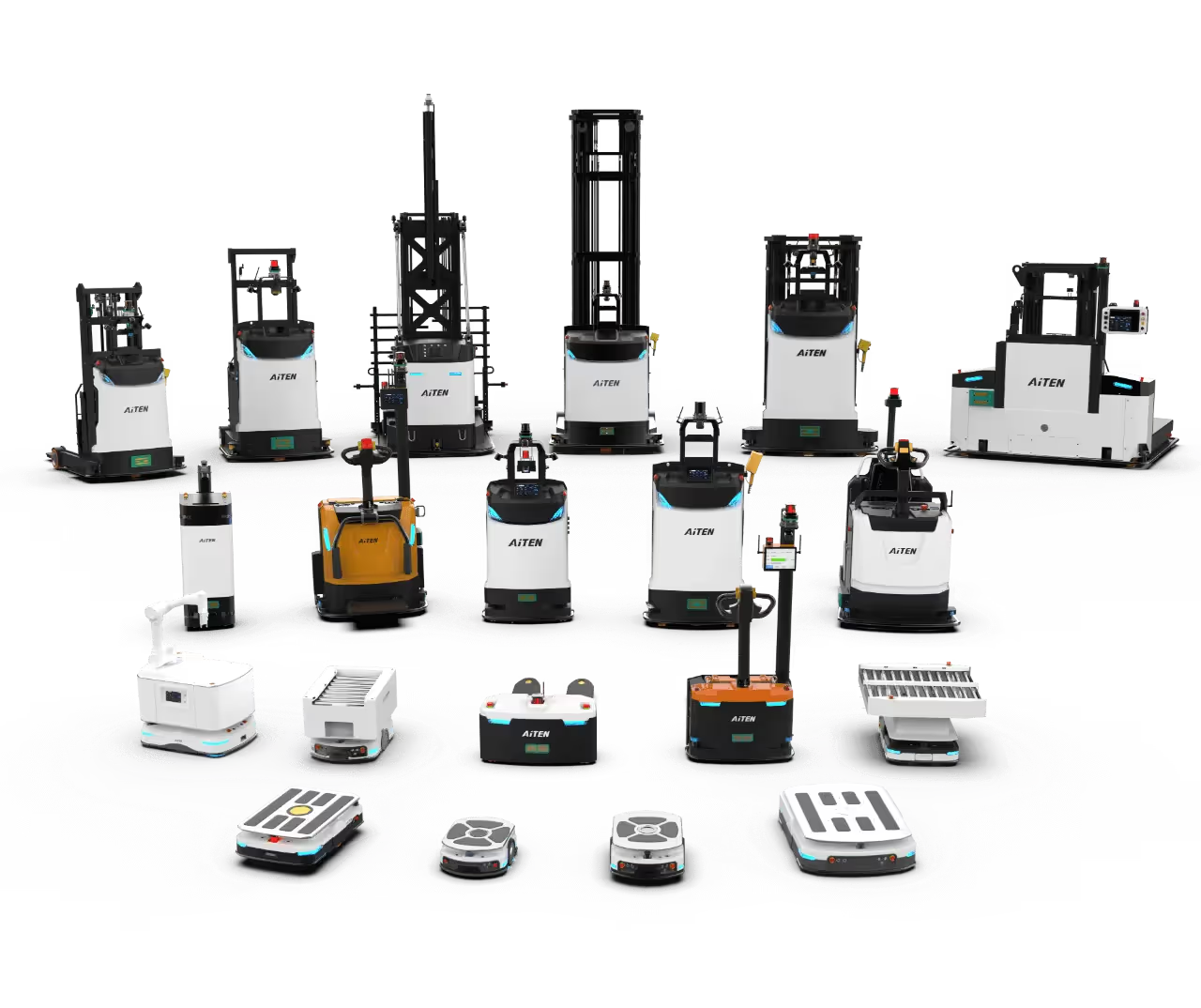
The application of the four core technologies of embodied intelligence - multimodal perception, dynamic modelling, autonomous decision-making and group collaboration - in the field of handling robots has achieved a breakthrough from single-function to full-scene intelligence. Intelligent breakthrough in the whole scene, significantly improving the level of logistics automation. The following AiTEN unmanned forklift as an example, in-depth analysis on specific technology landing and industry cases.
1. Multi-Modal Perception
AiTEN's unmanned forklift adopts the fusion of LIDAR, vision camera and internal sensors to build a three-dimensional sensing capability and achieve all-around monitoring of the complex environment. For example, the APe15 small moving robot integrates AI fusion perception technology based on Lidar and vision, which can accurately respond to complex scenes.
Its core includes:
- Lidar and vision fusion:
The combination of vision and LiDAR is used to achieve ±10mm high-precision positioning and dynamic obstacle avoidance, and the 360° safety radar scans the environment in real time, combines with deep learning algorithms to identify dynamic obstacles, and supports map building navigation, obstacle detection and fork-tip protection, with a safe scanning distance of up to 5 metres, which significantly improves the flexibility and safety of operations in narrow spaces.
- Cargo identification sensor:
Real-time monitoring of cargo weight and centre of gravity through intelligent sensing technology to prevent overloading or tilting. Combined with AI algorithm to judge the gripping strength and path planning to avoid cargo damage.
- 3D Zone Sensing Technology:
Through the combination of ultrasonic sensors and mechanical anti-collision touch edges, it achieves three-dimensional safety protection and significantly improves the accuracy of pallet identification and shelf positioning.
2. Dynamic Modelling
AiTEN unmanned forklift realises the deep integration of the physical environment and virtual simulation through dynamic modelling technology, which supports the unmanned forklift to respond quickly to environmental changes.
- Hybrid navigation: AiTEN Robotics self-developed laser navigation technology combined with dynamic mapping, without the need to lay magnetic strips or positioning points, to support the construction of maps and path optimisation in dynamic scenarios, combined with visual navigation to form a hybrid positioning system, significantly reducing the cost of deployment, while supporting flexible path planning.
- Digital Twin Integration: AiTEN Robotics has launched the ‘WMS+MES+RCS+Digital Twin’ solution, which achieves dynamic modelling and previewing of operational scenarios and optimises the warehousing process through the real-time mapping of virtual simulation and physical equipment. At the same time, the use of a large model base to drive the digital twin system for scene generation improves the robustness and adaptability of the robot to unknown scenes. For example, its AGV unmanned forklift previews the handling path in the virtual environment, and then fine-tunes it with real data to reduce the trial-and-error cost of the actual scene.
- Real-time environment adaptation: AiTEN Robotics' RDS scheduling system supports dynamic avoidance and path adjustment to avoid multi-vehicle congestion; its WCS system achieves collaborative control with lifts, automatic doors, robotic arms and other equipment.
Dynamic modelling technology deeply integrates the physical environment with virtual simulation, reducing trial-and-error costs and supporting flexible production requirements.
In addition, the intelligent control system of AiTEN handling robots can monitor the running status of the robots in real time, such as speed, power, load and other information, and dynamically adjust the motion parameters of the vehicles according to these data to ensure the stable operation of the robots under different working conditions, which is also a manifestation of the dynamic modelling at the control level.
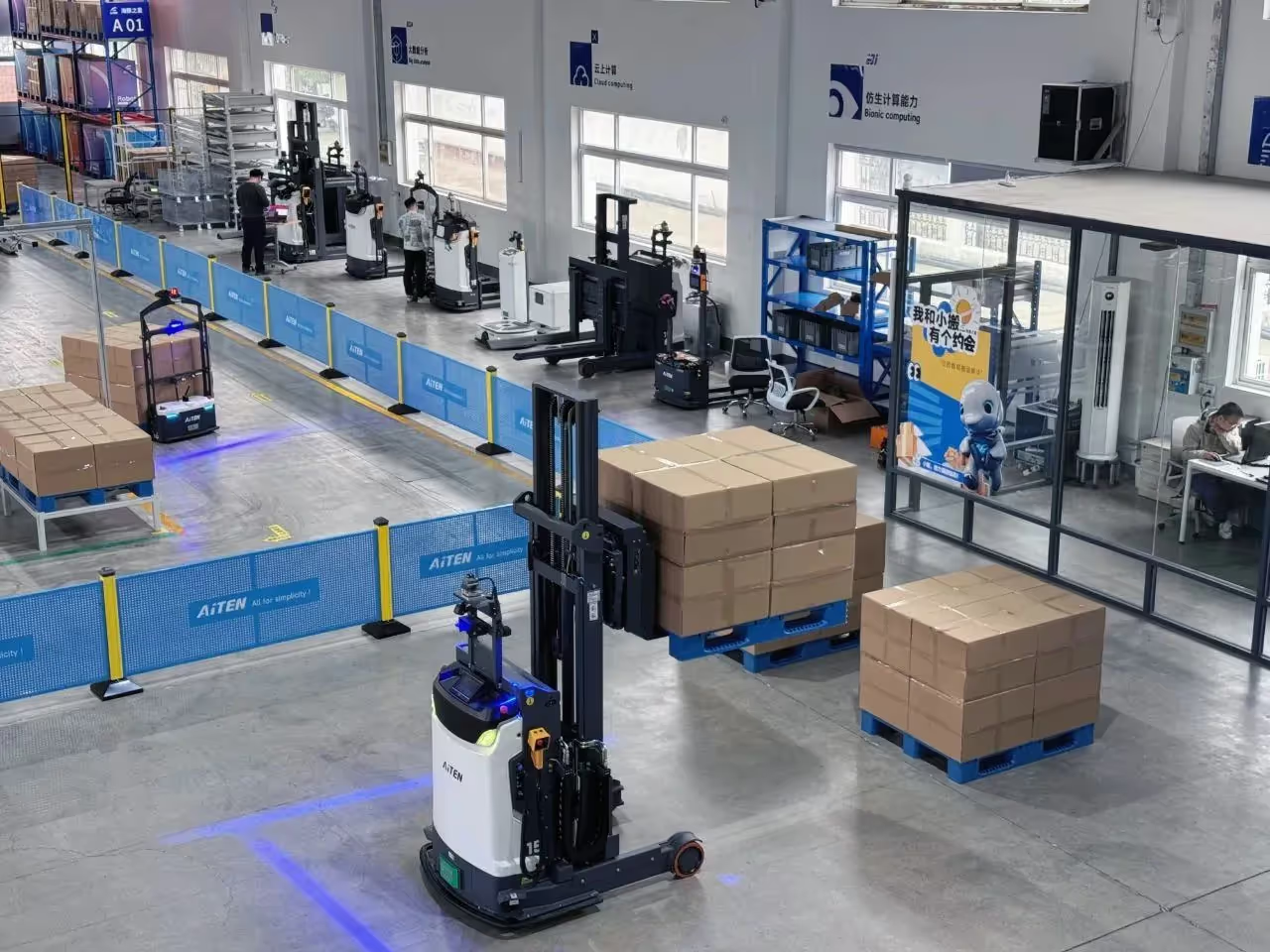
3. Autonomous Decision-Making
The autonomous decision-making ability of handling robots relies on the closed-loop optimisation of AI algorithms and real-time control systems.AiTEN's robots are equipped with advanced intelligent control systems based on deep learning and reinforcement learning algorithms, and can make decisions autonomously based on real-time perceived environmental information and task requirements, such as path planning, obstacle avoidance strategy selection, etc. The robots are also able to make decisions autonomously based on real-time environmental information and task requirements. Its self-developed intelligent scheduling and control system can achieve efficient scheduling and task allocation of multiple robots and optimise the operational efficiency of vehicles. In the face of unexpected situations in complex logistics scenarios, the handling robot vehicle can quickly respond to automatically adjust the running path or take corresponding obstacle avoidance measures to ensure the smooth completion of the task. For example, AiTEN APe15 is equipped with a self-developed AI scheduling algorithm and real-time data analysis system, which can dynamically optimise the paths and loads, and help customers shorten the cycle of cost recovery by 30%.
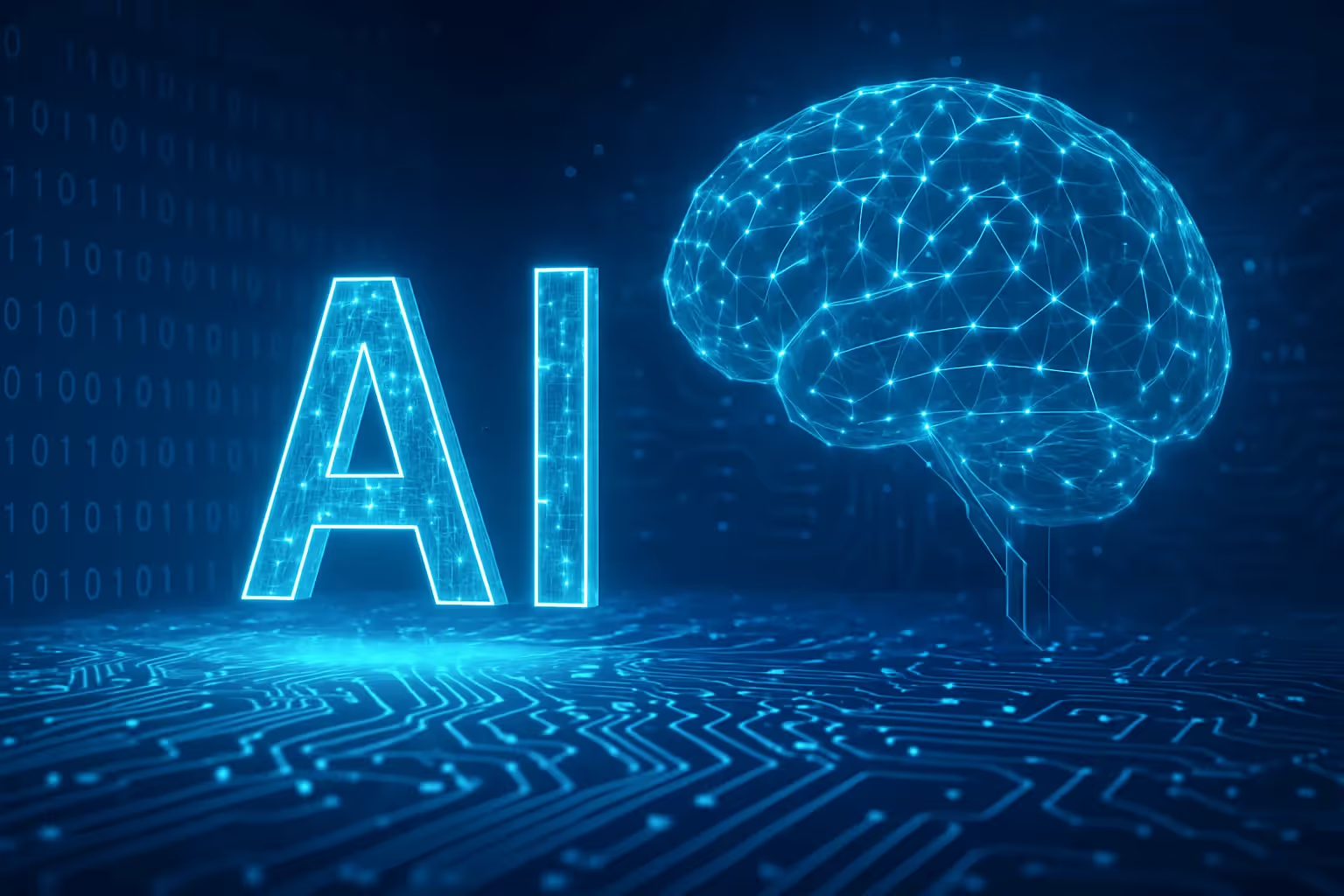
- Path planning and obstacle avoidance: An AI algorithm based on a convolutional neural network (CNN) supports dynamic obstacle avoidance and path replanning, ensuring millimetre-level accurate operation.
- Intelligent operation and maintenance decision-making: analysing the robot's operation status through cloud brain big data, predicting equipment failures and generating maintenance strategies, with a 99.2% accuracy rate of fault diagnosis.
- Multi-task parallel processing: AiTEN robot supports man-machine coexistence mode, which can automatically adjust the work queue according to the task priority, achieving flexible switching in multiple scenarios.
Autonomous decision-making technology has enabled the handling robot car to achieve continuous operation without human intervention in industrial scenarios, and the yield rate has increased to 99.99%.
4. Group Collaboration
AiTEN Robotics realises multi-device collaboration through the group intelligence protocol stack. the RDS intelligent scheduling system, developed by AiTEN Robotics, realises the efficient collaboration of multiple handling robots and other logistics robots. It can monitor the position and status of the robots in real time, reasonably allocate tasks according to the task demand, and coordinate the running path of the robots to avoid collision and congestion. In practice, multiple AiTEN handling robots can work together through the scheduling system to complete complex logistics tasks, improving efficiency and overall operational effectiveness. For example, in warehouses, multiple robots can work together to complete cargo handling, stacking and other tasks to achieve automation and intelligence in logistics.
- Multi-machine Collaboration Algorithm: Developing a distributed scheduling system based on cloud brain computing, supporting hundreds of vehicles to be dispatched on the same site to achieve collaborative operations, achieving dynamic task allocation and resource optimisation through RCS (Robot Control System), and achieving group efficiency up to 15 times that of an artificial team.
- Cross-equipment collaboration: Seamless docking with equipment such as stand-up storage and automated production lines, supporting automatic interaction with robotic arms and conveyor lines to form an all-link intelligent logistics system.
- Global adaptation: Through multi-language instruction parsing technology, it achieves standardised access to transnational warehousing networks and supports global project deployment.
Summary
The application of the four core technologies of Body Intelligence in the handling robot industry promotes the handling robot from a single automation equipment to the ‘perception-decision-making-execution-collaboration’ whole chain of intelligent leap. With the technology iteration and industrial ecological improvement, the handling robot will further release the efficiency potential in manufacturing, warehousing and logistics, and become the core node of the intelligent factory.
As an enterprise in the field of intelligent logistics solutions, AiTEN Robotics always focuses on ‘smart factory’ scenarios, deeply integrates technological innovation and industry demand, and has provided comprehensive services for more than 200 manufacturing customers around the world: relying on the full range of handling robot product matrix to cover diverse handling scenarios, self-developed industry-level intelligent scheduling system to achieve efficient collaboration of multiple equipment, and self-developed industry-level intelligent scheduling system to achieve efficient collaboration of multiple equipment. We have provided comprehensive services to more than 200 manufacturing customers around the world: relying on a full range of handling robots to cover diverse handling scenarios, self-developed industry-level intelligent scheduling system to achieve efficient collaboration of multiple devices, and a full life cycle service system covering pre-sales planning, deployment and implementation to operation and maintenance optimisation, we have assisted enterprises in realising the intelligent transformation of logistics and continued to empower the manufacturing industry in digital upgrading and quality development.