How Much Does an Autonomous Forklift Cost? How Much Is an AGV?
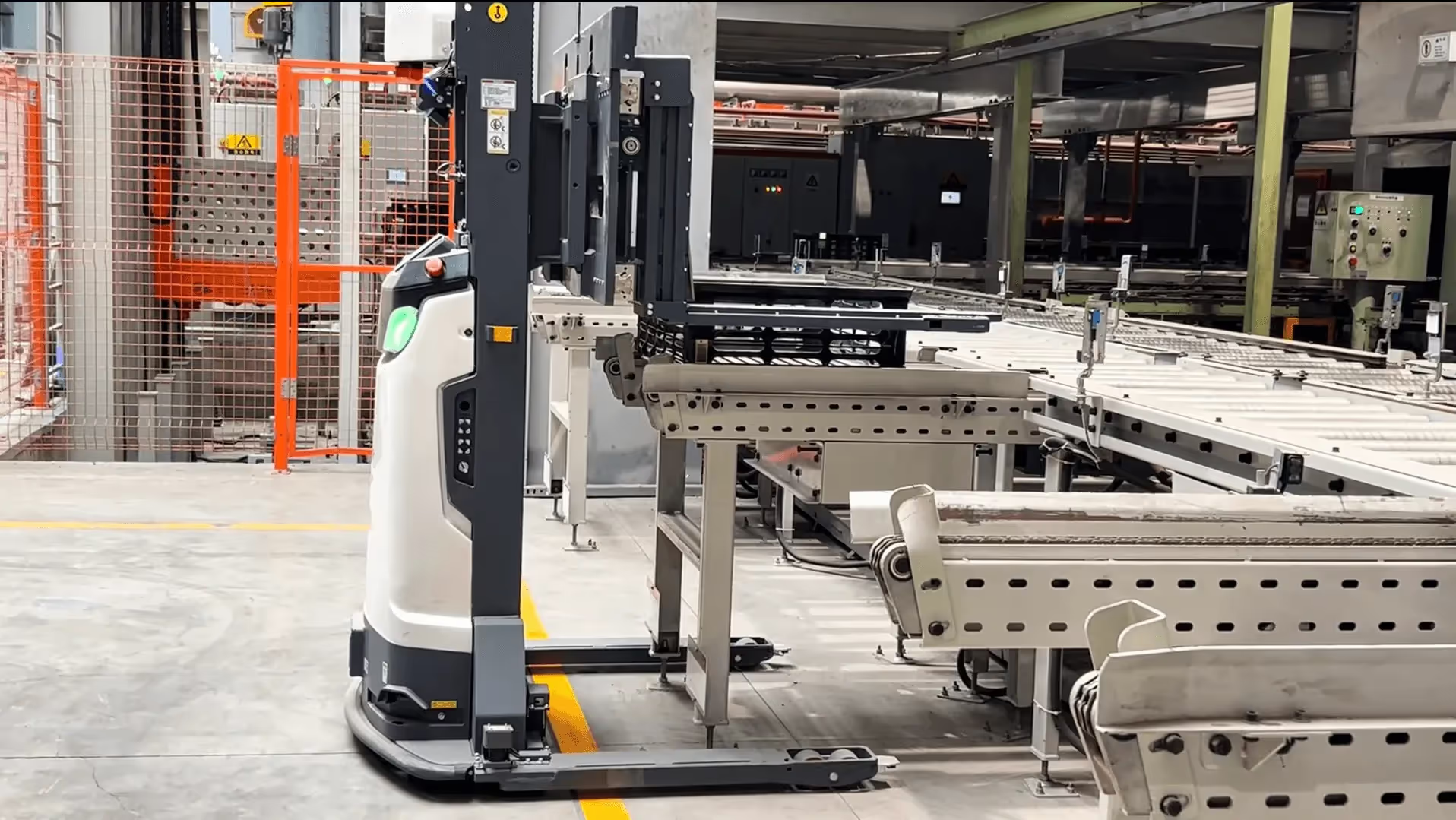
I. The Cost of Autonomous Forklifts
With labour shortages and rising operating costs, more companies are adopting self-driving forklifts to optimise their logistics and warehouse operations. These forklifts can increase efficiency, reduce human error, and improve workplace safety.
I'm sure you already know some of the basics, like what an automated forklift is and the different types of robotic forklifts. But how much do they cost? Let's dive into the price of an automated forklift! From upfront costs to hidden costs, this guide will help you understand this transformative investment.
Ⅱ. What Is the Difference? Automated Forklift vs Fork AGV
An automated forklift is a vehicle that lifts autonomously, and these vehicles often have hybrid capabilities, meaning they can be operated autonomously or driven manually as needed. Automated forklifts are sometimes referred to as Automated Guided Forklifts (AGF), Forklift AGVs, or Driverless Forklifts.
Fork AGVs are Automated Guided Vehicles (AGVs) with forks. These vehicles are designed for automated driving.
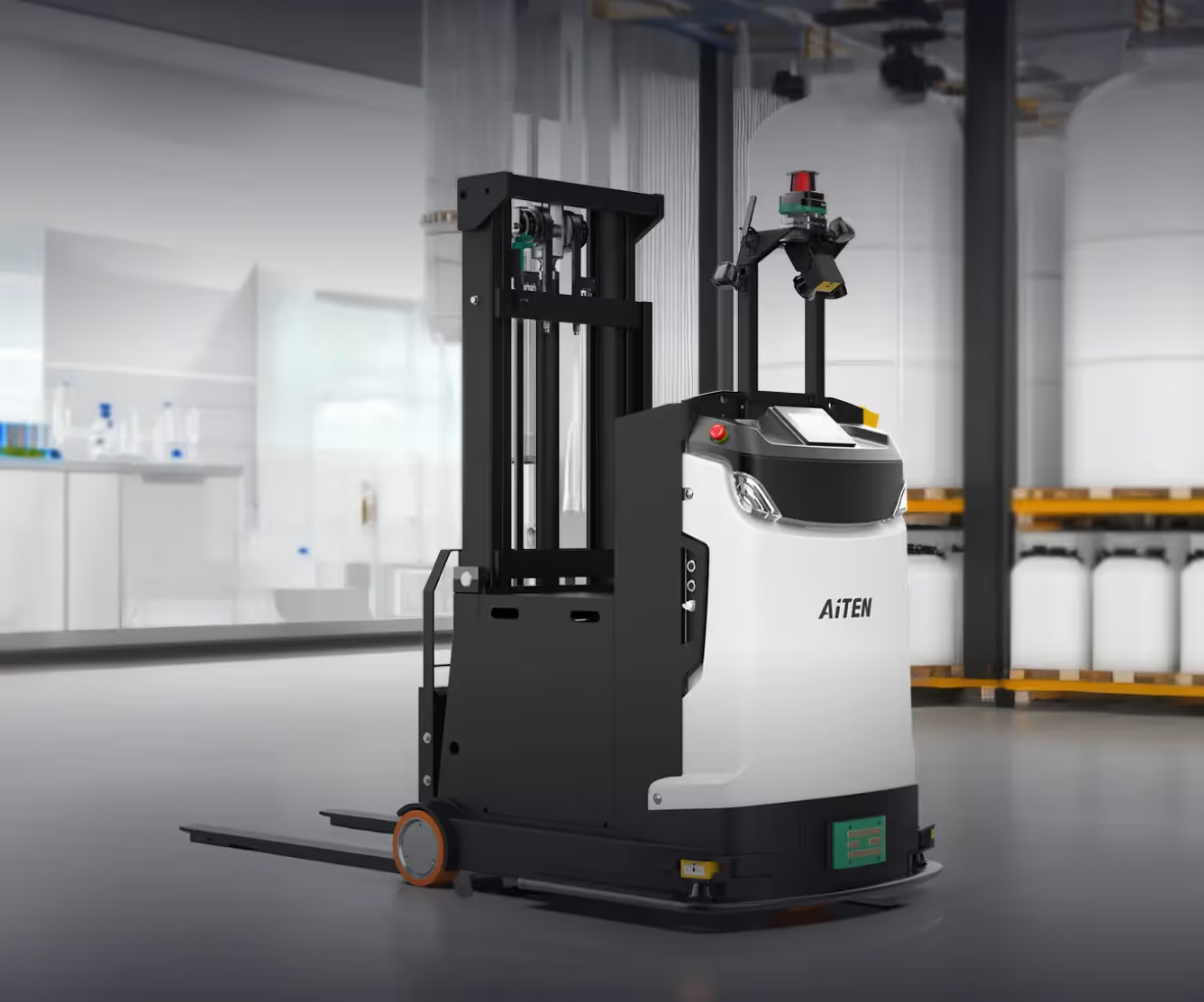
Ⅲ. What Factors Affect the Cost of an Automated Forklift?
Several major factors affect the initial purchase price of an AGV:
1. Payload capacity
How much weight can it carry? The higher the payload, the higher the cost.
2. Lift height
How high can it carry the load? The higher the height, the higher the cost.
3. Navigation technology
The cost of laser, vision, inertial and magnetic navigation systems varies greatly.
4. Software
More powerful and add-on software usually increases the cost (sometimes it is overpowered for the task at hand)
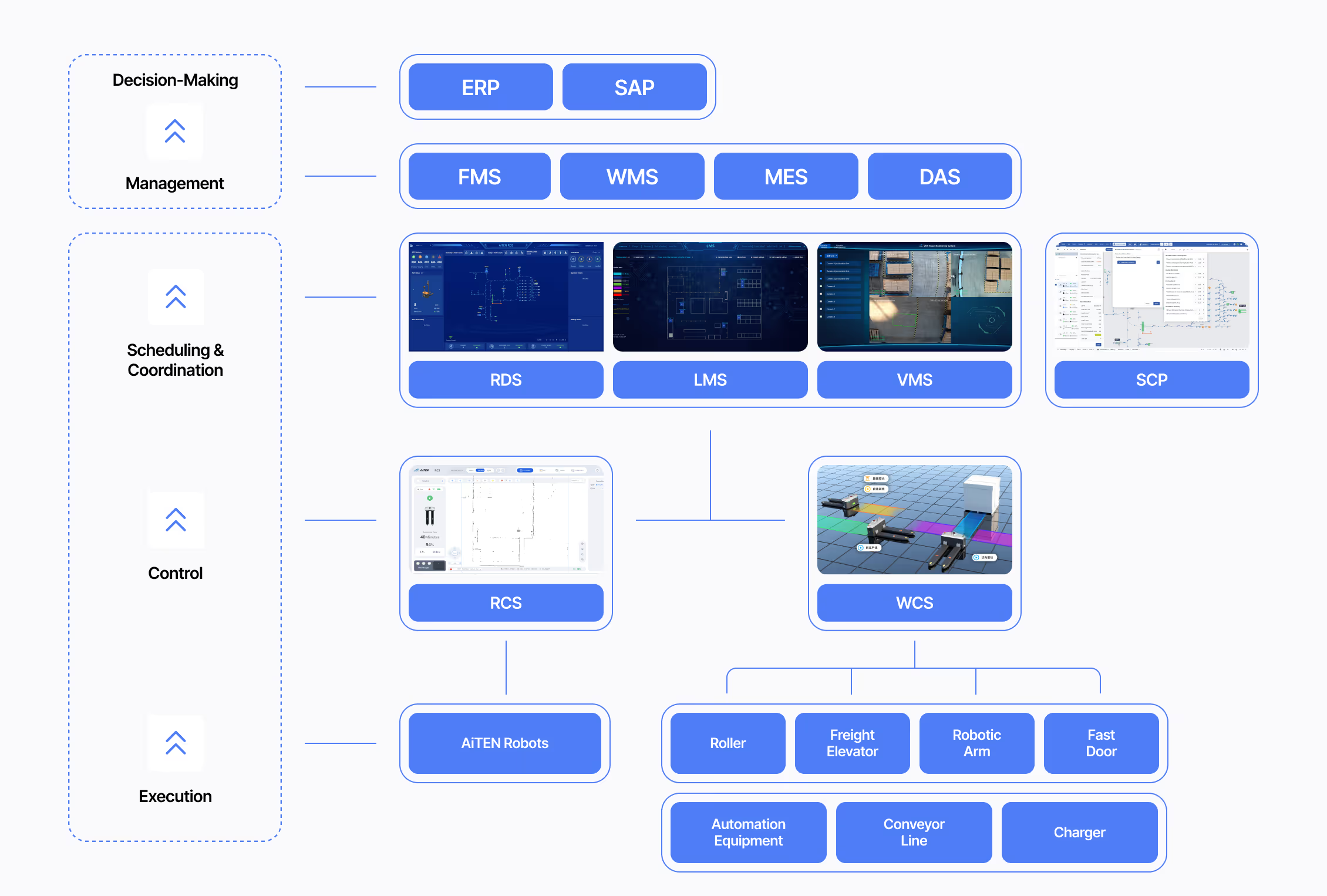
5. Safety systems
There are no mandatory AGV safety standards for self-driving forklifts. In Europe, for example, they only need to comply with the CE marking. This means that a forklift truck from one supplier may be equipped with only 1 safety scanner, while a vehicle from another supplier is equipped with 3 or more safety scanners. Then there are some other protection requirements. For example, if you wish to detect protruding objects above the ground, additional AGV sensors such as LIDAR, ultrasonic sensors or radar may be required, which can increase the cost of the vehicle.
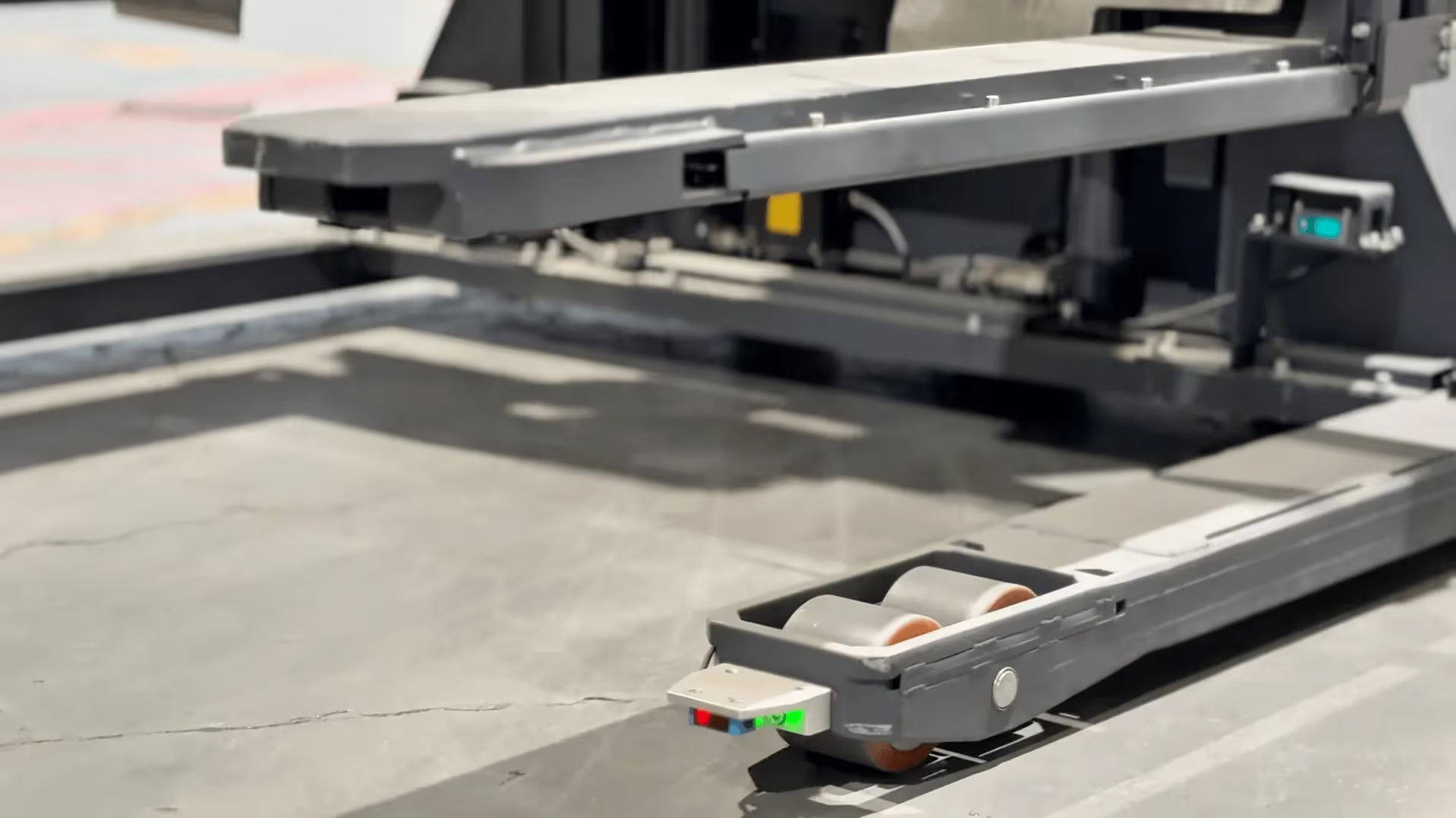
6. Customisation
Integration with existing software systems and specialised profiles or configurations can significantly increase costs.
7. Support options
Technical support, user and maintenance training, maintenance contracts and extended warranties can all add to costs
8. Brand Reputation
Established equipment manufacturers often have higher pricing
Ⅳ. How Much Does an AGV Forklift Cost?
Before investing in AGVs for your factory, there are some key points to consider that affect the cost: how many vehicles are needed? What kind of AGV should be used, and what is the complexity of the installation? What are the vehicle dimensions? What is the load capacity? What is the load capacity? - All of these have an impact on the cost of an AGV installation.
.avif)
In addition to the purchase price, companies should consider the following costs: maintenance and repairs, energy costs, software and integration.
V. How Long Does It Take to Get a Return on the Use of AGV Automated Forklifts?
For factories operating two or three shifts per day, most companies can expect to recoup their initial investment in AGVs within two years. And those plants operating three shifts may be able to fully recoup their investment in less than a year, with some companies even recouping their AGV investment in a matter of months. (Yes, really!)
Key factors affecting payback time include:
- Hours of operation - more shifts lead to faster returns
- Labour costs - higher wages mean quicker break-even points
- Productivity gains - automated systems optimise workflow and eliminate downtime, increased production equals increased revenue
- Safety impact - Reduced risk of accidents, lower insurance costs and improved workplace compliance
- Flexibility - Basic AGVs can be easily redeployed to where they are needed most, increasing the value of agility
- Quality Improvement - Reduced errors and damage increase profits
- Scalability - organisations can expand their fleet without worrying about recruitment challenges.
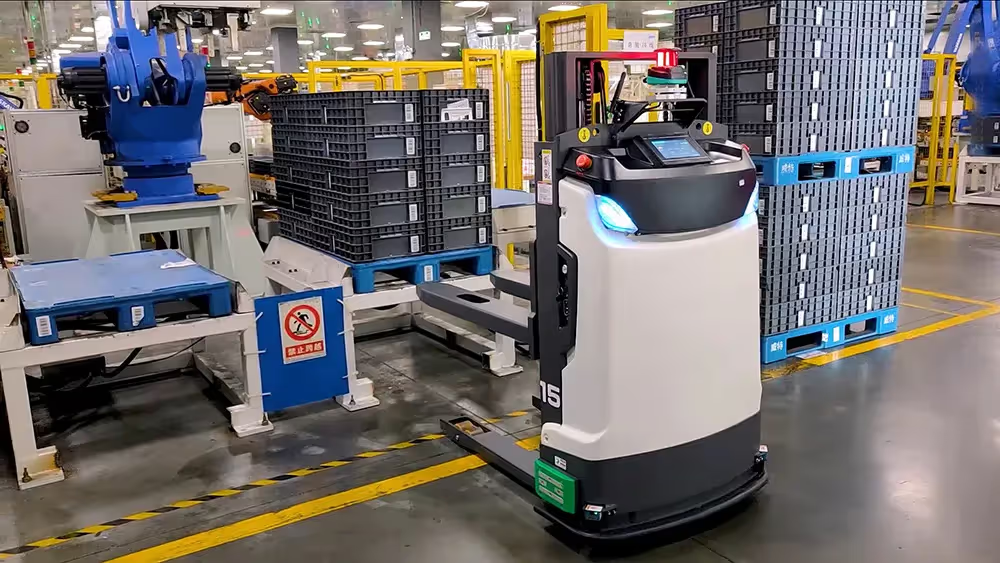
Round-the-clock operation means the AGV continues to move tools, products, materials, bedding, and more even after workers have left work. Workers can return to the production line the next day fully loaded and ready for maximum productivity.
Remember, there are additional costs associated with keeping people on the job. The increased risk of accidents means higher insurance costs - and, of course, actual accidents can cause huge expenses. This makes accident-prone areas, such as blind corners, narrow areas near conveyors and densely packed production lines, an ideal opportunity for automation and a quick return on investment.
Ⅵ. The Application of AGV Automatic Forklift Trucks
The way AGVs are used depends on the use case and the needs of the end user. Most cases focus on transporting, delivering and storing various materials in warehouses, manufacturing and logistics centres. These operations are carried out without human assistance, ensuring that production lines are always managed accurately.
These systems are increasingly used in many industries such as:
- Automotive
- Beverage/Food
- Consumer Goods
- Healthcare/Pharmacy
- Industrial manufacturing
- Retail and e-commerce fulfilment
- Others
Regardless of the industry, innovative navigation systems that enable vehicles to manoeuvre automatically can optimise operational processes.
VII. Will Automated Forklifts Replace Human Operators?
Analysts predict strong growth in the forklift automation market through 2030. However, complete replacement of human operators remains unlikely. Most warehouses will have a mixed model of automated forklifts and certified human operators. Even in automated environments, human supervision will remain critical. U.S. Occupational Safety and Health Administration (OSHA) regulations still require operators to be certified to supervise or manually operate forklifts, whether conventional or automated.
VIII. Conclusion
So sorry I can't provide an accurate price for an automatic forklift because there are so many factors to consider. However, I hope this article has helped you understand. I recommend that you contact AiTEN Robotics for a more detailed analysis.
In the meantime, if your business relies on high-volume material handling, then an automated forklift is a strategic investment that can significantly improve efficiency, reduce operating costs, and ensure long-term scalability.
Ready to discover the right automated forklift for your business? Contact AiTEN Robotics for a free consultation on your needs.