The Advantages of Unmanned Forklifts in the Logistics Industry
.MP10S%E5%8A%A0%E9%AB%98%E6%94%AF%E6%9E%B6-MP10.avif)
In today's rapidly evolving technological landscape, the logistics industry is undergoing profound transformation. As a key component of logistics automation, unmanned forklifts are leveraging their unique advantages to redefine traditional logistics operations gradually. Unmanned forklifts (also known as autonomous forklifts, AGV/AMR forklifts) are increasingly becoming the cornerstone for enhancing warehouse and material handling efficiency. With rising labour costs and growing demand for automation, these intelligent material handling robots are accelerating the replacement of traditional forklifts, thereby reshaping the modern logistics system.
What is an Unmanned Forklift?
An unmanned forklift is an intelligent vehicle that can automatically complete tasks such as material handling, loading and unloading, and transferring without human operation. It usually integrates multiple sensors and control systems such as laser radar, visual recognition, and inertial navigation, and has high-precision path planning and obstacle avoidance capabilities. It is widely used in intelligent warehousing, factory logistics, cold chain transportation, and other scenarios.
What is an autonomous forklift? Revolutionizing warehouse operations
Core Advantages of Unmanned Forklifts in Logistics
1. Improved operational efficiency
Unmanned forklifts can operate continuously 24/7, greatly improving handling efficiency and task completion rates. Programmed control ensures stable operating speeds, avoiding fluctuations in speed and efficiency caused by manual operation, and significantly improving warehouse entry/exit and handling throughput.
Intelligent path planning and scheduling systems ensure forklifts travel along optimal routes, with seamless task handoffs, significantly reducing idle waiting time and improving overall equipment utilisation.
Additionally, unmanned forklifts are equipped with advanced navigation and positioning systems, such as laser SLAM navigation, achieving positioning accuracy of ±10mm, enabling rapid and precise cargo handling and transportation, greatly enhancing operational efficiency.
2. Reduce operating costs
Although purchasing unmanned forklifts requires a certain amount of capital investment in the early stages, in the long run, they can effectively reduce a company's operating costs.
Unmanned forklifts' precise operation avoids damage to goods, collisions with shelves, and equipment wear caused by human error, thereby reducing repair and compensation costs. Predictive maintenance can also extend the service life of the equipment.
Unmanned forklifts are typically designed to be compact with a small turning radius, with some models featuring a turning radius as low as 1040mm (MP10). This allows them to navigate narrow aisles and densely packed shelves with ease, significantly improving warehouse space utilisation. Additionally, their precise positioning and operational capabilities enable tight stacking and efficient storage of goods, meeting businesses' needs for maximising warehouse space utilisation. For example, warehouses using unmanned forklifts can increase storage density by over 30%, enabling the storage of more goods within limited warehouse space.
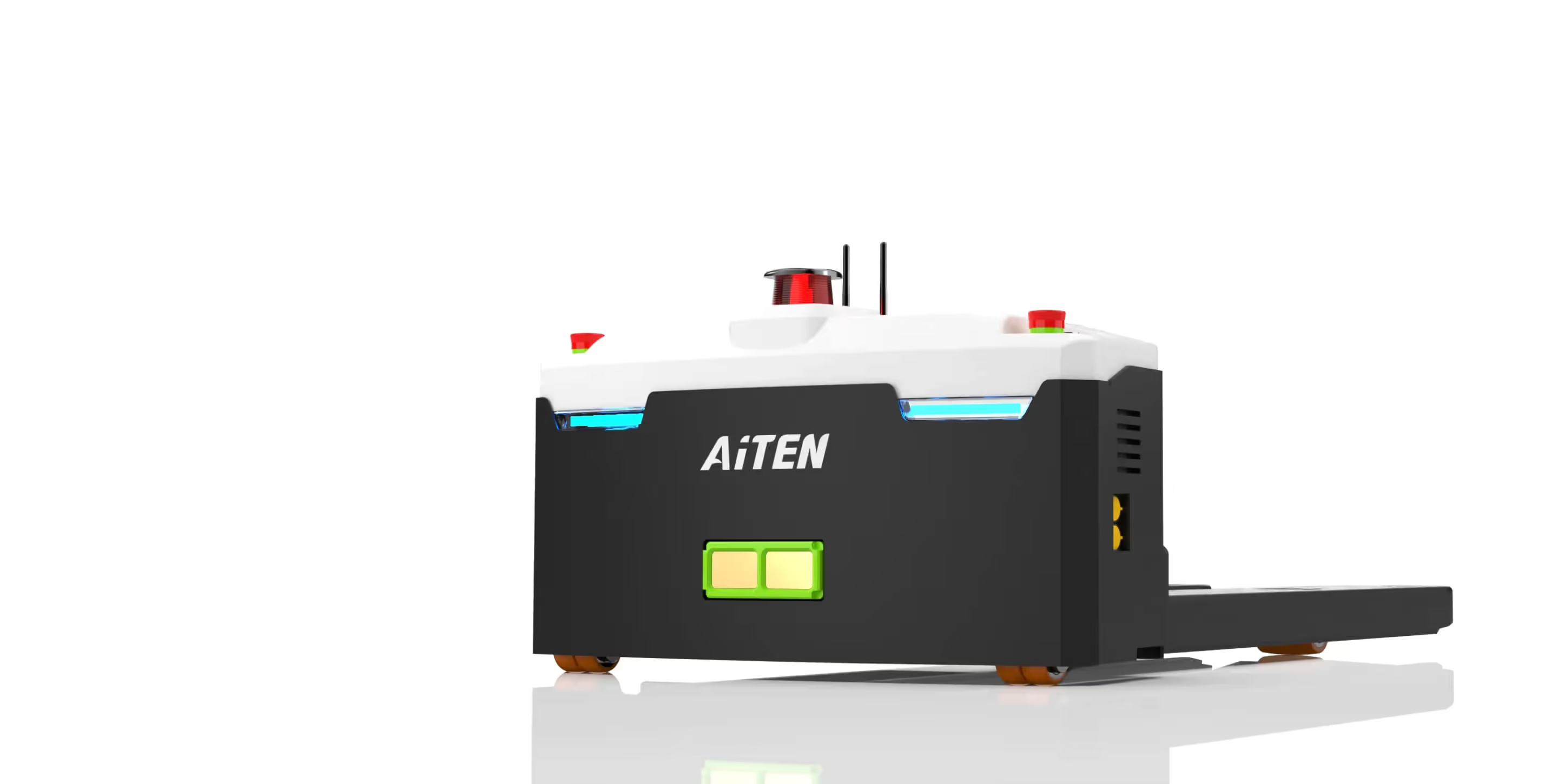
3. Enhancing operational safety
In logistics operations, forklift operations involve certain risks. Manual operations are influenced by factors such as fatigue and mood, making collisions and cargo drops more likely to occur. Unmanned forklifts are equipped with functions such as automatic obstacle avoidance, collision prevention and slow stopping, and safety sensing, which can significantly reduce the risk of personal injury and cargo damage, ensuring safe and orderly operations on site.
- Eliminate human operational risks: Completely avoid accidents caused by fatigue driving, operational errors, and non-compliant operations that result in personal injury and cargo loss
- Intelligent obstacle avoidance and active protection: Integrated with multiple sensors such as laser radar, 3D vision, and ultrasonic sensors, it can detect dynamic obstacles (people, equipment, cargo) in the environment in real time, automatically slow down or stop, and ensure the safety of people, cargo, and equipment.

- Enhanced environmental adaptability: Capable of operating in harsh or hazardous environments such as cold storage, dusty conditions, and low-light environments, ensuring operational continuity and personnel safety in special scenarios.
4. Reduce operational errors
Manual handling is prone to errors such as misplacement, missed picking, and collisions due to factors like fatigue and mood. Unmanned forklifts, equipped with precise positioning systems and task execution algorithms, can achieve millimetre-level docking and accurate handling, significantly reducing error rates and improving overall operational quality.
Precise handling achieves inventory accuracy of 99.9%, with ±10mm repeatable positioning, automatic identification of pallet orientation, and reduced cargo damage.
5. Data-driven management and system integration
Unmanned forklifts can be integrated with WMS, MES, ERP, and other systems to achieve automatic task dispatch, real-time data upload, and visualisation of operational status. They also support remote maintenance and fault prediction, helping enterprises build a data-driven smart logistics system.
- End-to-end digital traceability: Real-time collection and recording of comprehensive data such as handling tasks, travel paths, energy consumption, and equipment status provides a solid basis for process optimisation.
- Seamless integration with intelligent warehouse systems: Deep integration with systems such as WMS, WCS, and ERP enables automatic task assignment, real-time inventory updates, and precise operational coordination, building a flexible intelligent logistics system.
- Supporting lean management: Based on big data analysis, continuously optimise operational processes, resource allocation, and scheduling strategies to drive the lean and intelligent upgrading of warehouse operations.
- Intelligent decision support: Big data supports strategy optimisation and resource allocation decisions, continuously improving warehouse operational processes.
6. Flexible deployment, adaptable to complex environments
Unlike the rigid layout of large automated equipment, unmanned forklifts have flexible deployment capabilities and can quickly adapt to diverse shelf layouts, aisle widths, and process lines. For example, AMRs are suitable for low shelves, while laser navigation forklifts are suitable for high-bay warehouses.
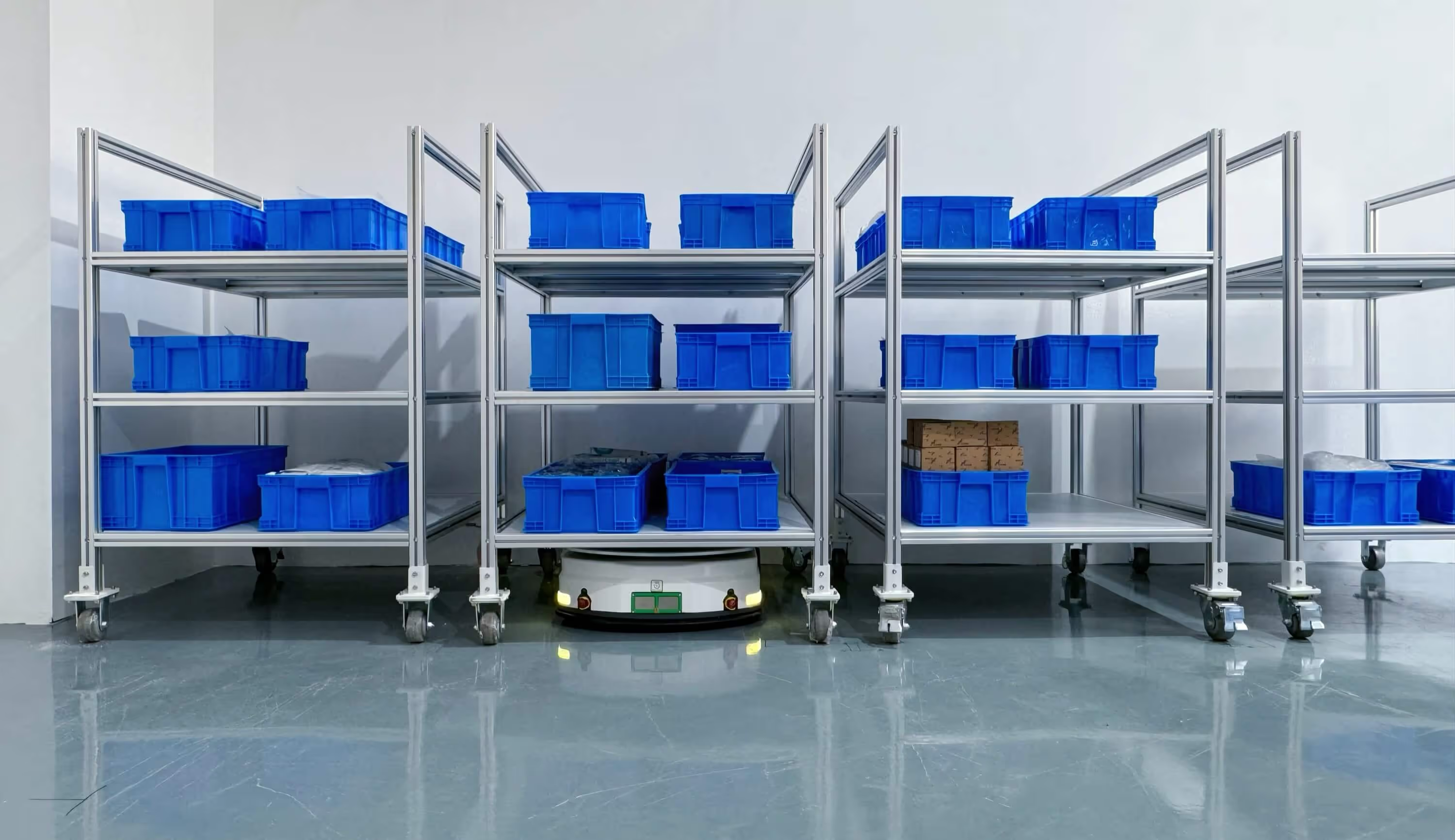
- Modular design, broad application scope: From pallet handling, high-bay stacking to bin handling and production line feeding, AiTEN robots' diverse models meet diverse logistics needs.
- High scalability: The AiTEN system supports flexible adjustment of vehicle numbers and fleet composition based on business growth needs. When production capacity doubles, simply add vehicles without needing to re-plan the warehouse.
- Advanced navigation, flexible adaptation: SLAM (self-localisation and mapping) technology is increasingly mature, eliminating the need for large-scale environmental modifications (such as installing magnetic strips or QR codes). Deployment is quick, path adjustments are flexible, and the system adapts to business changes.
- Supports multiple scenarios: Narrow aisles, low-temperature cold storage (-25°C), and dark environments are all operational.
Typical Application Scenarios
Unmanned forklifts have been deeply integrated into the core processes of modern logistics:
- Raw materials and finished goods warehousing: Efficiently complete transportation, shelving, and fully automated warehousing.
- Production Logistics: Achieve just-in-time (JIT) automatic delivery of materials to production lines, connecting warehousing and manufacturing processes.
- Cross-Floor and Cross-Area Transportation: Interoperate with elevators and automatic doors to achieve automated transportation between multi-level warehouses or factory areas.
AiTEN Robot Cases:
AMK Narrow-Aisle AGVs Power Qianjiang Refrigeration’s Smart Factory Transformation
AiTEN Material Handling Robot in Textile Machinery Manufacturing Application Case
Key Steps in Implementing Unmanned Forklifts
- On-site assessment: aisle width, ground flatness, load-bearing capacity.
- System integration: WMS/MES interface open to ensure real-time task distribution.
- Safety zones: set up dedicated AGV lanes and human-machine mixed traffic warning lights.
- Data monitoring: view vehicle status, battery power, and mileage in real time through the IoT platform.
Conclusion
With the development of AI algorithms, lidar, 5G communications and other technologies, unmanned forklifts will continue to evolve towards high intelligence, coordination and multi-machine scheduling. In the future, it will not only be an automated device, but its comprehensive advantages in efficiency, cost, safety, management and flexibility will provide strong support for enterprises to meet challenges and enhance competitiveness.
Unmanned forklifts not only improve the efficiency and safety of logistics operations, but also drive the transformation of traditional factories and warehouses towards intelligent logistics upgrades. For businesses seeking to reduce costs, enhance efficiency, and achieve digitalised operations, deploying unmanned forklifts is no longer an option but a necessity. As technology continues to advance and mature, unmanned forklifts will undoubtedly find broader application in the logistics industry, driving its ongoing development towards greater intelligence and efficiency.
Are you evaluating how unmanned forklifts can optimise your logistics operations? Contact us immediately to obtain a customised intelligent logistics upgrade solution.
About AiTEN Robotics
As a company specialising in intelligent logistics solutions, AiTEN Robotics has consistently focused on the ‘smart factory’ scenario, deeply integrating technological innovation with industry needs. It has provided comprehensive services to over 200 manufacturing clients worldwide: Leveraging a full range of material handling robot product portfolios to cover diverse material handling scenarios, we have developed an industry-grade intelligent scheduling system to enable efficient collaboration among multiple devices. Through a comprehensive lifecycle service system spanning pre-sales planning, deployment and implementation to operations optimisation, we empower enterprises to achieve logistics intelligence transformation, continuously driving the digital upgrading and high-quality development of the manufacturing industry.
Contact us to explore automation solutions for your factory.