AGV Unmanned Forklift Application Guide: Optimising Security and Network Stability
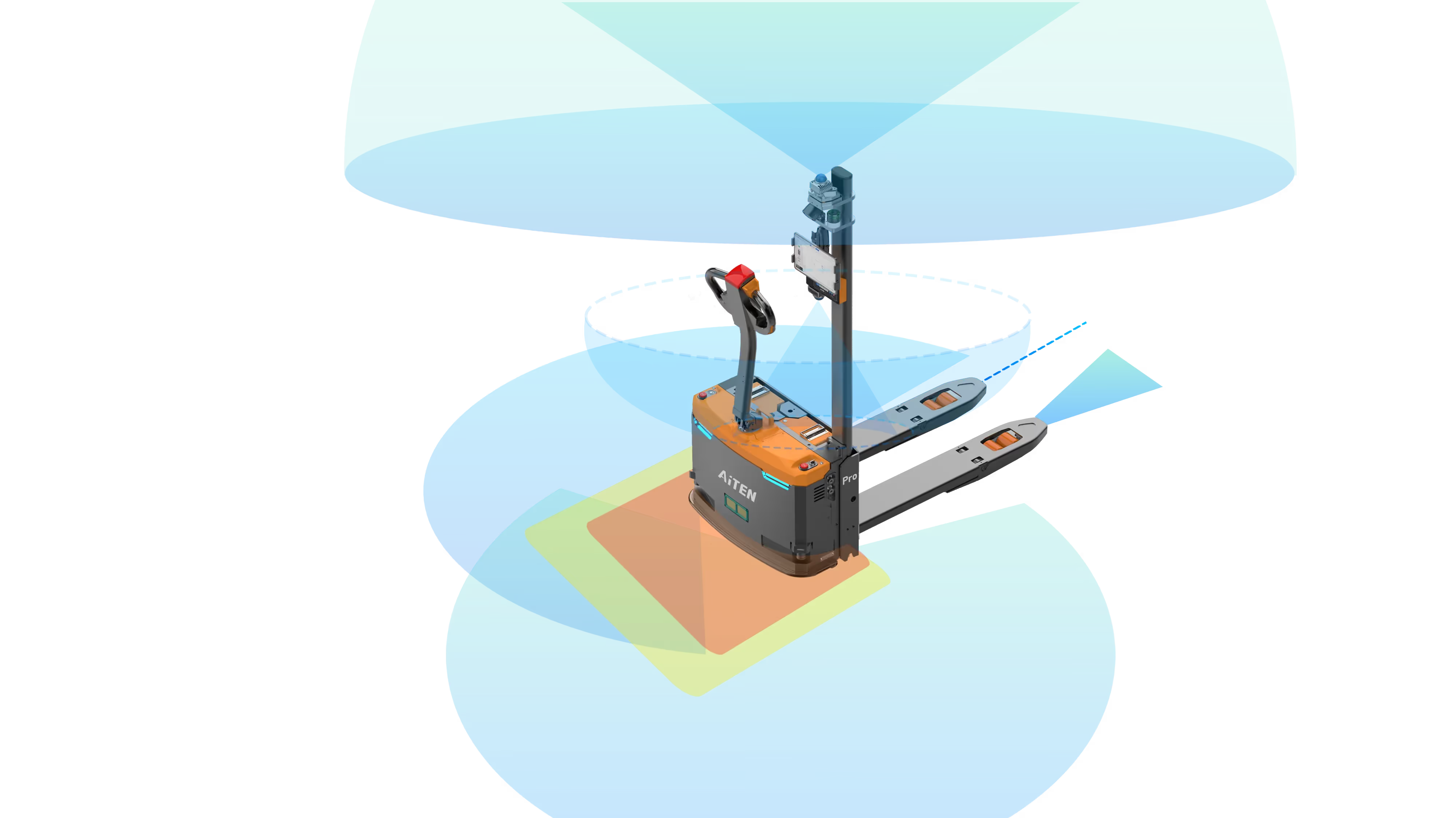
As the core equipment of intelligent manufacturing, AGV unmanned forklift trucks are driving changes in the logistics industry by deepening technological innovation and application. By clearly distinguishing technical concepts, analysing working principles, strengthening safety protection, and optimising network performance, enterprises can fully leverage the capabilities of unmanned AGV forklift trucks and accelerate the realisation of cost reduction, efficiency, and intelligent transformation. In this article, we will introduce the safety protection function and network performance optimisation of the unmanned AGV forklift in detail.
Introduction to AGV Unmanned Forklift Safety and Security
In industrial scenarios, the safety protection system of AGV unmanned forklift trucks is directly related to the safety of personnel, equipment and goods, so its safety design runs through the whole process of hardware, software and operation to ensure the reliability of man-machine co-operation.
1. Multi-Level Obstacle Avoidance and Collision Detection
- Pre-scanning area: The laser radar scans the area 3-5 metres in front of the forklift. When an obstacle is detected, the forklift will decelerate in advance and try to go around it.
- Emergency Braking: If an obstacle enters within 0.5 metres, the AGV forklift stops immediately and alerts the neighbourhood with an audible and visual alarm.
- Mechanical collision avoidance: The body is equipped with elastic collision avoidance strips, which can be triggered to stop the forklift in case of sudden obstacles.
2. Environment Adaptive Design
- Dustproof and waterproof: key components (such as motors and sensors) reach an IP65 protection level, and can operate stably in dusty and oily environments.
- High and Low Temperature Adaptability: Some AGV forklift trucks support extreme temperatures ranging from -20℃ to 50℃, which meets the needs of cold chain warehousing and high-temperature workshops.
3. Redundant System and Fault Tolerance
- Dual Power Backup: The main battery and the backup battery are alternately powered to avoid dropping of goods due to power failure.
- Sensor redundancy: Equipped with LIDAR, camera and ultrasonic sensors to ensure normal operation in case of single sensor failure.
In addition, AGV forklift trucks are required to comply with international safety standards (e.g. ISO 3691-4, ANSI/ITS DF B56.5) and are CE, UL, etc. certified to ensure equipment reliability.
AiTEN Robotics' unmanned AGV forklift products are trustworthy in terms of safety performance. AR15, APe15, AMV10 and other AGVs that can be applied in different scenarios support 360° safety stopping and forward three-dimensional obstacle avoidance, low/overhanging obstacle detection, fork-tip collision detection, emergency-stop switches and wrapped collision avoidance strips, and comply with the CE certification.
AGV Unmanned Forklift Network Issues
Network stability is key to the efficient operation of unmanned AGV forklifts, but in large-scale AGV cluster operations, network dropouts can lead to mission interruptions or equipment loss of control. The following are common problems and solutions.
1. Signal Interference and Inadequate Coverage
Wi-Fi, Bluetooth devices or large metal structures in the factory may interfere with 5G/Wi-Fi signal transmission, Wi-Fi band conflict, metal shelves blocking or APs (Access Points) deployed in insufficient density.
Countermeasure: Adopt 5G frequency band communication, optimise AP layout (suggest deploying 1 AP per 200m2 ), achieve seamless switching between APs, and improve signal coverage and anti-interference capability.
2. High Network Load
When many AGVs transmit data at the same time, the amount of data transmission exceeds the network's carrying capacity, resulting in insufficient bandwidth.
Countermeasure: Process part of the data in the local server to reduce the dependence on cloud transmission, and use TDMA (Time Division Multiple Access) technology to allocate communication time slots, or upgrade to industrial-grade switches to improve network throughput.
3. Protocol Compatibility
The AGV control system does not match the protocol of the host computer (e.g. TCP/IP conflicts with Modbus), resulting in packet loss.
Countermeasure: Uniformly adopt standardised protocols such as OPC UA, and realise data format conversion through middleware to ensure trouble-free multi-device collaboration.
Conclusion
In practice, it is recommended to conduct regular network stress tests and configure redundant communication modules (e.g. dual SIM 4G/5G) to ensure that preset tasks can still be performed offline in case of disconnection.
Ready to explore adapted AGV unmanned forklifts for your business? Contact AiTEN Robotics, and we will provide you with a free consultation based on your needs.