From the AlphaGo Board to Intelligent Handling Robots: How Embodied Intelligence is Breaking Down the Boundaries between Real and Virtual?
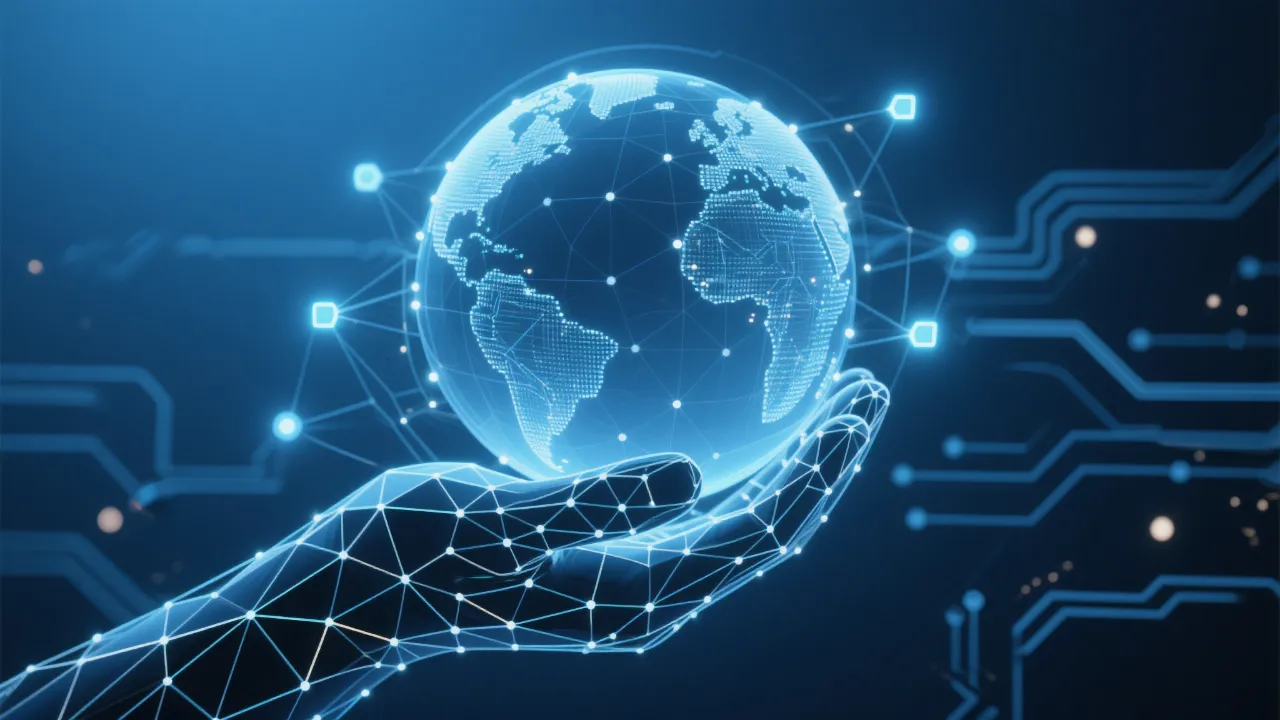
From AlphaGo's chessboard to intelligent handling robots, embodied intelligence reconfigures the boundary between reality and virtuality. AiTEN and other companies have upgraded industrial robots from ‘execution tools’ to ‘cognitive subjects’ through multi-modal perception, dynamic decision-making and group intelligence technologies. In the future, with the in-depth integration of 5G, AI big model and digital twin, embodied intelligence will promote the manufacturing industry to an ‘autonomy, flexibility, low-carbon’ leap, opening a new chapter of Industry 4.0.
Ⅰ. The Evolution of Embodied Intelligence
--Cognitive Leap from Symbolism to Physical Entities
01 The Foundations of Robotics and the Dilemma of Symbolism
In 1950, Alan Turing—widely regarded as the father of artificial intelligence—proposed the idea of embodied intelligence in his seminal paper Computing Machinery and Intelligence. The first mobile robot to implement AI concepts, “Shakey,” was developed between 1956 and 1972 at Stanford Research Institute (now SRI International) under the leadership of Charles Rosen. Controlled remotely by two computers via a wireless system, Shakey’s slow processing power meant it often took hours to sense its environment and plan its movements.
Early robotic systems operated within a symbolic framework, executing simple tasks based on predefined rules. This sequential architecture of “sense-plan-act” proved inflexible in dynamic, real-world environments. The limits of symbolic AI became clear: it lacked true adaptability to external change.
As a result, scholars began to reflect on the limitations of traditional symbolist AI. They gradually realised that intelligence is closely linked to the body and the environment, and cannot rely solely on abstract symbolic operations.
2. Behaviourist breakthroughs and embodied awakening
In 1986, Rodney Brooks, a pioneer of behaviourist robotics, pointed out from a cybernetic perspective that traditional symbolist AI relied too much on complex reasoning systems and ignored the crucial role of body-environment interaction in intelligent behaviour. He proposed the concept of behavioural robotics, which emphasises the removal of representations and promotes the development of embodied intelligence with behaviour at its core, arguing that intelligence is embodied (Embodied) and contextualised (Contextualised). This theory laid the foundation for embodied intelligence and began to influence the field of robotics at the time.
In 1991, Brooks proposed Behaviour-Based AI, which argued that intelligent systems should be highly adaptive by interacting directly with their environment, rather than relying on internal models. This groundbreaking work became a milestone in embodied intelligence, leading researchers to shift from computational power to body-environment interaction, and driving innovation in robotics in terms of adaptability and environmental interaction.
In the 1990s, the Massachusetts Institute of Technology (MIT) in the United States successfully developed a six-legged bionic robot called Genghis, which could rely on sensor feedback to achieve self-adaptive walking, and it was the world's first artificially intelligent robot with the ability of machine perception, reasoning, augmented learning and autonomous behaviour. This achievement marks an important milestone in AI robotics.
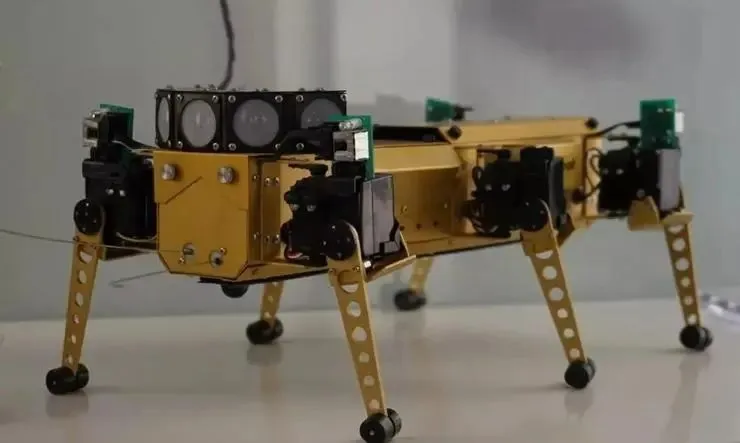
3. Industry 4.0 and the Tipping Point of Virtual Reality Convergence
At the beginning of the 21st century, research on embodied intelligence gradually deepened and extended to the field of human intelligence. Researchers proposed embodied cognition models based on the interaction of perception, action and environment to better understand human cognitive processes. Meanwhile, technological advances in the fields of humanoid and bionic robotics have further advanced the application of embodied intelligence, enabling robots to more realistically address challenges in complex physical environments.
In the 2010s, with the rapid development of deep learning and machine learning technologies, embodied intelligence entered a new phase. Researchers combined deep learning technology with embodied intelligence to give robots the ability to self-explore and adaptive behaviours through deep reinforcement learning, enabling them to self-learn in unknown environments.In 2011, Germany's Industry 4.0 strategy put forward ‘information-physical systems’ (CPS), which requires physical entities and digital models to be deeply In 2011, Germany's Industry 4.0 strategy put forward ‘Information Physical Systems’ (CPS), which requires the deep integration of physical entities and digital models, and the transformation of industrial robots, such as robotic arms, to embodied intelligence to adapt to complex and changing industrial production needs.
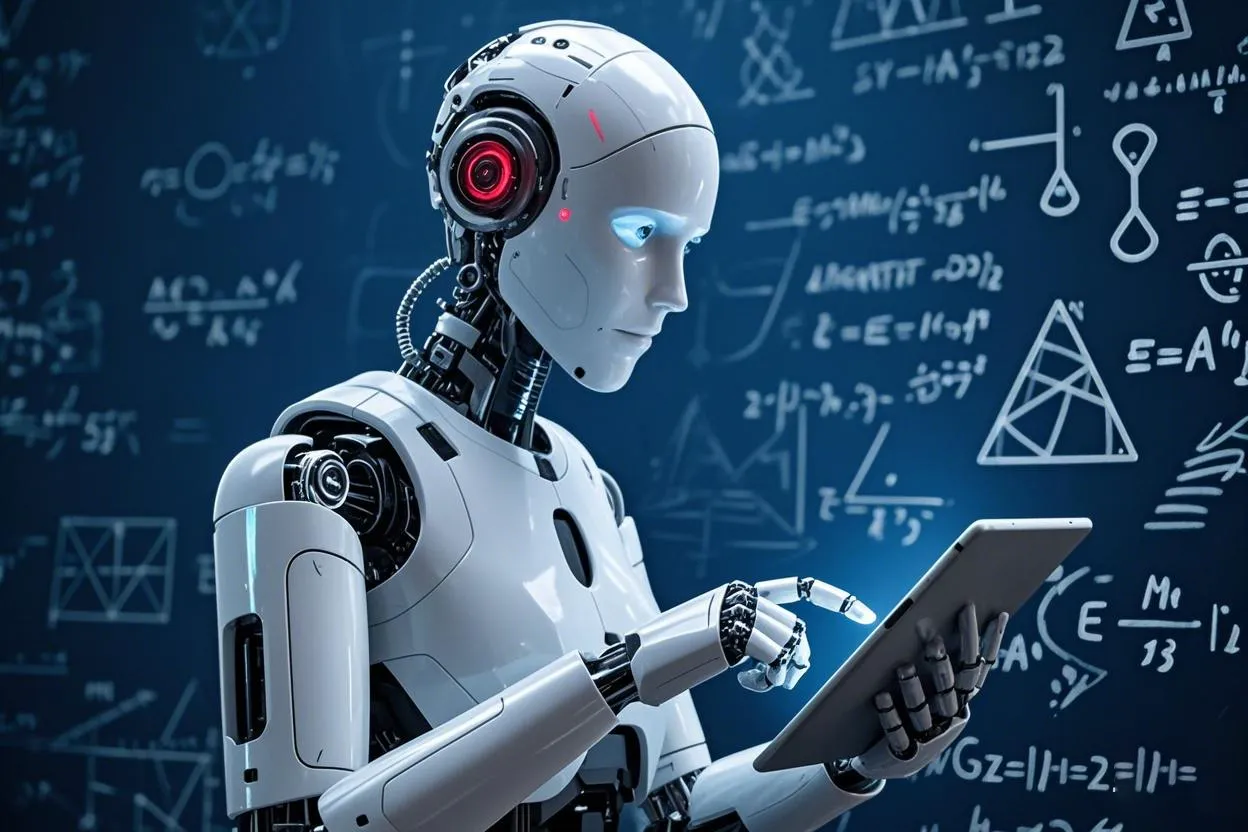
4. The explosion of embodied intelligence: from AlphaGo to physical entities
By the 2020s, embodied intelligence had become an important research direction in AI and robotics.AlphaGo's victory over Lee Sedol in 2016 marked a breakthrough in deep learning in abstract decision-making. However, Go belongs to a ‘closed environment’, while embodied intelligence needs to address physical interactions in open environments.
In March 2024, OpenAI partnered with Figure Inc. to launch the Figure 01 humanoid robot, demonstrating cutting-edge advances in understanding, judgment and self-assessment in embodied intelligence. In October of the same year, the embodied cerebellar model was listed as one of the top 10 cutting-edge technology trends in AI, signalling that embodied intelligence is further combining multimodal perception systems, bionic design and large model technology to equip robots with adaptive and decision-making capabilities closer to humans, and to drive human-robot collaboration into a new future.
II. Technological Breakthrough of Unmanned Forklift Trucks
--Dynamic Obstacle Avoidance and Multi-machine Collaboration in Embodied Practice
1. Introduction
The field of embodied intelligence contains huge market potential and development opportunities. With the continuous maturation of technology and expansion of applications, embodied intelligence products will play an important role in many fields such as smart manufacturing, smart home, smart medical care, and smart services.
Factories and workshops are one of the earliest and most mature application scenarios for robots. Traditional industrial robots (robotic arms) have been widely used in automotive manufacturing, electronics assembly and other fields, but they are mostly fixed-position specialised equipment. And with the addition of body intelligence, it is expected to undertake more flexible and changeable production tasks, as a ‘factory for the general workers’. Warehouses and logistics centres are one of the most cutting-edge battlegrounds for the commercialisation of embodied intelligence. The boom in e-commerce has led to a sharp increase in the demand for automation of warehousing and sorting, and the traditional fixed conveyor belts and AGVs can no longer meet the requirements for flexibility, giving rise to some general-purpose robots that can move around freely in warehouses and carry out handling tasks.
As a pioneer in the field of embodied intelligence, AiTEN takes the independently developed cognitive decision-making technology as the core to break through the problem of autonomous perception and dynamic decision-making of intelligent robots. Its MP10s, APe15 and other unmanned forklifts have been widely used in intelligent manufacturing, intelligent logistics and other scenes. The company has always focused on the ‘technology + scene’ dual-wheel drive, through the AI model and robot depth fusion, to create a full chain of ecology from algorithm development to industrial landing.
2. Dynamic obstacle avoidance: from passive response to active cognition
Unmanned forklift trucks need to perceive the environment during operation. AiTEN's handling robot adopts multimodal heterogeneous sensor fusion technology, which can perceive the environmental information and make cognitive deduction of the environment through model computation, which greatly improves the adaptability to the dynamic and unstructured scene.
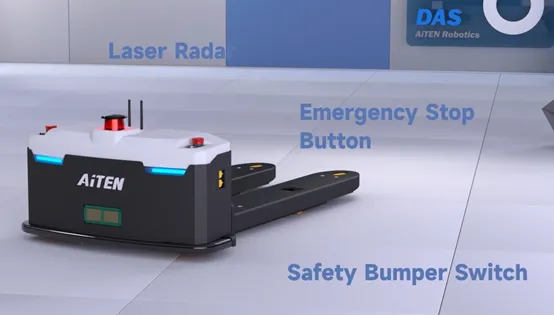
The fork tip sensors are coordinated with the cargo in place sensors to be able to control the accuracy within ±10mm.
In addition, AiTEN's robots support planar 360° safe stopping and forward three-dimensional obstacle avoidance, and can also support recognition of low/overhanging obstacle detection, with fork-tip collision detection, an emergency stop switch and wrapped collision avoidance strips, in line with CE certification.
3. Multi-machine collaboration: from single-machine automation to group intelligence
The central control system, supported by a large model base, allows data analysis and remote control of handling robots. AiTEN's software platform, supported by artificial intelligence calculations, enables automatic assignment and scheduling of tasks, comprehensively improves internal logistics management, supports compatibility with a wide range of equipment and systems, and easily and seamlessly integrates with the existing infrastructure, as well as supporting real-time path planning and collaborative operation of multiple robots to avoid congestion and conflicts, improve operational efficiency and optimise workflows. At the same time, it supports real-time path planning and collaborative operation of multiple robots to avoid congestion and conflicts, improve operational efficiency and optimise workflow.
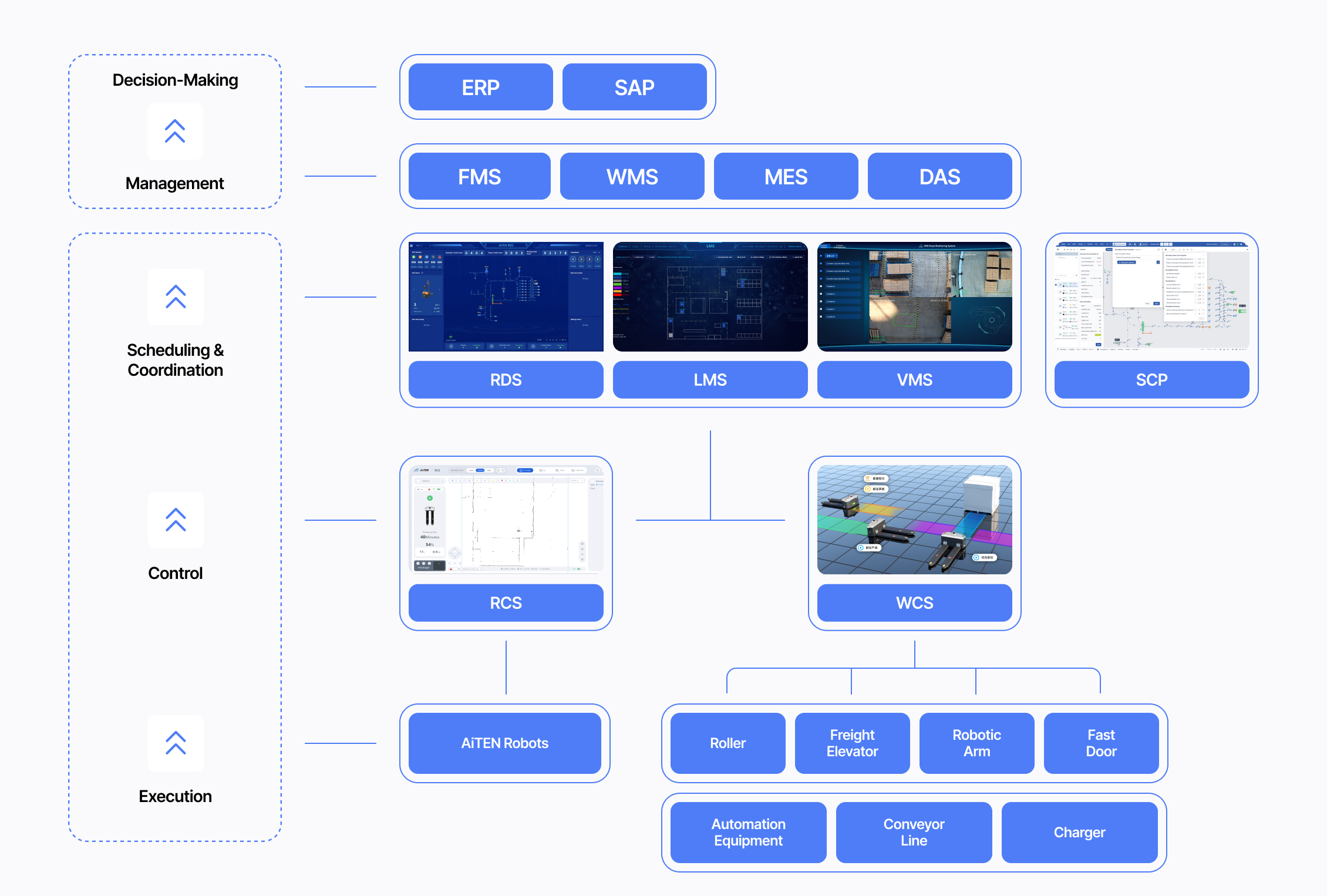
A 3c electronics industry customer, through the introduction of AiTEN robot AR15 and intelligent scheduling system, optimised the internal logistics system, reduced logistics costs, improved production synergy, the overall turnaround time of the product to shorten the product, to protect the product's high quality, large-scale production needs.
Conclusion
From AlphaGo's chessboard to intelligent handling robots, embodied intelligence is reconstructing the boundary between reality and virtuality. AiTEN and other companies have upgraded industrial robots from ‘execution tools’ to ‘cognitive subjects’ through multimodal perception, dynamic decision-making and group intelligence technologies. In the future, with the in-depth integration of 5G, AI big model and digital twin, embodied intelligence will promote the manufacturing industry to an ‘autonomy, flexibility, low-carbon’ leap, opening a new chapter of Industry 4.0.
As an enterprise in the field of intelligent logistics solutions, AiTEN Robotics always focuses on ‘smart factory’ scenarios, deeply integrates technological innovation and industry demand, and has provided comprehensive services for more than 200 manufacturing customers around the world: relying on the full range of handling robot product matrix to cover diverse handling scenarios, self-developed industry-level intelligent scheduling system to achieve efficient collaboration of multiple equipment, and self-developed industry-level intelligent scheduling system to achieve efficient collaboration of multiple equipment. We have provided comprehensive services to more than 200 manufacturing customers around the world: relying on a full range of handling robots to cover diverse handling scenarios, self-developed industry-level intelligent scheduling system to achieve efficient collaboration of multiple devices, and a full life cycle service system covering pre-sales planning, deployment and implementation to operation and maintenance optimisation, we have assisted enterprises in realising the intelligent transformation of logistics and continued to empower the manufacturing industry in digital upgrading and quality development.