Autonomous Forklifts vs Traditional Forklifts: Pros and Cons
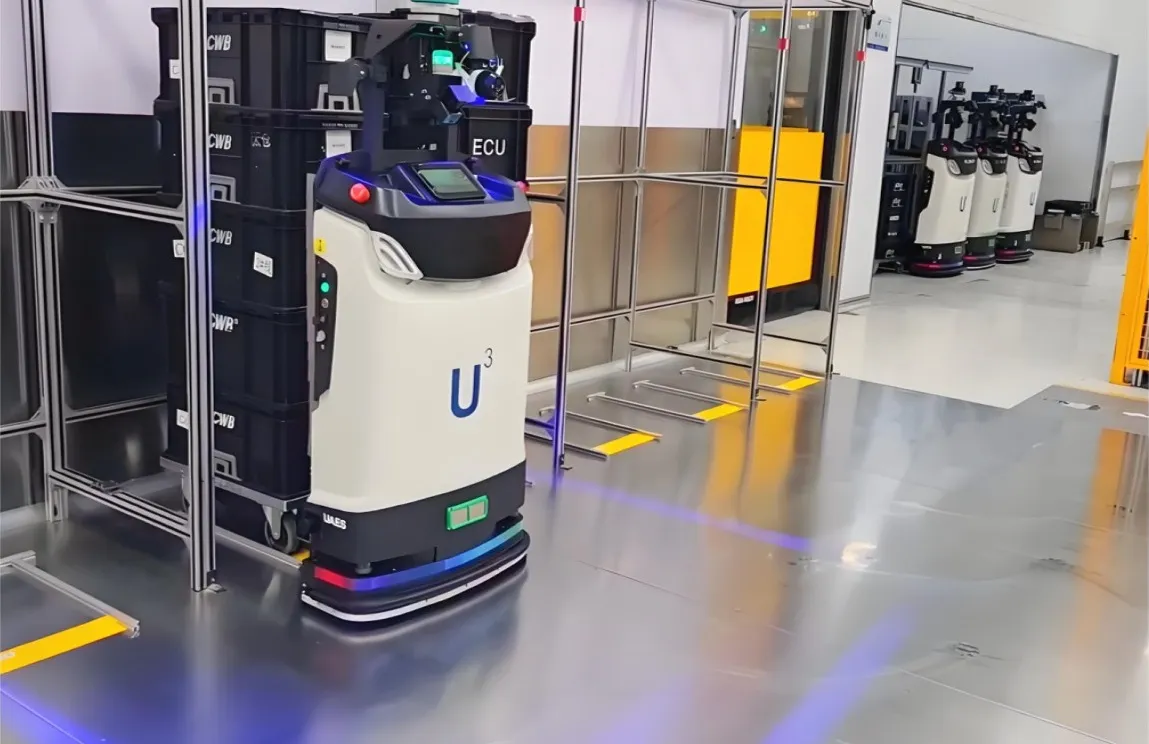
In the evolving landscape of industrial material handling, the choice between autonomous forklifts and traditional forklifts has become a critical decision for warehouses, manufacturing facilities, and logistics centers. While traditional forklifts have long been the backbone of material transport, autonomous forklifts—powered by advanced robotics and AI—are rapidly gaining traction. This article compares their key advantages and disadvantages to help businesses make informed choices.
1. What is an Autonomous Forklift?
An autonomous forklift is a forklift that can navigate, avoid obstacles, and recharge itself automatically. It uses advanced sensors and artificial intelligence (AI) to complete material handling and transport tasks without human intervention. Compared to traditional forklifts, autonomous forklifts offer more efficient and flexible operations.
What Is an Autonomous Forklift? Revolutionizing Warehouse Operations
2. Features of Traditional Forklifts
Traditional forklifts are manually operated, relying on an operator to handle materials. Operators need to be trained and familiar with operating procedures. Moreover, during high-intensity work, human errors can occur, affecting both operational efficiency and safety.
3. Autonomous Forklifts vs Traditional Forklifts
(1)Efficiency and Productivity
- Autonomous Forklifts
(1)24/7 Operation: Unlike human operators who require breaks and shift changes, autonomous forklifts can work continuously, reducing downtime. For example, AiTEN’s AP20 autonomous forklift charges for two hours, with a range of 8 hours of operation.
(2)Precision Navigation: Laser SLAM enables millimeter-level positioning, optimizing space utilization in narrow aisles and reducing collision risks.
图片
(3)Smart Task Scheduling: Integrated with warehouse management systems (WMS), they auto-assign tasks, prioritize workflows, and adapt to real-time changes.
- Traditional Forklifts
(1)Dependent on Operator Skill: Performance varies with driver experience, leading to inconsistent productivity.
(2)Manual Task Handling: Requires human intervention for route planning, load adjustment, and problem-solving, increasing delays.
(2)Safety
- Autonomous Forklifts
(1)360° Safety Systems: Equipped with laser radar, emergency stop button and sensors, they detect obstacles in real time, reducing accidents by up to 90%.
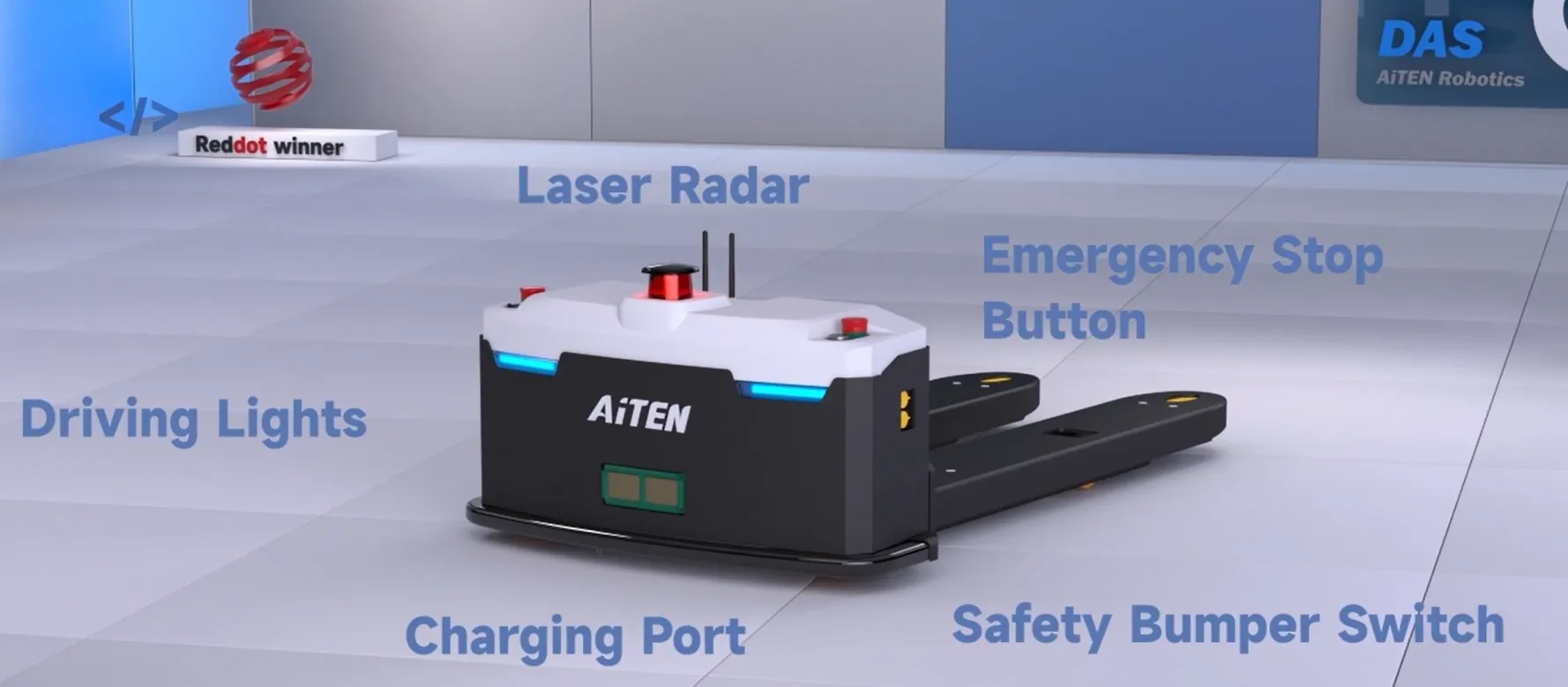
(2)Eliminates Human Error: Removes risks of fatigue, distraction, or misjudgment, critical in high-risk environments like cold storage (-30°C) or chemical warehouses.
- Traditional Forklifts
(1)Higher Accident Rates: Human-driven forklifts account for 25% of warehouse accidents, often due to blind spots or operator error.
(2)Safety Dependent on Training: Requires regular safety training and PPE, adding administrative overhead.
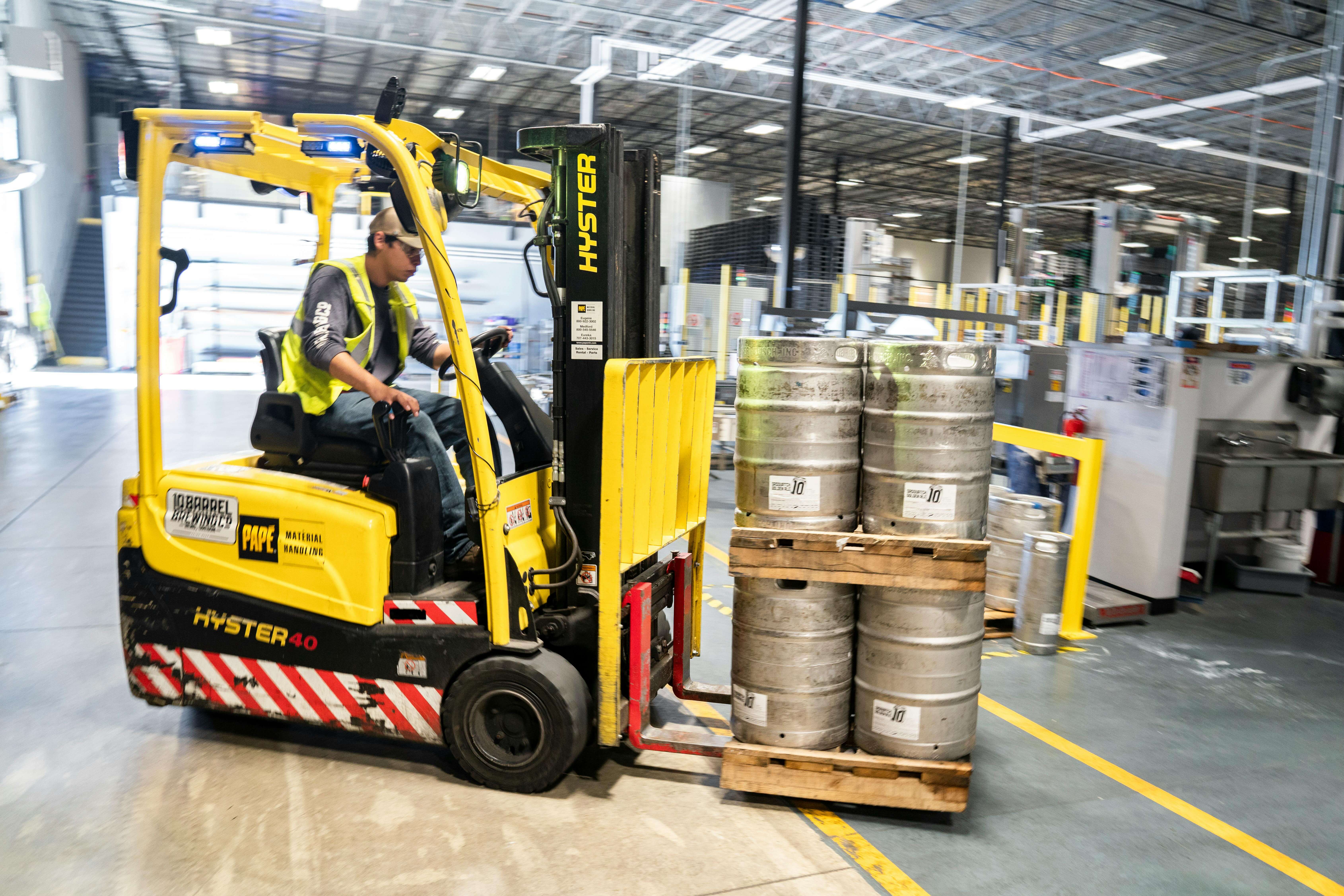
(3)Cost-Effectiveness
- Autonomous Forklifts
(1)Lower Long-Term Costs: While initial investment is higher, they reduce labor costs (eliminating operator salaries) and maintenance expenses (fewer mechanical failures).
(2)Energy Efficiency: Electric-powered models with fast-charging technology consume less energy than diesel/petrol forklifts.
- Traditional Forklifts
(1)Higher Labor Costs: Require skilled operators, increasing payroll and training expenses.
(2)Frequent Maintenance: Mechanical components (engines, hydraulics) need regular servicing, leading to higher downtime and repair costs.
(4)Flexibility and Adaptability
- Autonomous Forklifts
(1)Rapid Deployment: Modern models use plug-and-play software, reducing installation time from weeks to days. AiTEN’s Ape15 forklift adapts to new environments via self-mapping SLAM technology.
(2)Multi-Task Capability: Can handle diverse tasks—pallet handling, container unloading, and even cross-docking—with quick attachments changes.
- Traditional Forklifts
(1)Limited to Fixed Routes: Require manual adjustment for new layouts, making them less suitable for dynamic environments.
(2)Operator Training Needed: New tasks or environments demand retraining, causing delays.
(5)Limitations of Autonomous Forklifts
(1)Technical Dependence: Reliant on stable WIFI/5G networks and accurate environmental mapping; occasional software glitches may occur.
(2)Initial Investment Barrier: High upfront costs can be prohibitive for small businesses.
4. Use Case Analysis
(1)Scenarios Suitable for Autonomous Forklifts
- Large-scale warehouses with 24/7 operations
- Complex environments requiring precision (e.g., pharmaceutical, electronics)
Case Study:
- Businesses aiming for long-term cost savings and automation
(2)Scenarios Suitable for Traditional Forklifts
- Small-scale operations with low throughput
- Temporary or highly variable tasks
- Budgets with strict upfront cost constraints
5. Conclusion
When choosing between autonomous and traditional forklifts, factors like warehouse size, handling needs, and budget play a key role. Autonomous forklifts have clear advantages in efficiency, safety, and flexibility, making them ideal for high-intensity, high-frequency operations. On the other hand, traditional forklifts offer cost benefits and operational simplicity, making them well-suited for smaller warehouses and less frequent tasks.
Ultimately, the decision between the two should be based on an evaluation of your specific needs. Contact us to obtain free feasibility analysis on how to choose a forklift.